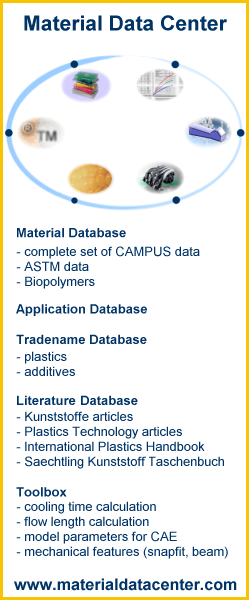
Material datasheets available free. Online registration at: www.materialdatacenter.com
Core - PVC - Avient Corporation
Material Data Center is a leading international information system for the plastics industry. Material Data Center offers a comprehensive plastics database, calculation tools, CAE interfaces, a literature database and an application database. For more information about Material Data Center visit www.materialdatacenter.com.
A search for "Core" in Material Data Center leads to the following information:
|
|
Material Data Center offers information about the following products with the requested tradename. To view a datasheet, please click on the relevant product.
...utive Conference Management. Other innovative technologies presented in the papers include rotating-core tooling that erases weld lines, and a new approach to press-side automation that is truly flexi...
Plastics Technology, 2006-05-04, Smaller EPS Beads Make Thinner Walls In Cups, Casting Patterns and Cushioning
...lity printed graphics. Smaller beads also permit molding more intricate thin-wall patterns for lost-core metal casting. Smaller beads for more intricate shapes are also a trend in resilient protective...
Kunststoffe international, Automotive Display: A Matter of Form
... instrument panel is constructed of three functional layers. The reverse side is formed by a printed film (FIM) with 375 µm thickness, the front side is a 15 µm-thick hard layer, which is applied from a transfer film (IMD). The core of the part consists of 2.1 mm-thick polycarbonate (PC), which is injected between the FIM film and the IMD film at the front. It subsequently remains in the mold under homogeneous pressure and temperatures of initially 300 °C during the cooling phase. Despite the si...
Kunststoffe international, Completely Joined to the Host Computer System
...and monitor our processes better.” That is how Jens Placke, IT Projects, Processes, and Consulting at Böllhoff, responds when asked why the company selected Arburg’s host computer system in 2012. And Placke gives even more reasons: “ALS scored with its short implementation time and readily adaptable integration into the existing IT landscape. This enabled us to switch over quickly from our old PDA system, and the development of interfaces to ERP was trouble-free.” The first step involved network...
Kunststoffe international, Fine Adjustment of the Melt Flows in the Hot Runner by Means of Melt Rotation
...he naturally balanced manifold system and in spite of the symmetrical configuration of the cavities, the melt flows faster to the side facing outwards whereas it lags behind on the side facing the center of the mold. If, as in our example, core shift, uneven temperature control or lacking production quality can be completely or extensively ruled out as a cause of the melt flowing faster sideways, then the question arises whether the effects of shear inside the melt may be the cause.For a full un...
Kunststoffe international, Foamed and Still Extruded in One Step
Foamed polystyrene in window profiles and façade elements can improve their thermal insulation and therefore their environmental efficiency. Simultaneous extrusion of polyvinyl chloride profiles with a PS foam core is challenging due to the different processing conditions and has not been performed before. A trial plant for ‧researching this process has now been set up at the SKZ. The German energy saving regulation (EnEV) of 2014 has placed extra emphasis on the minimization of heat loss and CO...
Kunststoffe international, Formed Pultrusion Profiles
...out the entire forming process (heating, forming, cooling) so that the continuous fibers remain taut at the inner radius and wrinkling is avoided. During the forming process, the remaining, non-pretensioned, continuous fibers are guided by a core and a mantle (each of which is a flexible metal bending spring), so that other typical damage mechanisms such as collapse of the profile cross-section or matrix failure are also avoided. Since the length of the continuous fibers remains constant, they m...
Kunststoffe international, Medical Applications of Additive ‧Manufacturing
...ts inception a challenge but also a necessity for plant and machinery installers to fully tap into the potential of AM, has been extended by now. One of its core points is the direct yield of digital STL files. Nowadays scanners can be used to capture the files directly. This can be done at the patient bedside, but also for conventional parts which are now to be produced using AM. But the digital process chain also happens in another dimension. The operative word here is modern AM plants with co...
Kunststoffe international, New Application Areas for Cube Molds on Standard Machines
...n molding machines with clamping forces ranging from 1000 to 3000 kN only require minimal modification. The Compactcube is based on the cube tool technology Foboha has been successfully deploying for over 25 years. With these tool systems, the core of the mold rotates in four steps by 90° increments. With two parting lines in the mold, the number of cavities can be doubled with the same clamping surface. It is also possible to carry out several production steps such as mold filling, cooling, or ...
Kunststoffe international, Open Control for More Efficiency
...M line from Gabler was transferred for the very first time to a Swing ‧machine, effecting the hoisting/tilting move‧ment using only one motor rather than two. Perfected in an array of diverse applications, the interaction of all core components facilitates a highly flexible production of deeper products such as bowls and cups, but also flat covers and coffee capsules on a single machine, with optional horizontal or vertical stacking at the outlet. This flexibility is supported by an integrated t...
Kunststoffe international, Polypropylene Beats Aluminum
...Structure with UD Tapes The technical solution lies in a sandwich structure known as ElroSafe. This uses UD tapes for the outer layers, because of their lower density, and a direct long fiber thermoplastic (DLFT) as the core material. In this way, through higher wall thickness, the required structural stiffness can be obtained for the same areal weight. Comparative calculations and validation tests show that with a 5 mm-thick sandwich comprising 1.5 mm outer layers made from UD tapes and a 2 mm ...
Kunststoffe international, Reactive Extrusion of TPU
...o reducing the CO2 footprint is the efficient replacement of precursors derived from fossil sources with renewable materials. In the “Dream Polyols” project, a consortium including Fraunhofer ICT has addressed this issue by replacing the core of a standard polyether polyol with a paraformaldehyde block (pFA), resulting in a triblock structure with a potentially significant content of renewable raw materials. The use of pFA from renewable sources opens a path to chemical intermediates that consis...
Kunststoffe international, Real-Time Process Monitoring in Cleanroom Environments
...ts, which are realized for example in compression molds and electric valve gate systems. For example, Schöttli has designed and manufactured a 72+72 cavity stack mold for a medical locking cone, which ensures the unscrewing movement of the thread cores and demolding through ejection sleeves via four individually controlled electric drives (Fig. 1). Challenging Control Technology Dynamic mold movements impose high demands on the regulation and control technology of the actuators. The acceleratio...
Kunststoffe international, Recycling that Gets under the Skin
...chwertberg, Austria, is contributing to this goal by offering a special injection molding process. The machine manufacturer and system supplier has developed the two-component skinmelt process for manufacturing sandwich parts, which have a core of reprocessed plastic wastes and a surface of virgin material. The new feature is that a high content of recycled material can be achieved even with complex part geometries. The new process was unveiled at K 2019 with the manufacture of transport crates ...
Kunststoffe international, Replacing Metal in the Gearbox
...cts would have an unfavorable fiber orientation, because the tensile strength is always greatest in the direction of the fibers. The solution was to use carbon rovings wrapped around a core of suitable diameter and embedded in a matrix of epoxy resin. Each fiber was only 5 to 9 µm thick and a million windings were needed to achieve an insert cross-section of 6 x 8 mm (Fig. 3). Various fiber orientations around the core were also tested virtually, with an angle of 0° ultimately proving to yield t...
Kunststoffe international, The Core Questions of Digital Transformation
© private© private© privateThose who know how to use data understand their business. Simple as that may sound, it is no easy matter for manufacturers to find out what data they must select and process in what way. And most importantly – what for? Do we want to increase productivity, improve monitoring of product quality or reassess our business models? Without a clear goal and implementation strategy, it is something of a lottery whether, following a digital makeover, a company hits the jackpot ...
Kunststoffe international, The One that Shears, Splits, and Folds Material
...le, for example, electrically conductive carbon blacks. Very high filler contents of up to 90 % can also be worked in. Besides complete axial cleaning (Fig. 4) by the array of kneading pins, the core ‧diameter of the screw shaft is scraped closely. Thus, the pins act much like the second or neighboring screw of a twin- or multi-screw extruder. The scraping and cleaning of all surfaces in the processing section, as shown in Figure 5, eliminates deposits and dead spots. The results include operat...
Kunststoffe international, Zero-Waste Concept for Carbon SMC
... respect to one another. In the optimized process, therefore, before the actual press forming, the system is subject to a low pressure of approx. 8 bar for about 15 s until the stack reaches a core temperature of at least 60 °C. In addition, the pressing force is increased to cause the material to flow during subsequent pressing. A graph illustrates the profile of the cavity pressure during the curing time. The reference material is shown in green and the recycled material in orange (Fig. 6). Du...
Kunststoffe international, 2005-11-21, 30 Years of Playmobil: Investing in the Future
...trategy will be deployed to further communicate the attractiveness of Playmobil and to boost demand. Approximately EUR 11 million has been earmarked for sales promotion. The company believes that a further factor in its success is a focus on core business. This entails accommodating real-life themes (Fig. 2), inspiration drawn from children’s wish-lists (Fig. 3) and supplying toys that are fun to play with and that excite children’s imagination and increase their motor skills. Around 50 people w...
Kunststoffe international, 2005-11-21, 3D Simulation: Simulation of Foaming Polyurethanes
...determines the amount of heat released, as expressed in a corresponding increase in temperature. Because of convection as well as thermal conduction in the foam and into mould cavity walls, the temperature distribution in the foam varies. Thus, core temperatures are usually higher, while temperatures near the boundary regions are lower. Since the reaction rate and change in temperature are closely linked to one another, the reaction conversion varies locally. The model for expansion of the PU f...
Kunststoffe international, 2005-11-21, A Commonsense Quota System
...s [1] has been in force since 21.10.2000. Its aim is to lay down uniform minimum standards for environmentally sound treatment of end-of-life vehicles (ELVs) throughout Europe. The reuse of components and material recycling are understood to be the core characteristics in terms of environmental soundness. For this reason, the Directive lays down recycling quotas for promoting the recycling of non-metals, and limits the energy recovery. The costs of uneconomical ELV recovery are to be borne by th...
Kunststoffe international, 2005-11-21, A Comparison of Hybrid Machines
...ning the clamping unit to be torsion free, with reinforced platens and tie-bars, as well as providing high-performance plasticization screws. The main priority is to improve the drive technology as a whole. Rapid, parallel movement of clamping unit, core pullers, ejectors and metering operation, as well as high injection capacity and dynamic response are requirements that an intelligent combination of different drive technologies can meet with energetic efficiency, quietness of operation and ext...
Kunststoffe international, 2005-11-21, A Comparison of Temperature Control Systems: Optimum Thermal Design of Injection Moulds
...uch methods rapidly be-comes apparent when problems such as inadequate surface quality or sink marks appear. The desired cycle times are often not achieved because of poorly cooled “hot spots” in the mould. Here – for exam-ple in the region of cores, slides, fillets or corners – a small amount of mould material has to cool a large amount of plastic. Various Cooling Concepts in Competition For the thermal design of an injection mould, various technical con-cepts have been available for years wi...
Kunststoffe international, 2005-11-21, A Demanding Body Care Set
...slides are required, with three star-shaped slides alone needed for the four snap hooks that fasten the cover (Fig.3). The housing interior and the undercut for the bore of the pressure setting switch of the Visapure luxury model are formed by a core puller with a mounted crank-operated drag slide (Fig.4). The opening for the drive shaft is achieved by demoulding a core at the ejector side, which is moved by means of a core-puller slide, and an upwardly angled, externally running core-puller sli...
Kunststoffe international, 2005-11-21, A New Pilot Plant: Customer Trials Required
... trimmer can be set for 4 x 500mm or 5 x 400mm wide rolls. Thanks to the fully automatic turret winder (type: 1027-S, manufacturer: Battenfeld), accurate reels with a diameter of up to 600mm can be produced on 76mm shafts. An automatic core feeding and reel removal system simplifies handling, as does the centralised Extrol control of the entire production line. Multilayer Blown-film Line Customer trials have already been carried out out the blown-film line since September 2002. The extrusion p...
