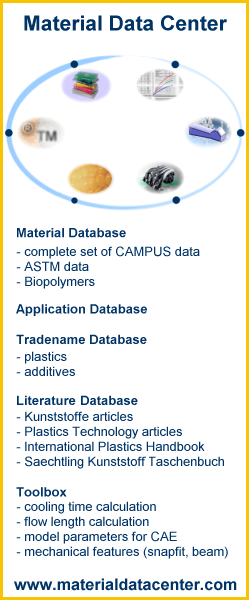
Material datasheets available free. Online registration at: www.materialdatacenter.com
Velocity - PA6, PA66 - PlastiComp, Inc
Material Data Center is a leading international information system for the plastics industry. Material Data Center offers a comprehensive plastics database, calculation tools, CAE interfaces, a literature database and an application database. For more information about Material Data Center visit www.materialdatacenter.com.
A search for "Velocity" in Material Data Center leads to the following information:
|
|
Material Data Center offers information about the following products with the requested tradename. To view a datasheet, please click on the relevant product.
...n the mold by a special film feeder. To fix the film in the mold, a twelve-part clamping frame concept is used. This fixes the film in the mold using a precisely defined sequence of velocity and position control (Fig. 3). The transfer film is now laid wrinkle-free in the mold under vacuum. When the two films have been positioned, the mold halves are closed and the films are backmolded with PC (grade: Makrolon Ai, supplier: Covestro) at up to 300 °C. Due to the high temperatures and pressures, th...
Kunststoffe international, Avoiding Shutdowns
...e injection molds, pipes, heat exchangers or other equipment. They can be easily connected at the feed and return points to the mobile Comprex unit via adapters. In the defined pipe section, first water (or another aqueous medium) flows at low velocity, before it emerges again at the discharge point. Pulse-controlled, filtered compressed air then enters the system via the feed point. This creates packets of air and water blocks, which flow through the cleaning section at high velocity of 10 to 2...
Kunststoffe international, Data Management at the Tool
...ct software cycle counter or for detecting a tool crash during transportation. The machine cycle, faults and incorrect or unauthorized use can thus be indirectly recorded and stored. The tool velocity (red curve) is shown at the left (Fig. 5), it was registered via the machine control unit and, the velocity calculated with the ImPro module is shown at the right. Depending on the assembly option, the ImPro module can perform an independent position determination in the XYZ direction of the Earth’...
Kunststoffe international, Excellent Resistance at Reduced Weight
...more, both an increase in the injection speed and an increase in the nozzle temperature cause higher component weights. This is due to increased shear as a result of the increasing velocity gradient with increasing volume flow, which damages the hollow glass spheres. A higher melt temperature reduces the viscosity – the resulting increased shear of the molding compound in the area of the block flow explains the higher component weights. In addition to the component weights, the mechanical proper...
Kunststoffe international, Flexible Guiding Systems for Cooling Air
In order to avoid bubble ruptures during the production of blown film, the velocity of the cooling air is often ‧reduced, which has a negative effect on the plant efficiency. The use of air guiding systems (AGS) can prevent such bubble instability. A novel air guidance system was developed at IKV in Aachen, Germany, using iris diaphragms in order to increase the cooling efficiency of blown film extrusion and thus improve the productivity of an existing plant. The applications of blown film range...
Kunststoffe international, Foamed and Still Extruded in One Step
...g. It is thus initially distinctly higher with foamed profiles. Under industrial conditions, i. e. with an increase of the take-off velocity and energy-efficient extruders, however, it can be assumed that specific energy consumptions can be significantly reduced. Environmental Life-cycle Analysis In addition, a comparative environmental life-cycle analysis was performed for a PVC window with the standard dimensions 1.23 m x 1.48 m and an assumed useful life of 30 years. It was assumed that, due ...