Kunststoffe international, 2005-11-21, A Short Time-To-Market Process
...t series can be made available already after one or two weeks. Integrated Front-End Modules Directly from CAD In the joint venture Hella Behr Fahrzeugsysteme GmbH run by Hella KG, Lippstadt, and Behr, Stuttgart, the companies want to combine their core competencies for co-operative development of integral front-end modules for motor vehicles. The advantages of integrated front-end modules could be demonstrated using a prototype in the context of the development study. By integrating the hybrid...
Kunststoffe international, 2005-11-21, Acceleration is Not Everything
...cleaves readily to the ejectors. If the injection moulding machine features double-pump hydraulics in which one pump performs the main movements (e. g., opening, closing, injecting) and the other carries out the secondary movements (e. g., ejecting, core pulling), the ejectors may also be traversed forward parallel to the mould-opening movement to transfer position L1. Overlapping the ejector movement with the opening or handling approach movement shaves a further 0.15 s off the mould-open time....
Kunststoffe international, 2005-11-21, Adding Value through Quality and Technology
...ir-conditioning is also installed in the workshops for the HSC milling stations and machining operations. The range of precision moulds includes those for sandwich moulding as well as multicavity moulds containing up to 48 cavities. The collapsible core technique [4] developed and patented by RKT enables demoulding of undercuts with a demoulding stroke of just 4.5 mm. Mould dimensions can be kept small as a result. This helps to make manufacturing of the parts more economical, as production can ...
Kunststoffe international, 2005-11-21, Additives
...e the cost-benefit ratio in overall terms. The trend in additives is towards easy-to-handle, environmentally-compatible products. Tailor-made solutions are providing evidence of closer customer proximity on the part of producers. By concentrating on core competencies and ensuring a worldwide presence, development times are being shortened, and a constant quality guaranteed, independently of the region. It is very difficult to give a reliable estimate of the consumption of plastics additives, s...
Kunststoffe international, 2005-11-21, Additives: Custom-engineered Plastics
...a small amount of additive. For instance, with Levagard DMPP, Bayer offers a low-viscosity product with a phosphorus content of more than 20%. It is intended for use in rigid PU foam that finds application in the construction industry or as the core in composite sandwich panels used for building construction, refrigerated warehouses and refrigerated storerooms. Clariant has expanded its Exolit Series by several additional variants that exhibit a low compound density, thus permitting plastics to ...
Kunststoffe international, 2005-11-21, Additives: Tough and Heat-resistant: New Silicone Particles for Thermosets
Thermoplastic Elastomers Tough and Heat-resistant: New Silicone Particles for Thermosets Additives A new generation of nanoscale silicone and core-shell particles is revolutionising the modification of heat-resistant thermosets. Even small additions of the new particles significantly increase the impact strength and fracture toughness of reactive resins and other plastics. Jochen Ebenhoch Highly crosslinking reactive resins, such as hot-curing epoxy resins, bismaleimide resins or cyanate resins ...
Kunststoffe international, 2005-11-21, Aid for Day-to-day Business: E-commerce Portal Facilitates Business Transactions
...ployees and annual turnover of EUR 450 million per year in 2002. BASF IT Services is among Europe's leading IT companies and also offers its services outside the Group. Its core activities are IT solutions for the process industry, managed infrastructure services and outsourcing business processes. BASF IT Services now operates one of the world’s biggest network systems and about 1000 servers for about 50000 users at over 250 sites. The BASF “WorldAccount” is one of the biggest of the many W...
Kunststoffe international, 2005-11-21, Airbus to Fly with PPS
...on rolls weighing up to 100 kg. At Nijverdal in the Netherlands, the Lipp-Terler film and the glass-fibre or carbon-fibre reinforced fabric (depending on the application) are united by Ten Cate Advanced Composites bv. This specialist company, whose core competence is industrial fabric, managed to successfully marry the two materials into the high-strength, dimensionally stable and resistant composites (trade named Cetex) required for aircraft construction (see interview with Willem van Dreumel)....
Kunststoffe international, 2005-11-21, All-rounders: Industrial Gases in Plastics Processing
...mption of nitrogen by 100 to 300% enables cycle times to be reduced by up to 30%. Bonus effects are better dimensional accuracy and smoother internal surfaces of the hollow spaces (Fig. 2). CO2 Spot Cooling of Injection Moulds Cooling of long, thin cores or other virtually inaccessible areas of an injection mould cause problems in practice. Spot cooling of these hot areas with CO2 is performed in addition to conventional water cooling and only in those areas of the mould in which no other type ...
Kunststoffe international, 2005-11-21, Automotive Safety Parts: Sophisticated Occupant Protection
...operating conditions, for example at high or low temperatures or after ageing. The machine’s accumulator hydraulics play an important part in both the airbag container and the cap with predetermined rupture point, providing the required core-pulling functions and other parallel functions. The short cycle times required for cost-efficient production can therefore be realised together with a high-quality part. For the subsequent coating with a 2-component water-based paint, which provides both hig...
Kunststoffe international, 2005-11-21, BASF and its Customers: Profitable Growth
... and dialogue, as the basis for mutually beneficial partnership. "Ultimately, in the case of Renault, we are taking on responsibility for a very major part of the production process. This demanding type of partnership represents the core of our strategic guideline and thus the future of BASF. At the moment, Renault produces 180 000 cars in Slovenia. BASF Coatings is not being paid for the paint used in production of the vehicle, but rather for every perfectly coated body (Fig. 3). This is a ...
Kunststoffe international, 2005-11-21, Better-Quality Rubber Products
...ences, which could affect quality in the mixing room. The aim was to try to derive a new quality assurance plan for the mixing room that takes account of the most important influences on the quality of products. Analysis of the Extrusion Process Core task of the Prodesc project (Better Process Description for Silica and Carbon Black Compounds) is to analyse and describe the extrusion process for rubber compounds. A distinction is drawn between those process stages within the extruder and screw...
Kunststoffe international, 2005-11-21, Bonding of Plastics
...ce for this application, where temperatures range from - 160 to 60°C. Storage and transport of the liquefied gases at such low temperatures requires appropriate insulation. The tank insulation comprises sandwich elements with a closed-cell foam core that are bonded to each other and to the metallic outer layers. The adhesives have to have exceptional mechanical strength. This is particularly true in view of the residual elasticity and slight embrittlement at temperatures of approx. - 160°...
Kunststoffe international, 2005-11-21, Boost for the Economy: Becoming More Competitive through Co-operation
... study. The empirical proof of this is the continuous increase in key economic data. Sales of the KC companies from 1999 to 2002, for example, rose by an above-average annual rate of around 5.5%. The clear core statement: "Companies involved in a cluster perform better than other companies." [3] When the cluster partners were questioned about the goals achieved in the network, the results were very pleasing [4, 5]: - Cluster partners achieve 90 % of their goals – this speaks in favour o...
Kunststoffe international, 2005-11-21, Cards are Trumps – Chip Card Bodies for the World Market
...Giesecke & Devrient and Orga. Because of the lack of suppliers with the necessary expertise, some smartcard manufacturers were also producing the card bodies themselves with support from the system suppliers, but plastics processing is not a core activity for these companies, who are more at home in the printing and/or electronics sector. They would love to give up the plastics processing side – at least in part – as soon as possible, as Proske found out during initial talks with his potential c...
Kunststoffe international, 2005-11-21, Case Study: Hot-Runner Solution for an Electronics Coil
...oals with the need for low pressure loss in the system. The only way to find a optimum compromise is to choose the ideal melt-channel diameter in the nozzles and in the manifold. In the specific case, the parameters were as follows: - article: core of an electrical coil; - material: PA 66 with 25% glass fibres and V0 flame protection; - shape/dimensions: 20mm x 20mm (L x W), height 16mm, wall thickness 1mm; - article weight: 1g; - tolerance: narrow; - technical requirements minimum gate mark. Th...
Kunststoffe international, 2005-11-21, Cast Polyamides for Small Series: Goodbye Injection Moulds
...ting, are also possible if the surfaces are properly prepared. This, together with the polyamide’s high thermal resistance, is particularly critical for design covers in the engine compartment. The Next Stage: Lost-core Technology At rpm, they are particularly proud of the lost-core process for producing one-piece hollow parts with complex geometries. With the example of a charge air duct, Kreutzburg explains that a separate core is produced for every part to be cast, which is eventually lost i...
Kunststoffe international, 2005-11-21, Close Cooperation Ensures Success
... the difficulty of a low metering volume in combination with a high clamping force. The high-speed machines used in the packaging industry need different screws to process engineering thermoplastics. The mould designer must eliminate the risk of the core getting out of alignment because the melt, if it should flow unevenly around a complex core, will generate an enormous difference in pressure and thus create a high force. Apart from this, the demands made with regard to wear and tear and to ven...
Kunststoffe international, 2005-11-21, Coinjection of Thermoplastics and Elastomers
... axial robot and precisely positioned in the mould of the LSR machine, then the seal is injected. Because of the synchronous operation, the cycle time is determined by the longest individual cycle. With complicated moulds containing moving elements (core pullers, slides etc.), long cores or deep inserts, the transfer process should be regarded critically. Its usefulness is limited by the free shrinkage and non-reproducible cooling. Process Variant C: Coinjection In the above-described multicomp...
Kunststoffe international, 2005-11-21, Colour Variation: Two Components, Four Colours, Five Units
...te and an electrical revolving unit on the three stations. The moulded parts can thus be further processed, pre-sorted by colour, and packaged. When the mould is opened, the indexing plate is forced forward by a mechanical device. The use of a core puller or ejector is not necessary. The indexing plate is end-point controlled, with a laser controlling the opening distance. To remove the finished parts, an arm of the indexing plate swivels completely out of the actual mould area. The gripper of ...
Kunststoffe international, 2005-11-21, Combinations Enhance Performance Many Times Over
...n can be achieved through the appropriate treatment, such as a skin component in the sandwich process or overmoulding. In a project conducted at the University of Erlangen-Nürnberg an adhesive magnet was produced by the two-component technique. The core of the moulded part is made up of a polyamide with a high filler content of magnetisable metal fibres, which can be externally magnetised after injection moulding. Even processes such as marbling, which are relatively simple in process engineerin...
Kunststoffe international, 2005-11-21, Combined Process: Foamed Parts with Excellent Surface Quality
...them reliably can vary greatly. If special processes also have to be combined, the effort can be expected to increase exponentially. But it can also be completely different, for example in two-component Monosandwich injection moulding with a foamed core. The attraction of the process lies in the reliable and disarmingly simple technology – and of course in the technical advantage of the parts it produces. Reducing the weight of parts is a significant reason for employing foaming processes – but ...
Kunststoffe international, 2005-11-21, Composite Constructions: Industrial Production of Structural Components Made from Fibre/Plastic Composites
...of thickness transitions, - impregnation of textile semi-finished products underneath load transfer elements, - impregnation of preforms with different permeabilities in the thickness direction, - impregnation of laminates with core inserts. The first area of special interest in this project was the impregnation of stringer-stiffened shell components with parallel-sewn stringers. As part of this project, flow studies were conducted with the preforms produced by ITA. In these studies, particular...
Kunststoffe international, 2005-11-21, Composite Parts: Flexibility in Rigid/Flexible Combinations
... After first deciding in favour of LSR for the flexible component, the persistent cost pressure and the constant improvements in TPEs prompted a move away from silicone. The switch to a TPE/thermoplastic composite also made it possible to opt for a core-back or rotary mould instead of employing transfer moulding. One advantage here is that Weigelt now has all the standard multi-component process techniques at its disposal. Alongside standard machines, the rotary table machines are used whenever ...
Kunststoffe international, 2005-11-21, Compounding with Twelve Screws
...rotating parallel axle tight fitting screws arranged in a circle in the attached profile housing (frontispiece). A two-part process volume is formed by the ring shaped arrangement of the screw profile (Fig. 1A). In the process space there is a fixed core, the exterior profile of which is adapted to the screw profile. Through a hole the core can be kept at a moderate temperature and thus be used for different engineering process functions. The construction of the power transmission and the segmen...
Kunststoffe international, 2005-11-21, Compounds and Blends Made to Measure
...y is enhanced and high soldering temperatures can be withstood. They are therefore used particularly in the electrical and electronics industry as well as in the engine area. Manufacture of tribologically optimised materials is a further important core competence of the Luvocom team (Fig. 1). Because of the many different load cases, at Lehmann & Voss each tribological system is adjusted individually to the application. Here the compounds used are based on high molecular weight polymers with adm...
Kunststoffe international, 2005-11-21, Compounds and Masterbatches
...esistant and can therefore be used at the customer's premises in warehouses for environmentally harmful substances. In the "one-shot foam" process, a PE-LLD special powder is used for the outer skin of the ramp and granules for the foam core. The two components are manufactured in two heating cycles in one shot. The process allows foam to be used even for extremely complicated parts. The foam density of 150 kg/m3 reduces the weight of the parts while retaining high stiffness. An acce...
Kunststoffe international, 2005-11-21, Concrete Building: Plastics Replace Plywood
...ht onto the market in mid-2003 in three different concrete formwork systems (re-usable formwork). The system, for which a patent application has been submitted, is made of two main functional elements: a substrate system and a formwork film. The core of the substrate is a weight-reducing PP foam which is supported by glass-fibre reinforced cover layers in the outer zones. The substrate system and the film are used jointly as a formwork element in a conventional modular frame so that all the func...
Kunststoffe international, 2005-11-21, Control Engineering: New Technical Beginning in Machine Control
...the problem. It accessed parameter groups directly into which the user had to enter corresponding absolute values, which increased setting expenditure and which occasionally obstructed the clarity of the programming process. For example, the complex core withdrawal processes had to be configured with many “yes/no inputs”. Changed Operation Structure with Improved Overview This problem the controller developers at Arburg took on in two ways. On the one hand the control structure should be recti...
Kunststoffe international, 2005-11-21, Cooling in Miniature
...e reached for reasons of space or the cooling performance is inadequate to dissipate the heat. Moulded Parts and the Mould For the practical cooling trials, a mould was developed (Fig. 1), in which problem zones could be examined by changing the cores and cavities and by using cooling elements of different lengths. Through an analysis of moulds in practical use, it was found that typical problem zones can best be simulated by thin cylindrical or rectangular cores. Mouldings of this kind are sh...
Kunststoffe international, 2005-11-21, Cooling Injection Moulds
...environment. In the variants with escaping refrigerant, referred to here as gas cooling, carbon dioxide or nitrogen can be used. The carbon dioxide is kept in a storage tank under pressure. It is passed into a porous metal element, which forms the core of the mould, where it emouldates and finally escapes through a minute slit. The porous core can be covered with a polishable alloy to improve surface quality. The system is designed and supplied by the manufacturer complete with control unit, ref...
Kunststoffe international, 2005-11-21, Cooling Time Reduction by Foam Injection Moulding: It Can Be Done Faster
...r injection that they determine the lateral dimensions. The volume contraction during cooling in the mould acts to an extent of 90–95% in the thickness direction in the case of non-foam injection moulding [4]. If the temperature in the core region is still sufficiently high, the foaming core region compensates the thermal volume contraction of the outer regions in the case of foam injection moulding. If bubble growth decreases as the cooling time increases, the blowing agent pressure prevailing ...
Kunststoffe international, 2005-11-21, Cost Efficiency and Innovations
...portant products today. Production capacities are located at strategically favourable locations in the USA, Mexico, Brazil, Argentina, Chile, Korea, China, India, Malaysia and Europe. Annual capacity worldwide is currently 2.2 billion tons for the core fields of polystyrene and EPS alone. Fixed overheads have been reduced by more than 30 % by comparison with 1996; this has been achieved through a comprehensive programme of restructuring, especially in Europe, and by increasing productivity throu...
Kunststoffe international, 2005-11-21, Cost-effectiveness: In-mould Decoration on Modified Standard Machines
...needs of the different types of decorative material. Technical Implementation of the Specifications The problem of the different extensibilities of the decorative materials was solved by using a hydraulic clamping frame mounted on the core side of the mould. This enables all decorative materials to be processed on the same mould. The core side is the fixed mould half. It features not only the hydraulic clamping frame, but also the hot runner systems and the ejectors (Fig.4). The production cyc...
Kunststoffe international, 2005-11-21, Cutting Costs, Increasing Benefits: Multi-Component Injection Moulding as Innovation Driver
...t-coloured materials, e.g. for vehicle tail-lights. - Rigid-flexible combinations for integrating seals, damping vibration and improving haptic properties, e.g. in operating elements and handles. - Formation of a multi-layer structure: Thus, a core component may consist of fibre-reinforced, foamed or recycled plastic under a skin component of unreinforced material with high optical quality.This process is also known as sandwich injection moulding. - Combinations of conducting and non-conducting ...
Kunststoffe international, 2005-11-21, Cycle time reduction: Linear Motion Technology Accelerates Production Exponentially
... AG substantially accelerated manufacture of thin walled injection moulded parts in its Schweinfurt/Germany works using an automation system from the handling specialist Hekuma GmbH. Hekuma uses Rexroth’s linear motion and assembly technologies as core components for the high-speed unloading robot. Torsten Kirchmann The highest quality and 24 hour delivery capability are crucial competitive advantages for us.” As Sigmund Appelmann, director of plastics manufacturing in the Schweinfurt works ...
Kunststoffe international, 2005-11-21, Decoration During Injection Moulding: Preforming and In-mould Lamination in one Operation
...d radiators heat the carpets shortly before processing at a suitable temperature before they are immediately inserted by a handling system in the mould. The mould closes and the carpet is preformed by the three-dimensional contour of the mould core side. To avoid wrinkles or cracks in the carpet, a tensioning frame is installed on the fixed side of the mould (Fig.4). Before the core side penetrates into the carpet, the decorative laminate is clamped between the movable mould side and the tension...
Kunststoffe international, 2005-11-21, Decoration on the Front, Attachments on the Rear
...mplex structure of the rear side of the basic support is illustrated in the grid model in Fig.4. To achieve the 180° wrap around the edge of the part, the mould has an intermediate plate (c in Fig.2) which is incorporated as a frame between the core plate and the moving mould half. This plate is necessary in order to allow the finished part, with the fold-over which acts as an undercut, to be demoulded. A version with a lateral slide on each of the four sides was not pursued any further on a...
Kunststoffe international, 2005-11-21, Degradation Behaviour of Polyoxymethylene (POM)
...ness-leading partner of the HB-Plastic GmbH/Austria and the HB-Plastic Kft./Hungary. Fig. 1. Influence of multiple processing on the MVR; dependence of the decrease of the elongation at break on MVR for example heat stabilised POM copolymers 1. A: Core morphology (copolymer 1, first processing step); B: Core morphology (copolymer 1, seventh processing step) Verarbeitungsschritte = Processing steps; Reißdehnung = elongation at break Fig. 2. Influence of the stabilisation states on degradation ...
Kunststoffe international, 2005-11-21, Development History of Plastics: Growth through Changing Times
...pliers of standard products, innovators and problem-solving partners, and service providers. They must increasingly decide where exactly their core competences lie, which marketing aims they can realistically achieve and what kind of organisational structures they need to succeed in this. All too often the number of product grades in individual ranges is still being reduced and portfolios are being stripped of less profitable specialities. The result is volume-oriented business models adapted to...
Kunststoffe international, 2005-11-21, Development Partnerships – Innovations Guaranteed
... the Development of Products and Processes The formulation of new materials or the modification of already existing ones often occurs at the very early stages of product development. Naturally, this task is part of the raw material producer’s core competence. Over the past years, raw material producers have acquired more competence in the area of component development which enables them to co-operate efficiently with car manufacturers and system suppliers at a very early stage in implementing t...
Kunststoffe international, 2005-11-21, Development Trends: Composites for Aircraft
...itional development objective is generally a fast and autoclave-free curing for which new curing methods such as microwave technology are favoured. For sandwich construction, which provides very high stiffness at a low weight, honeycomb cores have been used for the most part. While these offer very high shear and compression characteristics, they are very expensive because of the discontinuous production method. The closed chambers in which condensation occurs under operating conditions, for ins...
Kunststoffe international, 2005-11-21, Development Trends: Extrusion Blow-moulded Automotive Components
...d-Hagen-Preis was awarded to an impressive innovation: blown components were filled with expanding foam. In future, this new method will allow the production of shock absorbers for better passenger protection or the introduction of bumper cores. Other new developments in this area will be implemented in co-operation with the OEMs. Depending on the size of the products, they will be produced on small extrusion blow moulding machines with clamping forces in the 25t to 60t range. Since they will be...
Kunststoffe international, 2005-11-21, Dies for Multi-Layer Pipe Extrusion
...em may differ even within one type of model. With spiral mandrel dies, the spectrum extends from the traditional manifold in which each spiral is fed from one drilled hole (star-type), to a melt predistributor which has a coathanger die mounted on a core mandrel, with a subsequent spiral manifold. Between these two extremes, there are designs with multiple pre-branching plus several coathangers plus spiral mandrels with a large number of spirals. Increasing the geometric degree of freedom is of ...
Kunststoffe international, 2005-11-21, Direct Laser Forming: New Structures Built up Layer by Layer
...tion with Two Chambers In the design of the TrumaForm LF machine, Trumpf Werkzeugmaschinen GmbH + Co. KG, Ditzingen/Germany, places special emphasis on flexibility and productivity as well as on industrial safety and process reliability (Fig.2). The core of the machine consists of the two identical processing chambers in which the actual construction takes place. While the finished parts cool in one chamber, a new cycle can be started in the other, even with a different material, if necessary. T...
Kunststoffe international, 2005-11-21, Double Belt Plants: Flexible Production of Various Insulation Panels
Building Flexible Production of Various Insulation Panels Wolfgang Friedl Michael Loferer Double belt plants. Large-size, pre-manufactured sandwich panels with a mineral wool or polyurethane foam (PU or PIR) insulation core have proved particularly successful in industrial buildings and cold store warehouses. Both types of element are produced on double belt lines in different configurations and stacked ready for shipping. The weatherproof, ready-to-use sandwich panels with outer layers made ...
Kunststoffe international, 2005-11-21, Double the Output
...thout a hot runner system. The locking mechanism consists of two rotating bolts that lock the parting line at each end with a bayonet-type lock. Both bolts move synchronously through the movement of a toothed belt. This belt is activated with a “core pull”, in other words it moves to the other position after each cycle (Fig.2). Every end position is monitored by a limit switch. Only when a limit switch is giving a signal should the relevant core pull be released for the ejection process. For th...
Kunststoffe international, 2005-11-21, Drafting Tolerances for Moulded Parts
...ape-Determining Dimensions Shape-determining dimensions are circumscribed in the same mould half by non-moving elements. Non-shape-determining dimensions are those dimensions which are formed by movable mould elements, such as slide bars, jaws, and core pullers or through the other mould half, i. e., thickness and floor dimensions. Naturally, these dimensions require greater tolerances since movable elements do not always move to their end position [3]. When applying tolerances as per DIN 16901...
Kunststoffe international, 2005-11-21, Drive and Applications Technology: All-Electric Broadside
...e are realised with a small integrated hydraulic unit. The weakening of the all-electric philosophy in favour of hybrid drive technologies was in many cases forced by practical necessities. Many moulds are still equipped with hydraulic core pullers. In the case of servo-electric rotary tables, locking is by means of an index pin and often hydraulic because of the dynamic advantages. The opening up of all-electric machines to a larger spectrum of applications means that general market trends must...
Kunststoffe international, 2005-11-21, Drive Technology: Reproducibility and Costs Are Primary Concerns
...alyses. The fully electric machines used by this processor incurred no costs for hydraulic oil. However, some of the fully electric machines available on the market have small integrated hydraulic units, e.g. for nozzle forward movement or core pullers. Even if machines require no hydraulic oil, lubricants are needed for the toggle and drive unit. These costs, which are not specified for the individual machine sizes, amount on average to 1.5cents/operating hour. That means that almost all machi...