Kunststoffe international, Ultrafast 3D Printing
...significantly higher process speed can be achieved. For controlled printing in curves and corners, as well as at position jumps without material discharge, the output rate must be controlled depending on the path velocity. Because of the sluggish plastication behavior of an extruder, it is not useful to perform a volume change via the extruder speed. An upstream unit for a velocity-dependent material output of between 0 and 100 % has been developed. The patent-pending unit is currently undergoin...
Kunststoffe international, Zero-Waste Concept for Carbon SMC
...lacement and reaction force were determined using a load cell. The component behavior under monotone, quasistatic loading was investigated by means of a critical load path in the Z-direction with a test velocity of 2 mm/min. To estimate the expected lifetime under service conditions, cyclic fatigue tests were performed in the critical Z-direction (Fig. 5). These tests were performed under sinusoidal loading (5 Hz), both displacement and force controlled. Optimized Press Forming The first investi...
Kunststoffe international, 2005-11-21, A Comparison of Hybrid Machines
...reduction. Injection, particularly in the case of high-performance machines, requires a high power that lasts only briefly and can be called up independently of the other movements. Highly dynamic acceleration of the screw to up to 1000 mm/s advance velocity is required. In the case of a 2000 kN machine alone, this demands about 150 kW, but only for 100 to 200 ms. Electric drives are, for the medium-term future, limited to a maximum of 400 mm/s advance velocity. The required 1000 mm/s velocity, ...
Kunststoffe international, 2005-11-21, Automobile Construction: A Substitute for Sheet Metal
...polyamide 6 semi-finished materials by thermoforming Fig. 2. Viscosity characteristics according to ISO 11443 Melt viscosity of the intrinsically viscous polyamide 6 durethane DP2-2140/15 Z H2.0 as a function of shear velocity
Kunststoffe international, 2005-11-21, Comparative Study: Virtually Equal in Terms of Precision
...re transducer in front of the screw, and an accumulator for high injection ve-locities of up to 400 mm/s. In the injection phase, the energy stored in the hydraulic accumulator ensures high acceleration; active retardation of the screw advance velocity is provided by the position control of the screw. To achieve optimum melt quality, the studies were carried out with screws with L/D 20 and new quality process units. The machines under considera-tion recognise the changeover point in the control ...
Kunststoffe international, 2005-11-21, Continuous Monitoring of Quality Parameters
...ng of Quality Parameters Inline Monitoring in the Extrusion Process Using Ultrasonics Ingo Alig and Dirk Lellinger, Darmstadt/Germany, Richard Lamour and Jürgen Ramthun, Leverkusen/Germany An ultrasonic technique for inline measurement of the velocity and absorption of longitudinal waves during the extrusion process was developed. For PS it was possible to differentiate between the different melt-flow indices. For the PE/glass bead composite a significant dependency of both measured variab...
Kunststoffe international, 2005-11-21, Control Functions with Artificial Intelligence
.... The preset pressure profile is reproduced from cycle to cycle by corresponding acceleration or delay of the screw advance rate at extremely small time intervals. The filling of the cavity is no longer controlled by two different methods (first the velocity control and, from the change-over point, pressure control), but by only one. This has advantages for the part quality (Fig.6). Viscosity effects on the melt are compensated, which can otherwise have an effect on the density and shrinkage beh...
Kunststoffe international, 2005-11-21, Controlling Injection Moulding Processes in Real Time
...r each individual nozzle can be input as a reference pressure curve via a touch-screen monitor, independently of the pressure profile for the other nozzles. This input replaces the parameters used for conventional injection moulding (e. g. injection velocity, injection time, holding pressure and holding pressure time. The control unit reads the output signal from the pressure sensors (P1, P2, see Fig. 1), compares this with the desired pressure profile and sends a signal to a hydraulic servo val...
Kunststoffe international, 2005-11-21, Cooling Time Reduction by Foam Injection Moulding: It Can Be Done Faster
...oaming process is influenced by many different factors. In addition to the combination of polymer and blowing agent, the following process parameters particularly influence the development of the foam structure [2]: - melt temperature, - injection velocity, and - concentration resp. pressure of the blowing agent. The test plan is shown in Table1. It is a full-factorial, statistical experimental plan with a centre point and variation of the parameters at two levels. The abbreviation m represents ...
Kunststoffe international, 2005-11-21, Cross-linked Polyethylene: The Right Pipe System
...e strength. Experts speak of the creep strength, which for PVC and PE decreases rapidly with increasing temperature. It is even forbidden to use PVC for compressed air supply, since a bursting pipe produces sharp-edged splinters at high velocity, which represent a danger to bystanders. Although polypropylene (PP) has a higher creep strength at high temperatures, it must be installed in an absolutely stress-free condition to prevent subsequent bursting. At low temperatures of below 5°C, PP is ev...
Kunststoffe international, 2005-11-21, Design of Single-screw Extruders
... the material. In the feeding section, the granules rub on the wall of the barrel and the screw. This friction influences the feed characteristics and the behaviour in the delay zone. It is dependent on - the local pressure, - the temperature, - the velocity and - the friction pairing [2]. The friction pairing consists of the screw and/or the barrel with its surface properties on the one hand and the granules on the other. A high friction coefficient on the barrel and a small friction coefficien...
Kunststoffe international, 2005-11-21, Determining Wear Mechanisms
...ymers and FPC were conducted to establish the correlations between material and wear properties. Erosive wear occurs when solid or liquid particles impact on surfaces and is normally characterised by material loss that depends not only on particle velocity and impact angle but also critically on the type of surface of the material. The use of fibre-plastic composites for applications in which high erosive wear is expected (turbine blades, rotor blades) is prevented by erosive wear mechanisms t...
Kunststoffe international, 2005-11-21, Dynamic Frictional Data
...nsity of the bulk material. From Measurements to a Practically Useful Equation To allow computer processing of the plastic's frictional properties, it is necessary to determine the dependence of the friction values on temperature, pressure and velocity by means of a statistical experimental design and regression analysis. The regression analysis yields an equation containing all the important relationships between friction factors and influencing parameters. It takes into account not only ...
Kunststoffe international, 2005-11-21, Economical Production of Barrier Film
... temperature and dwell-time range should be ensured as well as a low pressure drop and good self-cleaning properties. An ideal solution here is the binary stack distributor. As shown in Fig. 1, through the binary division, the melt with the highest velocity is turned into the melt with the lowest velocity after each division. As a result, the temperatures are homogenised. In addition, the stack-type predistribution means that the blown film die can be designed relatively low down. Whereas the ov...
Kunststoffe international, 2005-11-21, Effect of Structure-borne Sound: Acoustics of Plastics parts
...agram. The results for the polypropylene in the study (grade: Polychim B 10 FB, manufacturer: A. Schulman GmbH, Kerpen/Germany) is shown as example. It can be seen that, as the angle increases, the absolute amplitude of the surface velocity increases and the associated frequency becomes smaller. The reason for this lies in the fact that the geometrical stiffness of the part decreases as the angle increases. A comparison with the results of the conditioned polyamide (grade: Durethan B 30 S, manuf...
Kunststoffe international, 2005-11-21, Efficient Project Development
...o be mounted more easily on the handlebar. Considering the gate position, the spacer plays a key role in selection of suitable simulation software. The filling study in Fig. 7 clearly shows the so-called "hesitation effect", i. e. the lower velocity and thin section both contribute to rapid cooling, which further reduces the available melt cross section. The sudden pressure drop in the flow constriction slows down the flow front. 2D mid-plane versus 3D method: Fig. 8 shows filling simul...
Kunststoffe international, 2005-11-21, Exhibition Preview: North American and Canadian Products at K 2004
...hemicals over a temperature range of -40 to +160°C; further testing to 17°C is under way. It is targeted for under-hood applications such as ducts and hoses, seals, hydraulic hoses, and constant-velocity-joint (CVJ) boots. Initially, two grades are available with 60 and 90 Shore A hardnesses. GLS Corp., McHenry/Illinois, will unveil its Versaflex OM 6100 series of TPEs for nylon overmolding. They are claimed to provide a superior bond to most types of standard and modified nylons. Other features...