Kunststoffe international, 2005-11-21, Driving the Automotive Industry: Engineering Elastomers
... applications. The Italian company Rapisarda Ind. has developed an interesting application: ozone-, weather- and fire-resistant hydraulic hoses for the maritime sector with an inner core of NBR and a CR outer layer. Both elastomer layers have good adhesion to steel wire reinforcement, withstanding bursting pressure peaks of 400 bar and continuous pressure loading of 300 bar. The estimated demand for NBR (service temperatures from –40°C to 125°C) is 380kt/a. The Chinese market is estimated to be ...
Kunststoffe international, 2005-11-21, Dynamic Growth: Liquid Crystal Polymers (LCP)
...mand in the Far East, especially the booming Chinese domestic market. Demand in Europe has also revived, not least of all due to the new camera mobile phones and the recovery in the electronics industry. In addition to the recovery of this ”core market”, penetration of LCPs into new market segments, such as the market for electrical components, has contributed to growth. Along with increasing miniaturisation and higher operating temperatures, the more stringent regulations of environmental auth...
Kunststoffe international, 2005-11-21, Easy and Reliable Demoulding
...rtment of Aalen Technical College and the firm NovoPlan Oberflächentechnik, Aalen, examined the influence of a mould surface coated with electroless nickel PTFE on the demoulding properties of an injection-moulded polystyrene part [1, 2]. The mould core did not have any drafts. The ejector forces with an uncoated and a coated mould were compared, and the surface roughness (peak-to-valley height) of the uncoated and coated core was measured at four points (over the entire length). To determine th...
Kunststoffe international, 2005-11-21, Ecological Beneficial Composites
...ave to be taken care of at high cost. Production of Different Components Three Dimensional Shapes: Arbitrary high strength three dimensional moulded components can be produced using a reaction casting technology developed by Schock & Co. GmbH. The core element is a heated metal mould (Fig. 1) consisting of two half moulds built into a press. Several layers of fibre mats are inserted into the lower half mould depending on the desired wall thickness of the later moulded part. Then an appropriate...
Kunststoffe international, 2005-11-21, Economical in Long Series
... load the component will later carry. - The thermoplastic pipe with reinforcement material wound on it is then inserted into the centrifuge mould. In this way an appropriate fibre orientation is achieved in the centrifuge mould. - The thermoplastic core pipe is heated during slow rotation until the thermoplastic material is melted and functions as matrix material. - The actual centrifugation procedure takes place in the fourth step. The rotation rate of the centrifuge mould is increased. Due to ...
Kunststoffe international, 2005-11-21, Editorial: A Healthy Approach
...have it in black on white once again – Germany is the world's biggest producer and exporter of plastics and rubber machinery by a clear margin, with world market shares of some 25% in each case (page 24). The production volume of Germany's core machinery business attained a value of EUR 4360 million in 2003, with three-quarters of this sum generated by exports. The sector certainly needs have no qualms about ascribing this success to its readiness to engage in new developments. Two facto...
Kunststoffe international, 2005-11-21, Elastomer Composites: Complex Mould Technology for Sealing Membranes
...the gripper to execute a 90° movement, and a rotary module is for a movement through 180°. The complete ancillary equipment of the line – besides the robot system, this includes the cooling units, drier, metering systems, mould heating and core pullers – is integrated in the machine control system and can therefore be centrally operated. Production Sequence The production sequence in detail: the central unit injects the polyamide in one station, simultaneously, in the second station, the other ...
Kunststoffe international, 2005-11-21, Elastomers
...ccording to consumer regions is given in Table2. Along with other characteristic data, the per capita rubber consumption is also an indicator of a country’s economic efficiency. Table3 gives the growth in the core data (volume of natural and synthetic rubber) for some selected industrial, threshold and developing countries over the past ten years. China shows a renewed – though subdued – special development here. The distribution of the market shares of some important synthetic rubber grades (SB...
Kunststoffe international, 2005-11-21, Electrifying: Emphatic Confidence
...nd, on 25 June. This programme was marked by geographical, product and application-specific diversification, ensuring high product quality, expansion of all services and the claim to be a trendsetting innovator in the market. The current and future core expertise of Netstal would consist in the development, production and marketing of injection moulding machines and systems for fast-moving thin-wall parts as well as high precision technical parts. Positive Balance Sheet for Fiscal 2003 In fisca...
Kunststoffe international, 2005-11-21, Engineering Network: Additional Knowledge Instead of Competition
...s "growth of the order of magnitude of 10%". The company's goal is to retain its strength, which derives from innovation, and to systematically expand the business without losing the company's focus on its own core competencies. When it comes to future projects, all that Johannes Jacob will hint at is that "thermoforming and composites will soon be meeting up once again in a highly attractive automotive application." "QIC Systemverbund Kunststofftechnik" QIC p...
Kunststoffe international, 2005-11-21, Engineering Plastics as a Growth Market
Engineering Plastics as a Growth Market DuPont Anticipates Double-digit Growth Rates for Sales and Earnings Even after the strategic realignment at DuPont, engineering plastics will continue to be one of the company's core businesses. With world wide sales of around $ 2 billion, DuPont is the market leader in this field. Its portfolio covers polyamides, polyesters (PBT and PET), polyacetals, polyimides and liquid crystalline polymers (LCP). After its withdrawal from the energy business...
Kunststoffe international, 2005-11-21, Enhancing Performance: Fast-Cycle Injection Moulding Machines with Tandem Moulds
... with the conventional process (Fig.1). For the alternating cycle mode of operation, a bayonet locking system needs to be mounted outside onto the mould (Fig.3), activated by a rotating toothed belt. The machine needs a special core-pulling program that controls the activating cylinder for the toothed belt drive. This action always takes place with the mould closed under clamping force. In this condition, a mould normally shrinks by approx. 0.3mm, so that the bayonet can lock without force. Only...
Kunststoffe international, 2005-11-21, Enterprise Transparency: Success Factor Business Process Management
... in this business area beginning in 2001 with rapid expansion of the automobile business. This presupposed two substantial decisions. Reasons for Building up a Business Process Management The management decided first of all concentrate the works on core tasks and second to structure a process management based on ISO 9001:2000 and ISO/TS 16949. The message accompanying the second decision read, "We do not develop a quality management system in order to hang a certificate on the wall, but we ...
Kunststoffe international, 2005-11-21, Exhibition Preview: North American and Canadian Products at K 2004
...ngstown/Ohio, will show off the Twinshot coinjection system, which can produce sandwich structures of two materials from a single barrel and screw. It will demonstrate the technology by molding a polycarbonate part with clear skin and colored core. Spirex will introduce the Power-Purge system, which cleans screws, barrels, and nonreturn valves without disassembling the injection unit. This is accomplished with a new, patented valve design and a cleaning compound. Hot-runner Technology Fast Heat...
Kunststoffe international, 2005-11-21, Expansion Injection Moulding: Amazingly Thin
...in expansion injection moulding, a commonly used screw with a diameter of 25mm and an overall length of 945mm (shank length 325mm + screw section length 620mm) is used as an example. With a mean core diameter of 18.8mm and a shank diameter of 23mm we get a mean stressed cross sectional area along the length of the screw of 3.25cm². For a preloaded pressure of 2500bar, an injection force of 123kN is required. This produces a compressive stress of s = 378N/mm² and thus a screw compression of 1.7mm...
Kunststoffe international, 2005-11-21, Experimental Testing: Ring-shaped Reinforcements Made of Fibre-reinforced Composites
.... 6). Both burst tests and pulsating pressure tests were conducted. One-piece PTFE sleeves served as seals. The fibre-reinforced composite test specimens were rings of epoxy-impregnated E-glass rovings produced by winding around a core unidirectionally in a wet winding process. The individual test specimens were cut to length and then machined flat. This assured a narrow gap between the ring-shaped specimen and the firmly attached plates that were separated from the specimen by the spacer ring. ...
Kunststoffe international, 2005-11-21, Export Champion: Changeover Completed
...ubber processing machine producers presented their newest technologies and trends at the K2004. The country has a crucial advantage: Taiwan uses manufacturing plants in China and in other parts of Asia, so-called low wage countries. However, the core components are still manufactured in their own country. Thus the country secures relatively high quality at low prices. To the question, why complete plants are not built in China in order to be still more competitive, most exhibitors with productio...
Kunststoffe international, 2005-11-21, Extrusion Technology of the Future
...ral, there is a trend towards tailored products manufactured by coextrusion (Fig. 6). Typical representatives include multilayer systems (Fig. 7) with metallic or non-metallic barrier layers, electrically conductive or anti-friction layers. PVC foam-core pipes are showing high growth rates on the market for unpressurized sewer pipes. They increase productivity and reduce material consumption [5]. For window profiles, attempts to find substitutes for tried-and-tested PVC will remain unsuccessful ...
Kunststoffe international, 2005-11-21, Fibre Orientation in the Simulation: Improved Dimensioning of Engineering Plastic Parts
...tions were then readily transformed into a tetrahedral volume model by means of Part Converse for the structural simulation. It was thus an easy matter to prepare the FEA model, since there is no need to generate the middle surface models. Reducing Core Displacement in Fusible Core Moulds In the design of fusible-core moulds, it is very important to reduce core displacement. The core can be displaced as a result of the melt pressure during injection moulding. If core displacement is significant...
Kunststoffe international, 2005-11-21, Fibre Reinforced Plastics: Tailor-made Reinforcing Textiles
...ir are generated here. Apart from round and stranded braiding machines, 3D rotation braiding machines are also available for generating three-dimensional braids with different cross-sectional shapes. It is also possible to create braiding around a core structure in some cases by employing different braiding methods. Knitted goods such as warp-knitted and weft-knitted fabric (Fig.3) can similarly be used. When stitches are formed, a loop of thread is pulled through the previous stitch by means o...
Kunststoffe international, 2005-11-21, Film Extrusion: For Flexible Packaging
...tifunctional winder that, like the S model, can reverse the direction of rotation if it is fitted with a vacuum-contact cutter drum. There is an option for additionally equipping this model with a laser core-positioning marker. This device is easy to use and saves time in precise coring during multiple roll production. The Filmatic T dual winder (Fig.2), which was launched back in 2001, saves considerable space through the vertical arrangement of the two winders in one frame. Maximum reel diamet...
Kunststoffe international, 2005-11-21, Flat-film Extrusion Lines
...to 10 m/min can be achieved without any problem because of the excellent true running of the servo motors. - The modular construction technique permits the right variant for the specific product to be used, which can be changed at any time. - A reel core preparation is not required - a cost-saving advantage in further processing on automatic converting machines. - Reel hardness (relative reel density) can be determined and displayed during production. - Freely selectable winding curves can be in...
Kunststoffe international, 2005-11-21, Flexibility Profit in Lost-core Technology
Flexibility Profit in Lost-core Technology Lost-core Machine with Two Independent Mould Clamping Units Windsor Kunststofftechnologie GmbH, Hanau/Germany has developed a new concept for a lost-core machine. The KGM 100 Duo model has two independent mould clamping units for the simultaneous use of two moulds and a relatively high clamping force of 1000 kN for casting metal cores. This company, part of the Cannon Group since August 1999, supplied the first design of the large lost-core machin...
Kunststoffe international, 2005-11-21, Flexible and Inexpensive
...rcing fibres. The critical fibre length is a function of the temperature and the load. At higher temperatures, longer fibres are needed to distribute the load effectively from the polymer matrix onto the fibres. The long glass fibres display a skin/core structure within the injection moulded part [2]. The fibres at the mould surface are orientated in the direction of flow, whereas the fibres in the core region tend to be orientated perpendicular to the direction of flow. Compared to the more pro...
Kunststoffe international, 2005-11-21, Flexible and Precise
...vacuum-forming machine was developed by Georg Geiss Maschinenfabrik, Sesslach/Germany, and implemented in a first system. According to the manufacturer's data the mould change time is shortened to about 5 min with this system (Fig. 6). The core item in the system concept is a fully automatic changer that takes the mould out of the machine after use and inserts a new mould. Also the sheet feeder is provided with material by the changer. Infrared Heating Systems Interesting new developments ...