Kunststoffe international, 2005-11-21, Expansion Injection Moulding: Amazingly Thin
...lly filled at a melt pressure of 1000bar. The subsequent pressure decrease results from the balancing out of the pressure differences existing between the cavity and the screw antechamber at the end of the filling process. The mean flow front velocity when filling the cavity does not remain constant either, but decreases rapidly as the filling level rises. In the filling process up to DS 3, it is still around 5000mm/s, but drops to nearly half (approx. 2800mm/s) by DS 4. - These test results sh...
Kunststoffe international, 2005-11-21, Expectations and Performance: The Importance of Numerical Simulation
...ediction of the viscosity values during the start-up operation [6–8]. Simulation of Flow and Solidification Behaviour In the simulation of flow and solidification behaviour in plastics processing, users are interested in pressure, temperature and velocity distributions and the prediction of flow-induced defects such as weld lines and trapped air. At present, modelling for this simulation is carried out on a macroscopic level by solving the conservation equations for mass, impulse and energy. Th...
Kunststoffe international, 2005-11-21, Fast and Reliable
...ining pressure for welding the plastics. The complete system is shown in Fig.2. An analysis was made of the welding process for each of the material combinations listed in Table1. During the welding trials, the three parameters, laser power, travel velocity of the laser and joining pressure were systematically varied. The housing geometry had a hole in its base to enable the welded parts to be subjected to both tightness and bursting pressure tests. In addition, microscopic examinations were mad...
Kunststoffe international, 2005-11-21, FE Method: Design Concept for Stacked-type Spiral Dies
...all-slipping materials, the geometry is determined such that the maximum shear rates and shear stresses do not exceed the critical lower threshold for the stick-slip range. In addition, further parameters are available for the design, such as velocity, shear stress, pressure gradient and shear viscosity. Experimental Results The simulation results that were determined by the design strategy presented here were used to transform the optimised distribution system into a three-layer stacked-type ...
Kunststoffe international, 2005-11-21, Fibre-reinforced Plastics: Lightweight and Corrosion-resistant
... for Materials, Explosives and Lubricants (Wehrwissenschaftliches Institut für Werk-, Explosiv- und Betriebsstoffe = WIWEB) was to establish the behaviour of multi-directional glass fire composites under the action of force in the low and medium velocity range as well as their damage tolerance. In order to achieve a differentiated assessment of the influence of the sewing threads, investigations were conducted on both stitched and non-stitched laminates. Testing Impact Strength The laminates in...
Kunststoffe international, 2005-11-21, Film extrusion: Predicting the Properties of Blown Film
...o orientation of the molecules in both stress directions: first of all, there is an orientation in the circumferential direction due to the expansion of the film, and secondly an orientation in the extrusion direction due to the increase in the film velocity. These orientations are primarily responsible for the mechanical properties of the blown film [1]. However, not all orientations introduced into the bubble expansion zone are also subsequently present in the film. Because of the elasticity o...
Kunststoffe international, 2005-11-21, Fluid Injection Technique: Manufacture of Multilayer Media Lines
...s determined by the flow processes in regions E and F. It is therefore also influenced by, apart from the process parameters of the FIT, the process and material parameters of the core component. In this context, it should be noted that the velocity profile of the core component of the two-component flow in region E can also be influenced by the skin component. A block-shaped velocity profile of the core material – analogous to the residual wall thickness with one-component gas-assist and one-co...
Kunststoffe international, 2005-11-21, Fluid Injection Technique: Understanding Residual Wall Thickness
...tem developed at the Institute for Plastics Processing (IKV at Aachen University) that permits flow-controlled injection of water. The water flow rate was 26 l/min. The remaining process parameters such as melt temperature (T=240°C), injection velocity (v=120cm³/s) and delay time (3s) were kept constant for all gas-assist and water-assist trials. Building on the knowledge that the shear viscosity, the pseudoplasticity, the stretching viscosity, the elasticity of a material and the interfacial t...