Kunststoffe international, 2005-11-21, Fluid Injection Technique: Manufacture of Multilayer Media Lines
Injection Moulding Manufacture of Multilayer Media Lines Fluid Injection Technique. Gas-assisted and water-assisted injection moulding technique allow channels to be formed in the molten regions of an injection moulded part by displacing the molten core into cavity regions that are at first unfilled or are additionally opened. New possibilities for reducing costs and producing innovative plastic hollow bodies can be achieved by combining this process with multicomponent injection moulding. Wal...
Kunststoffe international, 2005-11-21, Fluid Injection Technique: Production of Media-conveying Ducts
...ses as to whether this process is suitable for the production of a media duct. An appraisal of this type should always be performed by comparison to extrusion, 3D blow moulding, the half-shell technique with a subsequent joining process, or the lost core or fusible core technique. The FIT has a number of advantages over other processes: - Functional components, such as fastening elements and connections are injection moulded together with the part, or the media-conveying ducts themselves are in...
Kunststoffe international, 2005-11-21, Fluid Injection Technique: Understanding Residual Wall Thickness
...tely the gas-assist (GIT) and water-assist (WIT) injection moulding techniques, permit creation of voids (cavities) within molten regions of an injection moulded part via controlled injection of gas or water by having the fluid displace the molten core material into as yet unfilled (short-shot method) or newly opened (overflow method) regions of the mould cavity. The residual wall thickness (RWT) of a hollow plastic part produced in this way results from the process of part formation, a so-call...
Kunststoffe international, 2005-11-21, Formwork Elements: Building System with High Future Potential
...anels with connecting elements are only assembled at the building site. With both systems the connecting elements can consist of plastic or metal. Furthermore three structural systems are distinguished. With the “flat wall” system the concrete core forms a homogeneous core of even thickness. If the concrete core consists of connected horizontal carriers and vertical columns, the construction unit is called a “waffle grid” system. With the “post and beam” system the concrete core forms self conta...
Kunststoffe international, 2005-11-21, From a Trading Company to an Assembly Supplier
...iness activities mark the outcome of the consistent further development of what was initially a trading company with a limited manufacturing capacity, through to a production company that also engages in trading activities. The company’s core business thus rests on three pillars at present: - plastic mouldings and assemblies - rubber mouldings and extrudates - flexible hose systems. Apart from the parent company in Lippstadt, Schieffer also owns two subsidiaries in the USA and Israel, as well as...
Kunststoffe international, 2005-11-21, From Plastic to Branded Article
...l materials. The plastic was previously known mainly to industry connoisseurs or plastics processors. Now Bayer wants to build up the Makrolon brand and make it popular with a broad public. Bayer, an international research-oriented enterprise with core activities in the fields of health, agriculture, polymers and chemical specialities, has already developed world-renowned brands in the health field. For example, "Aspirin" is a common and frequently used synonym for the term headache ta...
Kunststoffe international, 2005-11-21, From the Idea to the Product
From the Idea to the Product Examples of a Consistent Development Process Ernst Schmachtenberg, Rainer Dahlmann, Oliver Pfannschmidt, Markus Glissmann, Sven Prollius and Jochen Töpker, Aachen/Germany In the course of part development, complex and interlinked problems are frequently encountered which have to be worked through on a step-by-step basis. The huge variety of problems that arise and the links that exist between them are set out on the basis of specific examples taken from differe...
Kunststoffe international, 2005-11-21, Functional Compounds
...sivity of the magnetite/PP compound permits considerably shorter cycle times in the injection moulding process than for a glass filled PP, for example. Magnetic properties: Soft ferrites, which also include the ferrimagnetic magnetite, are used as a core material for coils and transformers for power electronics (line transformers, accumulator chokes, ballasts and combinational circuit components) as well as for interference suppression in filter coils and pulse transformers. Figure 4 shows a num...
Kunststoffe international, 2005-11-21, Functional Integration: Packaging Design Between Economy and Creativity
... as Foundation The packaging is such a substantial part of the brand that it is constant in all its essential aspects. It is the constant feature. It can remain constant, however, only when in all essential aspects, this essential aspect, the brand core, is found to be unique. Only after the brand core, the brand positioning with its values, has been found and the core competence has been worked out, can work on the packaging design (Fig.1) begin. Professional packaging designers work on the bas...
Kunststoffe international, 2005-11-21, Functional Plastics: Materials Research as Technical Investment
...ew models of cooperation between developers and end users as well as a rethinking of the innovation process. It no longer suffices to desire new materials; initiative is necessary. With increasing concentration of the plastics sector on its core businesses, a completely new field of activity has opened for R&D specialists as service provider, developer and producer of new materials. Companies that take such an approach enable both the resin manufacturing sector and the end-user industries to pur...
Kunststoffe international, 2005-11-21, Functionality is the Key Factor
...operating theater or hospital ward made by GMP Poliurethani, Oderzo/Italy takes full advantage of the potential offered by a modern high-performance plastic such as Baydur 60 (Fig. 6). The material has a sandwich structure consisting of a cellular core and a solid smooth surface. This results in high strength properties and impact strength in combination with low weight and low wall thicknesses. It can also be used for complex moulding geometries which are difficult to achieve with thermoplastic...
Kunststoffe international, 2005-11-21, Gas - Not just because of the Cell Structure
... melt into the cavity. If the melt comes into contact with the mould wall, it cools down in this area to below the glass transition temperature and foam formation is halted. A three-layer structure is formed with compact outer layers and a cellular core, similar to a sandwich structure. Observations with heterogeneously nucleating plastics show that, due to the high speed of foam formation, not much outer layer is formed so that the three layer structure is not complete. The compact layers form ...
Kunststoffe international, 2005-11-21, Gas-assist Injection Moulding: GAIM: From the Design to Successful Application
...ty, it can now be assumed that the two moulded parts are similar in terms of their suitability for production by the GAIM process. Taking the GAIM process employed (standard process, melt push-back process, overspill cavity process and core-puller process), the expected production problems and reject rates, etc. can be transposed from the pedal to the bathroom fittings and a statement made on the subsequent production process (Fig.12). It is intended that the user should work on the assumption t...
Kunststoffe international, 2005-11-21, Gas-assisted Injection Moulding: Accurate Determination of the Injection Points
... three to four (Figs.4.3 and 4.4) provided an improvement in part filling, though it was still not optimum. A successful and reproducible application of gas-assisted injection moulding in this part is only possible by means of side-cavity, core puller or melt back-pressure processes. Another example in which gas channels have been identified with a unidirectional flow direction is shown in Fig.5. The surrounding edges of the article are intended for stiffening and at the same time prevent warpag...
Kunststoffe international, 2005-11-21, Gas-assisted Injection, Temperature Control, Foaming: Industrial Gases as Aids During Injection Moulding
...g resin to form hollow channels. Gas-assisted Injection Moulding When employed for gas-assisted injection, nitrogen is injected at high pressure into the polymer melt that has not yet completely filled the mould. The gas displaces the melt from the core of the moulded part and presses it against the cavity wall. This creates a void in the core of the part (Fig.1) – the amount of material used and the moulded part weight drop considerably. After solidification of the moulded part, the gas is rel...
Kunststoffe international, 2005-11-21, Gear Lever in Hand
...combination PP/SEBS that makes economic production in the 2-component injection moulding process possible. Until now high-quality passenger car gear lever knobs have been composed predominantly of a polyamide strengthened with glass fibres for the core, which is then covered by polyurethane and leathers. The glass-fibre reinforced polyamide thus transfers the gear changing forces to the shift rod, while the polyurethane foam material in combination with the leather provides for pleasing tactil...
Kunststoffe international, 2005-11-21, GIT, Sandwich and Two-component Moulding in Practice and Research: Correct Application of Multicomponent Processes
...r in an injection unit are injected in a single operation into one or more mould cavities (Fig.4). The controlled mould filling of this simultaneous process is based on the different rheological properties of the two materials. The skin and core components must be compatible enough to form composites with one another; the freer flowing skin component, which is transferred into the injection unit from a side extruder, precedes the core component there. The core component is plasticised in the in...
Kunststoffe international, 2005-11-21, GITBlow: Inflating Functional Channels in the Injection Mould
...ing can be achieved: - large hollow-channel cross-sections, - uniform distribution of the (low) residual wall thickness, - extremely thin-walled functional channels, - integration of delicate regions, - complex geometries that are not possible by core pulling, - and a wide range of applications; - secondary processing steps are eliminated. State of Development and Further Challenges The first studies have shown that the concept of the GITBlow process is in principle technically realisable. To...
Kunststoffe international, 2005-11-21, Growth through Specialities: New Markets and Individual Compounds
Distribution and Compounding New Markets and Individual Compounds Growth through Specialities. The distributor and compounder, Albis Plastic, plans further growth by adding complementary products and specialities to its core product range. Albis in-house developments are also important focal points for cooperation with OEMs. The Germany company Albis Plastic GmbH, Hamburg, is systematically pursuing its strategy of adding complementary products and specialities to the core product range it han...
Kunststoffe international, 2005-11-21, Heat Management
...integral foams such as Baydur from Bayer), an in-situ foam system can be used, which seamlessly encloses the "foreign body". With purlin roof elements, in which two wood-based panels (e. g. chipboards) form the facings and enclose a PU foam core, self-supporting roof structures can even be produced. With these constructions, a conventional rafter roof frame is unnecessary (which saves costs). By means of 16 mm chipboards and 110 mm thick insulating core, a heat transition coefficient of ...
Kunststoffe international, 2005-11-21, Hedging to Cover Risks: New Opportunities with Fluctuations in Raw Material Prices
...he leading IT full service providers in the SAP environment. In addition to consulting, engineering and system integration, the licence business and the outsourcing and services sector, including hosting, are among the firm’s core competencies. Further activities are complementary solutions and services, including those for chemical enterprises and food and semi-luxury production. itelligence is a long-time partner of the SAP AG, Walldorf/Germany, and has received multiple awards. itelligence of...
Kunststoffe international, 2005-11-21, High Increase in Consumption: Polyamides (PA)
...artment. In materials for suction modules, a trend towards PA6 can be observed. In addition to the lower raw materials costs, this trend is being driven by reduced manufacturing costs for friction-welded PA6 intake manifolds, compared with fusible core cast intake manifolds of PA66. In the engine compartment, the temperature and stress limits are being pushed ever further. Examples of this are pioneering application developments, such as the first oil-filter module (series production Audi A6, 20...
Kunststoffe international, 2005-11-21, High-Grade Design
...h, by contrast to the case for conventional IR radiators, has been reduced to 1 µm, so that it does not fall within the range of an absorption peak in the material. This reduces the surface heating and counteracts the inadequate heating of the core of the comparatively thick panels. Cycle times of less than 3.5 min and an automatic tool change permit the cost-efficient production of tubs in batch sizes of one to five and thereby enable processors to react flexibly to customer wishes. The h...
Kunststoffe international, 2005-11-21, High-performance Applications: Trends in Packaging Technology
...ll as different centring hole diameters. The important thing is that the clamping force is introduced into the centre of the mounting platen, which is the case for the hydraulic clamping units of the Ferromatik machines. As a result, the sensitive cores are dependably supported in the moulds. This eliminates core displacement, especially in multicavity moulds. That has a substantial influence on product quality and the lifetime of the precious moulds. New moulds generally do not cause the proble...
Kunststoffe international, 2005-11-21, Higher Value Added
...ssion of the Karl Egger family. For more than 50 years it has been concerned with developing, producing and selling plastic tubing systems and tubing insulation as well as tubes pre-insulated at the factory. The product range of KE Kelit covers four core areas as well as special products: tubing systems buried underground, connection tubes for heating element tie-up and sub-floor heating, drinking water tubing systems and sound-insulated discharge systems as well as tubes and hoses for thermal a...
Kunststoffe international, 2005-11-21, Hybrid Technology: Tailor-made Thermoplastics with Layer Structures and Continuous Fibre Reinforcement
...e microstructure of the braid-reinforced hybrids, Promolding BV, The Hague/Netherlands, developed hollow, cylindrical test specimens that it dubbed “dog bones” (Fig.3). Flat composite inserts may be used for applications that require a rigid core, e.g. compact gear levers with moulded-on functional zones. Furthermore, preform combinations, such as wound cages and local radial reinforcements, can be made from UD profiles. Moulds for the Hybrid Technology The mould technology for the new hybrid ...
Kunststoffe international, 2005-11-21, Hydraulic and All-electric Injection Moulding Machines in Practice
...n therefore exert a considerable influence on the different characteristics of a particular machine. It is often said that the absence-of-oil advantage enjoyed by electromechanical injection moulding machines is negated by moulds with core pullers – this is frequently correct, since hydraulic core pullers are predominantly used in moulds (Fig.5). That there is another way, i.e. the use of electromechanical core pullers (Fig.6), is illustrated by a mould which Wilkinson in Solingen/Germany employ...
Kunststoffe international, 2005-11-21, Impact Modification Of Thermosets
... phase separation only occurs up to about 20 % by weight of rubber. With a higher percentage, a mixed phase of rubber and resin can occur, or the rubber can form the matrix with resin particles incorporated in it [1]. To avoid this problem, special core/shell particles of fixed size are also sometimes used. One of the decisive factors for the toughness of a material is its ability to absorb energy, which can be done in a variety of ways. A number of publications have appeared on the subject of e...
Kunststoffe international, 2005-11-21, Improved Efficiency and Quality
... the temperature in the region of the screw tip agrees with the temperature profile of the rest of the screw channel. Various measurements carried out in the pilot plant have given detailed information important for the design of screw tips and the core bore. The aim is to achieve a melt temperature profile that is as homogeneous as possible and therefore the same for all extruder types (Fig. 7). This allows increased flexibility for using dies on different extruders. Apart from the melt-tempera...
Kunststoffe international, 2005-11-21, Improved Performance
...improved activity over the 1st and 2nd-generation phenols, AO-2110 still shared the poor gas fade discolouration tendencies of AO-2176 and AO-BHT. No Discolouration The next breakthrough in technology came with the incorporation of an isocyanurate core in a multifunctional hindered phenol. AO-1741 and AO-1790 represent the 4th generation of hindered phenol antioxidants. These compounds have the highest specific phenol concentration and excellent volatility. However, what really sets the 4th ge...
Kunststoffe international, 2005-11-21, Injection Moulding (1): Innovation at Closer Inspection
...ier layer in a two cavity mould on a Krauss Maffei machine. So far the processing has always run serially, i.e. the barrier component on the inside was injected after the skin component on the outside. However, thereby uneconomically thick core layers develop. Only with the hot channel nozzle technology now surfacing (Kortec, Hofstetter) is it possible to inject both melts at the same time and thus to manufacture barrier layers of less than 10% of the total wall thickness (Fig.7). Things have ca...
Kunststoffe international, 2005-11-21, Injection Moulding by MuCell Technology: Pole Position
... evenly distributed microcellular bubbles. The cross-sectional profile typical of an ideally foamed prototype part shows how cell structure formation takes place. The skin is firm and non-porous, while the core has a homogeneous closed-cell structure. The MuCell housing differs from conventionally produced parts by its lighter and slightly cloudy coloration. The process thus cannot be used without modification for quality surfaces, however it is ideal for in-mould lamination of films. Once Schrö...
Kunststoffe international, 2005-11-21, Injection Moulding Machine Control Technology
...hese areas will certainly have an effect on the control of larger injection moulding machines, and will therefore increase reproducibility. Because an injection moulding machine is often modified in the course of time, e. g. by the retrofitting of a core-puller control, the control must be expandable. The ideal solution is a platform concept, to which further modules can be added as required. Apart from capacity for expansion, the possibility of communicating with other systems is increasing in ...
Kunststoffe international, 2005-11-21, Injection Moulding Metal and Ceramic Powder
...time, components with shot weights of up to 500 g can be produced. Designers have all the options available that are familiar from plastics injection moulding: undercuts, threads, surface texture, helical gearing or details that can be achieved with core pullers. Similarly, hollow components can be produced by gas-assist injection moulding or fusible cores. What trends can be observed? On one hand, the shot weight of components is increasing and designs are becoming more complex. On the other, p...
Kunststoffe international, 2005-11-21, Injection Moulding Microstructured Functional Surfaces
...t, a test mould that would allow the questions to be studied was designed and made. It has a modular design so as to allow moulded parts ranging in thickness from 0.5 to 4 mm to be produced. The degree of microstructuring can be varied by swapping a core whose temperature can be kept under control. While this core, and thus the moulded plastics part, was being designed, special consideration had to be accorded to production aspects. Structures with dimensions far below 100 µm can be produc...
Kunststoffe international, 2005-11-21, Injection Moulding of Long-Fibre-Reinforced Thermoplastics
...el decreases. For thin parts the holding pressure can have an influence only in the case of high-speed injection. The fibre length decreases with increasing holding pressure (Fig. 6). A high holding pressure causes more movement of the melted liquid core than does a low holding pressure. Fibres with one end in the solidified boundary region and the other in the liquid core region are cut off. At the low flow rates of the holding phase the fibres are exposed only to limited forces and are much le...
Kunststoffe international, 2005-11-21, Injection Moulding of Microcellular Foams
...eometry was used for all tests. Clearly, the attainable reduction in density increases with increase in wall thickness. Given a comparable thickness of the compact outer layer, this can be explained by the ratio of compact outer skin to foamed core. In this connection, it is interesting that the maximum attainable reduction in density seems to be more or less independent of the polymer and is mainly influenced by the moulded part geometry, in this case the wall thickness. Irrespective of the des...
Kunststoffe international, 2005-11-21, Injection Moulding Technology for the Packaging Industry (2): Systems Approach
...osts but also the business objectives of the customer." Catoen is convinced that significant cost and time savings can only be achieved with an across-the-board systems approach. "Our machine, handling and hot runner technology forms the core of our service. For the additional equipment required beyond this, such as automated sequencing systems and other peripherals – we cooperate with leading industry partners. Customers do not have to worry about a thing. We purchase, integrate and ins...
Kunststoffe international, 2005-11-21, Injection Moulding Technology for the Packaging Industry (4): Differentiation of Products for Thick and Thin
...ion of the labels. The labels are pre-positioned independently of the injection moulding cycle by means of a patent mechanism. The handling system inserts them into the cavities, simultaneously with the removal of the parts already labelled from the cores. A movable removal platen minimises the required opening stroke. The linear drive of the robot also permits a high-speed and positioning accuracy. Operation is completely integrated into the Hylectric’s Windows-based machine console, Polaris Co...
Kunststoffe international, 2005-11-21, Injection Moulding Trends: Increased Complexity and Tighter Specifications
...mportant for customers not to be offered expensive special-purpose machines but appropriately-priced, flexible, series-produced machines. Another key factor is that processors must be able to use existing moulds and mould functions (such as core pullers) on new, state-of-the-art machines without need for major adjustments. System Suppliers Called For Although the supply of individual standard machines with low and medium-level clamping forces still accounts for by far the biggest proportion of...
Kunststoffe international, 2005-11-21, Injection Moulding under Clean Room Conditions: Machine and Process Technology for Medical Products
... in favour of the hydraulic concept for a two-platen clamping unit comes easily. The benefits versus other clamping systems are numerous: the clamping unit is cantilevered; hydraulics provide a high energy density (and permits the use of moulds with core pulls); in addition, the hydraulic clamping unit is well-suited for delicate coining operations. The two-platen technology offers a decisive and unique feature, since the actuating cylinders for the clamping unit are mounted to the back of the s...
Kunststoffe international, 2005-11-21, Injection Moulding Water Taps
...ejector mechanism, a requirement which necessitated the following properties for this particular application: - long hot-runner nozzles, because the ejector system must be bridged; - slim design, because interchangeable inserts, ejector pins and the core cooling device have to be positioned near the nozzle; - generous runner size, because even the tiniest streaks resulting from shear become visible after chrome-plating; - positioning of the gate in a narrow recess so as not to project beyond the...
Kunststoffe international, 2005-11-21, Injection Moulds Direct by Laser
...d mass-production mould is not ready on time. From CAD to High-Quality Injection-Moulded Parts in Three Days The Swedish automobile group Volvo Car Corporation worked with the Rapid Manufacturing Group of De Montfort University, England, to make a core and a mould cavity for injection moulding an adapter for a car (see Fig. 1). The inserts had a diameter of approx. 60 mm and were about 22 mm high with internal 90° angles which could not be produced by milling. In this case, the inserts wer...
Kunststoffe international, 2005-11-21, Injection-Moulded Packaging
...nt-coloured second component provides a colour contrast to the first. Over moulding can be combined successfully with the multi-daylight mould technique and this combination is already being used to produce 2-component CD packaging. With the aid of core-retraction technology, a differently-coloured frame is gated onto the box in a 4+4 mould. Greater use of over moulding can be expected in thin-section packaging. This poses new challenges for both mould-makers and machinery manufacturers. The adv...
Kunststoffe international, 2005-11-21, Innovation through New Processes
...ulated. Special Variants of the Injection Moulding Process and PU Processing In melt processing, multi-component processes have gained in importance. Examples are gas-assist technology and sandwich injection moulding, in which a molten or gaseous core component is injected into the fluid centre of a first polymer component so forming a sandwich structure. These processes reduce raw material consumption and component weight, compensate for shrinkage effects and combine properties of different t...
Kunststoffe international, 2005-11-21, Innovation with Polyurethane
...us is reinforced by a stable, dense GRP laminate sheath. The next layer is made of medium-density polyurethane. It is this material which basically allows the designed form to be produced and also gives the component its stability and lightness. The core is hollow. The add-ons for the joints and the guide rails for the brake are set into the foam to protect them from external influences. Innovative Process Concept Ingo Kleba, Roland Szasz and Inge Gabriel-Jürgens from IKV Aachen/Germany, who e...
Kunststoffe international, 2005-11-21, Innovative Design Opportunities for Magnet Technology: Injection Moulded Permanent Magnets Employing the Two-component Technique
...ning magnetic fields and guiding them in a controlled fashion. They can protect electronic assemblies in magnetically contaminated environments and also restrict the emission of magnetic fields by bobbins and transformers. They can be used as bobbin cores and shells to increase induction or to concentrate the magnetic field on a specific spatial zone (Fig.1). A number of characteristic values are set out in Table1 for the standard magnetic materials used. - BHmax is the energy product of the max...
Kunststoffe international, 2005-11-21, Integrated Automation: Manufacture Economically – Exploit Resources
...arm robot are fully exploited (Fig.2). Synergy from Combining Injection Moulding and RIM Technology Three areas developed jointly both the new SkinForm technology [2] and the golf production exhibited at the K2004. For the golf balls, the core inserts were first supplied to an industrial robot (Fig.3), which then placed them, from the non-operator side of the clamping unit, into the cavities of the 4-cavity mould. Integrated vacuum nozzles held the cores exactly in position. These were then ove...
Kunststoffe international, 2005-11-21, Integrated CAE Solution: Proper Simulation of Fibre Reinforcement
...dt@ikv.rwth-aachen.de Fig. 1. Simulated filling of the pump lid Fig. 2. Velocity profile and resultant fibre orientation across the cavity cross-section (schematic) Fig. 3. Fibre orientation in the core zone (left) and in the shear zone (right) Fig. 4. Selected measuring points on the pump lid Fig. 5. Agreement Comparison of measurement and simulation at 80 °C Fig. 6. Simulated bursting experiment conducted at room temperature and 13 bar, part "dry" (strain factors according to Pu...
Kunststoffe international, 2005-11-21, Interior Trim Parts made of Plastic: Common Ground between Automotive Technology and Design
...h, behaviour with change of climate and colourfastness as well as the fulfilment of safety regulations for the vehicle interior. Wilden AG works in this environment and classes its automobile division as the most important growth carrier next to its core business, medicine. A set of examples proves the achievements of Wilden AG as a supplier of high-quality interior solutions to the automobile industry. Accelerator pedal plate for the Porsche 911 In July 2004 Porsche brought the two new "El...