Kunststoffe international, 2005-11-21, Fluoropolymer Prevents Flow Instabilities
...ique, which is conventionally used to measure the flow velocities of gaseous media, was adapted at the Institute of Polymer Materials, Friedrich-Alexander University Erlangen-Nuremberg, to make it suitable for polymer melts. Because it measures the velocity with high spatial and time resolution, the LDV technique allows the flow behaviour to be determined with a high level of precision in the molten state. For example, it enables a direct observation of whether a polymer adheres to the die wall ...
Kunststoffe international, 2005-11-21, GIT, Sandwich and Two-component Moulding in Practice and Research: Correct Application of Multicomponent Processes
... is illustrated by Fig.7. The graphic shows the results of an FE analysis that was produced with the Abaqus program. In the simulation, PC+ABS was injected as first component, onto which a TPE-E was moulded as second component. The injection velocity determines how strongly the molecules are oriented. The degree of orientation in the interface has an effect on the quality of the bond. Additional shear energy is introduced into the material, for example by high injection velocities, in order to r...
Kunststoffe international, 2005-11-21, High-efficiency Polymeric Foam: Improving Occupant Safety
...ad impact protection requirement (FMVSS201u). Safety Requirements: Segmentation and Solutions In a free-motion impact, the impactor (e.g. the free-motion headform in FMVSS201u or the instrumented pendulum in ECE R21-FMVSS201) is moving at constant velocity before impact [3]. FMVSS201u tests at component level showed that high-efficiency EA countermeasures enable optimum energy management to be achieved in terms of injury levels, while minimising weight and space utilisation (Fig.2) [4]. The ad...
Kunststoffe international, 2005-11-21, High-performance plastication: High-speed Screws in Injection Moulding
...ection moulding machine from Krauss-Maffei Kunststofftechnik GmbH, Munich/ Germany. The screw is driven by an asynchronous motor. The system is capable of screw speeds of 1000rpm at a screw diameter of 50mm. This corresponds to a circumferential velocity of 2.6m/s. In extrusion, screw systems are often matched to the operating point or to the material, but for injection moulding, universal screws are generally used. Series of experiments were therefore conducted to investigate how a conventional...
Kunststoffe international, 2005-11-21, Hyperelastic Elastomers
...The measurements show that the materials are virtually incompressible. The deviations of the measured values from the theoretical value of 0.5 can probably be attributed to measurement uncertainties and microscopic air inclusions in the specimens. Velocity-Dependence of the Mechanical Data In the tests on silicone elastomers, it was not possible to detect any velocity dependence in the stress-strain curves within the range measured. As an example, Fig. 1 shows with the stress-strain curve for ...
Kunststoffe international, 2005-11-21, Improved Injection Moulding Simulation
...stallisation temperature were, following the cooling and crystallisation experiment, heated back to the melt temperature (Tm = 180°C) in steps of 0.5 K/min. The storage component (G') of the shear modulus was determined with the same angular velocity and shear amplitude as during the cooling experiment (Fig. 2). The heating curves in Fig. 2 show a steep drop in the storage modulus by about four orders of magnitude in a relatively narrow temperature range. This effect can be attributed to...
Kunststoffe international, 2005-11-21, Influence of Process Conditions on the End-Use Properties of Injection Mouldings: Material-based Process Control Recommended
...e: 20K/min, purge gas: N2; mean value from two measurements Fig. 4. Morphological structure as a function of processing; material: POM Copo (MFR: 27g/10min), transmitted light/polarisation, thin section: 10µm. Left: injection velocity = 2cm3/s; right: injection speed = 40cm3/s Fig. 5. Rheological investigation: Melt viscosity as a function of processing; comparison of the moulding compound before and after processing Table 1. Machine parameters for producing specimens in POM Copo (MFR: 27g/...