Kunststoffe international, 2005-11-21, Interview with Dr. K. Bourdon: “We Need to Strengthen our Corporate Identity”
...office but in the production halls. Now, we are on a good footing. Not only because of my work, but thanks to the efforts of the whole team in the USA. Kunststoffe: Where did you start out? Bourdon: It is important to penetrate to the core of a company. At Milacron injection moulding technology in the USA, the focus is on large machines and sales of electric machines from Fanuc. It is not possible to completely reorient a company through 180°. Realignment from large and electric machines toward...
Kunststoffe international, 2005-11-21, Interview: “Ensuring Sustainable Development”
...the business units. I see my role as that of a mentor who helps to break new ground and in so doing supports the realisation of new ideas. Kunststoffe: Why is BASF, specifically in the plastics area, making collaboration with customers a core priority? Feldmann: Successful collaboration with customers has always been at the heart of our business dealings and it is what made BASF into “The Chemical Company”. It was therefore always a “core” priority. However, our competitive environment is changi...
Kunststoffe international, 2005-11-21, Interview: “With the Four Pillar Strategy, We Are on the Right Track“
...on the worldwide Degussa distribution network. Kunststoffe: What are the top markets for the individual business units? Spindler: In principle, the business units support identical industries, but are targeted at specific segments of them. Core markets are the automotive industry (particularly for the Business Units High Performance Polymers, Specialty Acrylics and Methacrylates), followed by home, lifestyle and personal care – which is an important industry for Advanced Polymer Shapes -, as wel...
Kunststoffe international, 2005-11-21, Interwoven Divisions: Successful Company Network
...terial from the production scrap from fibre manufacture. The compounding activities fall under the Aquafil Technopolymers business group, also based in Arco, which the journalists visited on the second day of the press conference. Defining the Core Business Bonazzi sees growth in particular in the field of engineering plastics for high-grade applications. In 2003, the company produced 39kt engineering plastics, of which 63% was compounds, 33% straight polymers and 4% masterbatch. The export quo...
Kunststoffe international, 2005-11-21, Joint Technology
...transmitted are considerably higher for the same nominal thread diameter because of the greater cylindrical surface area of the insert (Fig. 3). The most important geometric factors influencing the load-bearing characteristics of an insert are the core hole diameter and the wall thickness of the plastic part as well as the outside contour of the insert. It is noteworthy that, except for a few hot-pressed inserts, all are very sensitive to variations in core hole diameter. The pull-out strength ...
Kunststoffe international, 2005-11-21, Large-sized Vehicle Parts
...ities to enable it to be deployed on a flexible basis with large parts and large moulds. These include a high-flexibility clamping system, the appropriate number of temperature-control circuits, and hydraulic versions of slides and core pullers, etc.” Details: www.battenfeld.com Dr. Ralph Sundermeier, Head of the Plastics Technology Division at the Braunschweig works The electric screw drive with a 138kW three-phase servo motor permits plasticization to be conducted in parallel on the hydrauli...
Kunststoffe international, 2005-11-21, Laser Sintering: For Tools, Looms and Water Cooling
...ctCast process, a new system for laser sintering of moulding sand is now available. The Eosint S 750 has two 100W lasers with dual-focus technology which allow increased building speed and productivity. The application of complex laser-sintered sand-cores with conventional mould making is demonstrated with the example of the main gear box of the new Airbus A380 engine, designed and developed by Avio S.P.A., Rivalta di Torino/Italy, and cast by Erreci Rapid Castigns S.r.l., Roletto/Italy (Fig.3)....
Kunststoffe international, 2005-11-21, Laser-sintering Technology: Series Production in Miniature
...These systems are generally used to build moulds for injection moulding and die casting, or to produce functional metal parts. - Eosint S systems are used to produce moulds and cores for sand casting using the DirectCast method. These systems involve the laser-sintering of resin coated foundry sand. Figures 4 to 8 show examples of the different processes. Contact: www.eos.info Title photo. Hearing-aid shells laser-sintered on an Eosint P 380 system Project partner: Phonak Fig. 1. Materials...
Kunststoffe international, 2005-11-21, Let’s Ask the Experts!
...red. For this reason, Kunststoffe/plast europe decided to ask the initiator of the WIT for some of the answers. What are the main areas of application for the WIT? !The WIT can be used for the production of rod-shaped and bent parts with hollow cores and integrated functional elements such as handles, armrests, pedals, pipes or for flat parts with struts (Fig.1). Components with structural reinforcements are also quite conceivable. What advantages and disadvantages does the WIT have? !Compa...
Kunststoffe international, 2005-11-21, Lightweight Construction: LWRT Technique for Car Underbody Covers
...rocessing stages, the product is equipped with heat protection and acoustic insulation elements. Component Properties and Requirements While the density of GMT and D-LFT materials ranges between 1.04g/cm3 and 1.13g/cm3, the porous core of LWRT materials has a density of only 0.4g/cm3 (Fig.4). The sealing film has a density of 0.9g/cm3 and the edges have a density of 1.0g/cm3. The total weight of the underbody cover amounts to only about 5kg for a surface area of more than 3m2. Moreover, despi...
Kunststoffe international, 2005-11-21, Logistics: Centralised Painting of Plastic Parts
...reduce colour mismatches and simplify logistics. This concept also offers plastics processors an interesting opportunity to gain a competitive edge. Tobias Rinza A concept is being debated within the automotive sector that concerns the location and core expertise of suppliers of coloured plastics: the centralisation of plastic parts painting, i.e. painting of all plastic parts in one location in the immediate vicinity of an automotive plant. The auto makers gain from a significant reduction in ...
Kunststoffe international, 2005-11-21, Machine Maintenance 2003: State of the Art and Future Trends
...report, a survey was carried out among a number of plastics processing machine manufacturers and some 30 plastics processors/converters. The results obtained form the basis of this trend report. Maintenance for the Processing Companies The core competence of a maintenance department in a plastics processing company is to document and exert an influence on the wear process as it affects the company’s machines and equipment. The maintenance procedures are governed essentially by the adopted mai...
Kunststoffe international, 2005-11-21, Machine Technology: Tandem Machine for Large 2K Automobile Components
...stem combines tandem technology and the indexing system on a two-platen injection moulding machine from the Quadloc Series. The indexing system, originally designed for production of PET preforms, is characterised by a mould carrier with two core halves that rotates around the horizontal axis, which provides the preforms with extra cooling from one additional cycle. The tandem technology employs a multi-mould carrier system (rotating centre platen) that permits simultaneous operation of two conv...
Kunststoffe international, 2005-11-21, Magnetic Fillers: Extrusion in a Magnetic Field
...y that is suitable for mass production. Flow Behaviour in a Magnetic Field The generation of a magnetic field in an extrusion die is shown schematically in Fig.2. The electricity supplied by a low-voltage mains unit flows through the coil with iron core and generates an adjustable magnetic field in its vicinity. On the test rig, the magnetic field was applied transversely to the extrusion direction. The magnetic induction reached approx. 1T (tesla). This test configuration was used to examine t...
Kunststoffe international, 2005-11-21, Maintenance of Plastics-Processing Equipment
Maintenance of Plastics-Processing Equipment High Availability is the Result of a Preventive Maintenance Policy Erwin Schwab and Ralf Marzineak, Iserlohn/Germany High plant availability and long useful life are the core competencies of the maintenance department as a service provider in the company, and the service business of the machine manufacturer. Do profit potentials in maintenance departments point the way from a pure cost factor towards an economic profit centre in the company? W...
Kunststoffe international, 2005-11-21, Market & Profiles
... the market for injection moulds for the production of bottle crates. Greiner Packaging, one of the largest producers of packaging applications in Europe, reports that this step is part of a strategy involving a stronger focus on the company’s core competence. Moreover, intense efforts in the European market by Mould & Matic Solutions called for co-operation. The company has many years of experience in the manufacture of injection moulding and thermoforming moulds for the production of cups and ...
Kunststoffe international, 2005-11-21, Market and Concept: Self-colouring of ABS
...element of the new strategy with which BASF aims to be successful on the ABS market involves large-scale plants with economical production processes and a portfolio that is trimmed to just a few large-volume standard products. The second core element concerns the regional availability of a globally uniform product. Through extensive, clearly defined cooperation with professional partner companies, it will be in a position to comply with even the most demanding customer requirements. That is the ...
Kunststoffe international, 2005-11-21, Market and Trends: Nanomaterials: Opportunities and Risks
... instance, - periodic 3-D architectures from nanoparticle crystallisation with periods in the wavelength range, e.g., for photonics, - processing of nanoparticles via flow processes involving nanoparticles with core-shell architectures or particle deformations, e.g., impact-resistant nanoceramics and photonic crystals, - nanoparticle dispersions and structure formation through nanoparticle linking for nanomaterials with controlled micromechanics, e.g., dispersions and polymer-based construction ...
Kunststoffe international, 2005-11-21, Market Campaign: Push into New Territory
..., according to its own figures, holds a share of 75% of the world market as a tooler for PET preform systems. Robert Schad, President & CEO of the company, said: we want to transfer our successful global business model in the PET market to other core regions, such as automotive and packaging. At K2004, Husky presents the new HyPET machines, fitted with the CoolJet cooling system, for production of preforms, which are based on the Hylectric series as platform and replace the G/PET systems. The fa...
Kunststoffe international, 2005-11-21, Market Growth Worldwide: Polymethyl Methacrylate (PMMA)
...hanks to its high stiffness, low weight and good processability, increasing use is being made of Rohacell polymethacryl-imide rigid foam, especially in the aeronautics and aerospace sectors. This foam, produced exclusively by Degussa, is used as a core material in high-performance composites, such as in the new Airbus A 380, as well as in a range of other Airbus models and Boeing's delta satellite transport rockets. Rohacell makes a key contribution towards more lightweight construction meth...
Kunststoffe international, 2005-11-21, Market News
...eton/UK, will be taken over by AKG Polymers of Vroomshoop/The Netherlands, and at the same time, Synbra Polymers will cease to exist. Synbra Polymers is a member of Synbra Group BV. After its removal from its core business, the group decided to divest its PP compounding business in Congleton. After careful consideration, AKG Polymers, a member of Aufderhaar Kunststof Groep BV, has decided to shut down the production at Congleton and to integrate the activities into their Vroomshoop plant instead...
Kunststoffe international, 2005-11-21, Material supply: Storage, Conveying and Metering
...tion are typical problems that can occur when bulk goods are stored in silos. A distinction is drawn between two different flow profiles during the outflow of bulk goods from a silo: mass flow, where the entire contents of the silo move, and core flow, where only the goods in the vicinity of the outlet move. Silos with the corresponding mixing facilities can also be used for batchwise or continuous homogenisation, however. Introducing dry air or, where appropriate, an inert gas (nitrogen) to the...
Kunststoffe international, 2005-11-21, Materials and Processes: Electrical Engineering in Transformation
... conductive polymer, to which metal wires or ribbons are usually applied as metallic shielding. The outer cable sheath is formed by a mechanically robust, insulating plastic layer. These construction principles also apply in essence to multi-core cables. While in low voltage applications cost aspects dominate the choice of materials and processes on the mass market, the high-voltage sector has a different profile because of the very high technical requirements together with comparatively low pro...
Kunststoffe international, 2005-11-21, Maximum Precision for Microparts
...mping platens are both cast parts, and the two machine series referred to include facilities for adjusting the platen parallelism, since this is a key factor that influences moulded part quality. The connections for the core pullers have been applied directly to the moving mould platen, ensuring short hydraulic paths, high dynamics, rapid transmission times and almost loss-free axle reactions. Modular and Precision Injection Unit Since the injection units are designed on a modular basis, they ...
Kunststoffe international, 2005-11-21, Medical Technology: High-precision Lightweight Design
... represent a suitable approach to meet the above requirements. To achieve the extremely high stiffness at a low weight, the orbital arc was designed as a sandwich construction with skins of fibre-reinforced composite materials and a rigid foam core (Fig. 2b). Before the design and calculations for the orbital arc could be started, an experimental study had to confirm that the materials to be employed would have no effect on the magnetic field in the MRT. The material combination of glass fibre ...