Kunststoffe international, 2005-11-21, Integrated CAE Solution: Proper Simulation of Fibre Reinforcement
...assfibre-reinforced PA 66 (Durethan AKV 50 H2.0, manufacturer: Bayer). In the case of glassfibre-reinforced thermoplastics, flow processes during injection moulding induce directional fibre orientation in the cavity. On account of the parabolic velocity profile, this leads to a stratified build-up of fibre orientation that is symmetrical to the midplane of the cavity: in the centre of the cavity, the fibres become oriented perpendicularly to the direction of flow. The reason for this is extensi...
Kunststoffe international, 2005-11-21, It’s the Benefit Alone that Counts
...injection profile (left), acceleration phase (centre) and braking phase (right) for the Ergotech El-Exis E and an all-electric machine Andere elektrische Maschinen = Other electric machines; Einspritzgeschwindigkeit = Injection velocity; Zeit = Time; Beschleunigung = Acceleration; Abbremsung = Braking Table 1. Performance characteristics for the regulation chamber
Kunststoffe international, 2005-11-21, Let’s Ask the Experts!
...he injector diameter and illustration of an “automatic ramp” in the area of the feed line, in or outside the mould Volumenstrom = volume flow; Druck = pressure; Austrittsgeschwindigkeit = water velocity at orifice; Durchmesser der Injektoröffnung = diameter of the injector orifice; Beispiel für eine automatische Geschwindigkeitsrampe zu Beginn der Wasserinjektion = example of an automatic speed ramp at the beginning of the water injection Fig. 3. Injector variants with drawing and piercing pin...
Kunststoffe international, 2005-11-21, Many Variations
...ruder with a dosing system and a chill roll with a water bath underneath (Fig. 1). Subsequent simultaneous stretching is carried out by means of a discontinuously operating stretching frame (Fig. 2). With this device, the parameters of stretching velocity, stretching ratio and stretching temperature can be varied over a broad range. The manufactured specimens are analysed mechanically, optically and chemically by the in-house chemical laboratory. With a well equipped laboratory facility (Fig. 3)...
Kunststoffe international, 2005-11-21, Material Handling under Clean Room Conditions
...ting chamber. Through the repeated colliding with the outer surfaces of the baffle cones or the parallel inner surfaces of the housing, the dust particles adhering to the pellets are released. Subsequently, because of their low flotation velocity, they are carried upwards together with the other fractions by the rising air current and separated off again in a subsequent dust-collecting filter. The pellets, now purified of all fine fractions, leave the separator through the outlet at the bottom. ...
Kunststoffe international, 2005-11-21, Measurement by Ultrasound: Temperature Fluctuations in the Processing Unit
...ent by Ultrasound: Temperature Fluctuations in the Processing Unit The temperature profile inside the extruder is generally determined by means of temperature sensors that have a number of drawbacks. An ultrasonic measurement system supplies sound velocity data that makes it possible to calculate the mean melt temperature at defined points along the screw. This does not require any fittings that protrude into the melt flow. Ingo Alig, Dirk Lellinger, Kai Wassum A uniform melt quality is nec...
Kunststoffe international, 2005-11-21, Measurement Technology: Determining the Coefficients of Friction for Bulk Plastics
... solids conveying in single-screw extruders. A new friction measuring instrument based on the principle of a vertically oriented solids-conveying extruder permits measurement of the coefficients of friction as a function of pressure, temperature and velocity under nearly real-world processing conditions. Gernot Zitzenbacher Günter R. Langecker Rudolf Schatzer The conveying and plasticising behaviour of single-screw extruders is determined by friction interactions in the feed zone on the screw an...
Kunststoffe international, 2005-11-21, Metal Injection Moulding: Precision Parts Rapidly and Economically
...ign, the injection moulding parameters play an important role. The qualtiy of the moulded parts is determined primarily by the injection time, duration of holding pressure and cooling time as well as by the injection pressure and injection velocity. This means specifically: the processor must set the injection time such that mould filling is completed within 0.5 to 1s. A uniform injection velocity between 10 and 30cm³/s is recommended. If jetting cannot be avoided because of the mould geometry, ...
Kunststoffe international, 2005-11-21, Micro-Injection Moulding: Microfluidic Systems with Integrated Semiconductor Chips
...ty was produced by micro-milling. The semiconductor chip to be insert moulded is fixed by applying a vacuum and the finished part is ejected by compressed air. In preliminary tests, the optimum metering volume is determined at constant injection velocity, processing temperature and mould temperature (Fig.4). The metering volume computed theoretically with Pro Mechanica is 92mm3; the clamping force computed from this for the machine is 10kN. Because of the expansion of the polymer as a result of ...
Kunststoffe international, 2005-11-21, Mixing Efficiency: Calculating Mixing Sections for Reciprocating Screws
Injection Moulding Calculating Mixing Sections for Reciprocating Screws André Wieczorek Günter R. Langecker Christian Gornik Mixing Efficiency. Three-dimensional FEA calculations make it possible to analyse flow processes in mixing sections and assess the mixing effect on the basis of trajectory calculations. Three mixing sections are systematically compared with each other in respect of the definition, execution and assessment of these calculations. During the metering process, the plastici...
Kunststoffe international, 2005-11-21, Mixing Technology for Hot Runner Systems: Improved Melt Homogeneity
... are deformed part of the strain energy is converted into heat and cannot be recovered. This is the case for polymer flow where shear deformation induces shear heating at the runner wall. Melt Channel Sizing in Hot Runner Moulds According to the velocity profile of polymer flow in hot runners (Fig.1) the residence time at the melt channel wall is theoretically very long. This means that, depending on the polymer and the process parameter, cleaning the melt channel of the old colour during colo...
Kunststoffe international, 2005-11-21, Modular Systems for Hydraulic Drives: Tailor-made “off the Peg”
... the holding pressure immediately following. At high injection rates with correspondingly high injection pressures, such pressure overshooting can even damage the mould. SOC-PP (PP = pressure peak), together with SOC-V (V = velocity) brake the injection speed at just the right time to prevent pressure overshooting. The system thus offers effective mould protection even at very high injection rates. SOC-V and SOC-PP are “self-adaptive” controls: within three to five injection cycles, the software...
Kunststoffe international, 2005-11-21, Mould Technology: Blown Films with Improved Properties
...s. In a traditional head, the material stream is distributed to several small-diameter bores, each of which leads to a spiral channel. Although the material flow merges again in the outlet cross-section downstream of the spiral channels, the velocity is not uniform around the circumference, since the material flows at a faster rate at the outflows from the channels. A distribution of the flow rate then takes place at the outlet cross-section (Fig.2). Furthermore, the repeated separation and mer...
Kunststoffe international, 2005-11-21, No Crash Helmets Needed in Cars
... stiffer than EPP foam at 58 kg/m3) and maintains a constant deceleration level during controlled strand collapse. After complete compression, there is a further small increase in deceleration because the head shape has not yet been retarded to zero velocity, but the HIC value is lower than for the conventional foams. This requires comparatively smaller packaging space, and provides greater freedom of design. Compared with conventional materials, which only absorb impact energy by compression, t...
Kunststoffe international, 2005-11-21, One Hundred Per Cent Control of Material Webs
...ace area that has passed through (see also Fig. 3). The following relationship applies: ((Formula_1)) Where ε = efficiency, ρ = diameter of the effective measurement surface, b = material web width vmeasurement head = measurement head velocity vweb = web velocity In general, the efficiency is only about 1 %. Therefore, the measurement can only yield very limited information about the distribution of weight per unit area or thickness throughout the entire web. A novel detector radi...