Kunststoffe international, 2005-11-21, Metallised Synthetic Fibres: Shielding Electromagnetic Radiation
...n values should be expected with an isotropic layer structure. Shielding Values the Same as for Steel-fibre Composites Composite types 0 and 3D are three-dimensional, continuous conductive networks, while type 3 only has a continuously conductive core. As conductivity measurements on type 1 and type 2 perpendicular to the nonwoven layers show, there is little or no contact between the conductive layers, since the volume resistivity values are above 106Ωcm. The actual conductivity values L...
Kunststoffe international, 2005-11-21, Microinjection Moulding: Plastification Units for Minimum Shot Weights
...200mm³ is best accommodated with a maximum screw diameter of 6mm. The screw diameter of screw-plunger injection moulding machines however, cannot be reduced willy-nilly, since transmission of the torque requires a minimum diameter of the screw core and the screw flights must be wide enough to accommodate pellets. Therefore, the smallest modern injection units have screws with a diameter of about 14mm – clearly unsuitable for the production of micro components with their typical shot weights. I...
Kunststoffe international, 2005-11-21, Microsystems Technology: In-mould Assembly via Microinjection Moulding
...oduced via 2-component moulding by pairing incompatible materials. Hard-soft combinations are always of interest where a defined sealing action must be achieved. Structures for microfluidics and cavities with undercuts can be created via the lost core technique. In addition, functional inserts can be incorporated [3]. Mould with Monitoring Capability The injection mould used for these investigations is shown in Fig. 4. The experimental mould is a split-cavity mould from Hasco Hasenclever GmbH +...
Kunststoffe international, 2005-11-21, Minutes of a Development Record: From Zero to the Road in Seven Months
...chnique that makes very light and dimensionally stable models with hard outer skins possible. In addition lower manufacturing costs result because of use of economical materials. Modelling Work on the 1:1Model For this first the NCprograms for the core production had to be computed in Tebis. After production of the core by milling the actual outside layer was applied so that after hardening there was a 1 to 4mm thick layer on the model. The milling treatment of the outer skin took place in a s...
Kunststoffe international, 2005-11-21, Model Test Systems: Wear Testing on Plastics processing Machines
... be tested simultaneously. In addition, a phased abrasive loading is possible in order to remove corrosion layers. The test specimens are electrically insulated so that electrochemical corrosion with electrical voltage can be studied. On the core is mounted the specimen holder for ten specimens, distributed uniformly around the circumference (Fig.3). The plate-shaped test specimens are clamped with two adapter rings. A mushroom-shaped manifold head upstream of the specimens distributes the melt ...
Kunststoffe international, 2005-11-21, Modelling of Part Properties: Physical Foaming for Cost-effective Injection Moulding
...ngths of microcellular foams. Flexural Strength: Sandwich Models As mentioned above, microcellular foams are characterised by a dense outer zone (Fig.1). They are thus sandwich structures comprising an unfoamed outer skin and foamed core. Since the flexural properties are substantially dependent on the outer fibre properties, it can be expected that such a sandwich structure will have a higher flexural strength than an equivalent isotropic foam. Sandwich models should thus be applied for model...
Kunststoffe international, 2005-11-21, Modular Clamping Force: Why a Mould Maker Needs His Own Injection Moulding Machines
...xtra would be very useful for installing and removing large moulds. The Sauer pilot plant is already high enough for loading the machine with moulds from above. It was much more important to have a programmable core-puller, or to expand the standard software with the “Engel Monitoring System” (EMS). This software package is used, for example, as an interface for “Teleservice” remote machine diagnosis and maintenance, as well as for managing all the mould-specific process data on a central comput...
Kunststoffe international, 2005-11-21, Modular Drive Systems in the Spotlight
...cally direct-driven five-point toggle system. The injection and dosage motion is also instigated directly by servo motors via a gear stage for converting the high torque. Core pullers and special motions on the mould which were formerly integrated hydraulically into the moulds, will continue to be operated hydraulically in the future. For the optional hydraulic secondary functions on the machine, a special energy-saving, small-accumulator hydraulic system has therefore been developed that can be...
Kunststoffe international, 2005-11-21, Modular Drive Technology
...atively quiet. Hydraulic drives are highly suitable for linear motion and offer a very high power density, as is needed for short injection times. A single motor can drive several functions in sequence via different valves, for example ejectors and cores. Hydraulic drives require a low installed total power, the investment costs are low and they take up only a small amount of space. The Optimum Drive for Every Section An injection moulding machine carries out a total of six movements: - plasti...
Kunststoffe international, 2005-11-21, Modular Drive Technology for Injection Moulding Machines
...smission, and then, by changing the direction of rotation of the electric motor, the linear injection movement is carried out via a control pump. A much smaller compact hydraulic central unit, such as that used as a decentralised hydraulic unit for core pulling movements with electric machines, powers the drive systems for the ejectors, core pullers and nozzle unit and, if required, for the quick-clamp system. The machine thus provides an alternative both to standard all-hydraulic injection mach...
Kunststoffe international, 2005-11-21, Modular Systems for Hydraulic Drives: Tailor-made “off the Peg”
...able of performing movement sequences for a total of six functions: - plastication of the plastic being processed, - injection-unit advance and contact pressure, - injection of the melt into the mould, - mould opening and closing, - operation of core pullers, and - ejecting the parts. Plastication, injection and mould opening and closing are termed the primary movements of the injection moulding machine, because they have the biggest effect on cycle time and part quality, and are also the most e...
Kunststoffe international, 2005-11-21, More Light
...velopment of innovative products: “There is no substitute for imagination.” On the other hand, Elkamet has its injection moulded parts produced by external suppliers because it has no core competence in this segment. “There are others who can do it better than we can”, says Michael Parsch. The mould-building work for the rotational units is also outsourced when no specific know-how is involved. Independence is another factor at the top of the priorities list for Elkamet: They have no customer ac...
Kunststoffe international, 2005-11-21, More Reliable Washing
...gineering. The Klinger company succeeded in having all the movements, e.g. the moving elements in the slides, controlled via the horizontal movement of the machine. This made it possible to avoid an elaborate and expensive structure with hydraulic core pullers, for example. The two-cavity mould with slides and drafts is shown in Fig.2. Flame Retardance Essential A further key point is the electrical reliability of the switching contacts. This places particular requirements on the flame retarda...
Kunststoffe international, 2005-11-21, Morphology and Mechanical Properties: Blends of Polyamide 66 and Syndiotactic Polystyrene
Blends Blends of Polyamide 66 and Syndiotactic Polystyrene Morphology and Mechanical Properties. Blends of polyamide 66 and syndiotactic polystyrene only display enhanced mechanical properties if good compatibility exists between the two materials and an optimum morphology can be achieved. Different compositions of these blends were investigated in a study employing a compatibility enhancer. Materials of this type are attractive for the production of automotive components that are exposed to hi...
Kunststoffe international, 2005-11-21, Mould Design: Safely Warp-free
... the visible side faces the fixed mould half. Because of the fastening holes, and for neat deforming without drafts in the high side walls, two large side slides are required. For gating the part, a hot-runner nozzle is used, which penetrates the core at the fixed half and feeds into a cold-runner manifold. This runner manifold leads to three gating points; two in the upper corners and one centrally in the panel ridge. This mould design reduces the overall height of the mould and reduces the ope...
Kunststoffe international, 2005-11-21, Mould Preliminary Costing: The Devil is in the Detail
...imes for each individual machining operation. To determine information about this, the cavity was broken down into all its individual modules. Starting with the mould platens, the cavity (Fig.1), is further analysed into mould inserts, cores or ejector pin faces. The parts are considered individually and assessed according to their complexity. Complexity is determined from several criteria, such as surface form (ribs, free-form surfaces or the like), fit and dimensional accuracy, and size. Furth...
Kunststoffe international, 2005-11-21, Mould Technology: Better Performance for Two-Component Technology
...i Kunststofftechnik GmbH, Munich, has continued to develop multiple turnover technology so that its advantages can be transferred consistently to the multi-component range. In the closing unit two moulds are used arranged one behind the other. The core sides of the moulds are installed on a rotating central block, which is between the mould clamping plates. The two mould dies are fastened to the mobile and/or to the firm clamping plate (Fig. 6). Hydraulic cylinders move the central block linearl...
Kunststoffe international, 2005-11-21, Mould-making 2000
...ction of Elastomer Mouldings The injection moulding of mini- and micro-articles in liquid silicone or elastomer blends is the main business of Hefner GmbH, Wels/Austria. Examples of such parts, weighing far less than 1 g each, consist of the single-core seals for cable glands, employed in the car industry, or syringe pistons, O-rings, and sealing plugs for medical applications. These tiny mass-produced articles have to be produced fully automatically for reasons of costs. State of the art is th...
Kunststoffe international, 2005-11-21, Multi-component Injection Moulding: New Properties through Rigid/Flexible Combinations
...ral division of the shell more or less in the middle of the phone. In other words, it is split up into an upper and lower half, which means completely redesigning the moulds. Because of this physiognomy, the designers had to provide a high core in the mould. The melt pressure had to be optimally adjusted to ensure that the core did not move during the injection process. Balda managed to do this by first carrying out a comprehensive mould flow analysis that helped to exactly fix the position of t...
Kunststoffe international, 2005-11-21, Multi-component Moulds: More Colour and More Functions
...The processes can essentially be distinguished by the way in which the components are combined in the cavity, i.e. by the sequential method or the addition method. With the sequential method, a short shot of plastic to form the skin has a compatible core material injected in after it or, alternatively, the injection stream is switched between two components after specific intervals. The aim of the two-component sandwich injection moulding process is to produce composite parts in two materials th...
Kunststoffe international, 2005-11-21, Multi-component Technique: Safeguarding the Future through Process Integration
Special Safeguarding the Future through Process Integration Multi-component Technique. Multi-component injection moulding has gained enormous importance over the last fifteen years. This is due both to the development of sophisticated products and to the efforts being made generally to economise. The combination of well-known processes, such as sandwich moulding with injection-compression moulding or the fluid injection technique, offers fresh possibilities for lowering costs and creating inn...
Kunststoffe international, 2005-11-21, Multi-Material Mould with Rotary Mechanism
...off nozzles. The gate location was selected such that the melt flows uniformly around the first shot, thereby avoiding an unilateral force as much as possible (Fig. 4). It was not possible to securely hold the headset-shaped first shot on the mould core, because it was not permitted to project beyond the overall wall thickness of the finished part. It could be held only by the pins near the gate and the preload in the second moulding position. Since it was not possible to predict in advance the ...
Kunststoffe international, 2005-11-21, Multiprocess Technology: Production Solution for Complex Air Intake Systems
...n turbo version. At a very early design stage, it became clear that the conventional, very efficient methods used today for industrial mass production of plastic air intake systems – such as manufacturing the unit in two half sections or fusible core technology – were not suitable for meeting all the specified objectives. The relevant moulds were either too complex and therefore too expensive (it would not have been possible to optimise the ducts sufficiently to obtain the required low pressure ...
Kunststoffe international, 2005-11-21, Nanocomposites - En Route to Application
...ispersed in different types of media as host/guest systems. In this way, it proved possible to generate innovative metal colloids where the particle diameter of the metal colloids increases with the degree of polymerisation of the polyglycerin core. Sample quantities and customised, modified polyglycerol are being supplied by the Freiburg company, Hyperpolymers GmbH. Carbon Nanotubes and Exfoliated Layered Silicates Anisotropic nanoparticles with a very high aspect ratio are especially attract...
Kunststoffe international, 2005-11-21, New Generation of Machines: Reaching the Goal in a Distinctive Way
...itor with large reading angle. The keys are clearly arranged in groups and have sufficient free space to include customers' preferences. Careful Attention to Ease of Use For control of mould ancillary equipment (e.g. core pullers), which is often a problem all-electric machines, a compact, powerful hydraulic unit is available (Fig.7). The moulds used on hydraulic machines can therefore be transferred to the Elion. No complicated conversion to electric or pneumatic drives is necessary. The ...
Additional information about this tradename, like producer contact address, etc. can be found at www.materialdatacenter.com. For access to this extra information a registration is requested. Free online registration is available.
Note: the information in Material Data Center was collected with maximum care, based on information from material producers. They are subject to short term changes at the market. There is no warranty for the correctness of this information. In no way this information can be seen as a legal advice, whether certain tradenames are protected or not.