Kunststoffe international, 2005-11-21, Online Process Control: Ultrasonic Measurements on Thermoset Moulding Compounds
...n Composite Industry) (AVK-TV), Frankfurt am Main/Germany, has worked on developing an online measurement method for direct monitoring of the processes in the mould. As a result, it was possible to develop the continuous recording of ultrasound velocity as an ideal method with great potential [1–5]. Ultrasonic velocity, as a control parameter, has the advantage that it correlates directly with the mechanical modulus – the storage modulus (real component of the modulus). In the dielectric methods...
Kunststoffe international, 2005-11-21, Optimisation of Screws with Small L/D Ratio: Custom-made Screws
... the throughput. In such cases the throughput rate is dominated by the melt. With injection moulding screws, the situation is different than for extruder screws because of the axial movement, which is superimposed on the screw rotation. However, the velocity component in the screw-channel direction is comparable for the two kinds of screw. The formula for Newtonian material behaviour, known from extrusion, can be used for estimating the volume throughput. The calculated volume flow rate can b...
Kunststoffe international, 2005-11-21, Pipe Extrusion: The Calculation of Spiral Mandrel Dies
...the circumference of the die is evaluated with the aid of the reduced volume flow. When determining the reduced volume flow, we initially assume a simplified impulse equation in cylindrical coordinates [3]. With suitable boundary conditions, the velocity profile at the die exit can be calculated. The boundary conditions correspond in each case to three adjacent points on the velocity curve (Fig.3). By integrating the velocity profile over the gap height, we get, for the reduced volume throughput...
Kunststoffe international, 2005-11-21, Pipe Extrusion: Universal Lattice Basket Die
...ticularly favourable manner for processing a very wide range of plastic materials, it also proved possible, for the first time, to visualise the flow components and their intensity in the axial and radial direction. Figure 2 shows the resultant flow velocity, starting at the inflow and proceeding through to the annular distributor. It is clear that a uniform flow has formed around the circumference in the Z direction a long way before the inflow into the lattice basket. Yet it is precisely this ...
Kunststoffe international, 2005-11-21, Plant Tuning: Increase in Capacity of Existing Polyester Plants
... the present pumps (product fitting dimensions and fitting height). Table 1 shows the most relevant dimensions of available pump types in comparison. When calculating pressure drop, we assume Newtonian fluids as a simplified approach. The low velocity of flow results in laminar flow (Re
Kunststoffe international, 2005-11-21, Plastic Bodies
...rties. For example, the impact strength is severely reduced after offline, and particularly online, painting. The hardness of the clear coat affects the fracture and impact strength by introducing cracks into the substrate. Fig. 3 shows the pendulum velocity necessary to fracture the same part made of the same material but with different paint systems. Both alternatives, online and offline painting, have high requirements which can probably only be solved with a uniform material concept for the ...
Kunststoffe international, 2005-11-21, Plastic Extrusion Dies
...e walls of the flow channel. The laser-optical measurements confirm and quantify the differences which could only be qualitatively obtained by pressure measurements. Fig.3 shows a normalised view at measurement point z = 30mm. The measured velocity values vz are plotted relative to the maximum velocity vmax in the channel centre (x = 0). In this way, the wall slip velocity components of the maximum velocity are easy to see. The x positions were taken relative to the widths B of the dies, which a...
Kunststoffe international, 2005-11-21, Plastic/Plastic Hybrids: It Doesn’t Always Have to be Steel
...orce of 1600kN. The hybrid brackets were tested in a standard climate in the three-point-bending and torsional tests and the force/displacement curves established. The bending test was performed with a support span of 340mm and a test velocity of 5mm/s on a Zwick universal testing machine. The torsion test was performed with a clamping length of 350mm and a rotational velocity of 1.5°/s on a test bench with a clamping and support device. Load-bearing Capacity similar to Steel The tests showed...
Kunststoffe international, 2005-11-21, Plasticising in Critical Areas
...xert a stress on the plasticising unit in that, with very fast running products such as packaging articles with very fast cycle times, load cycles of ≤1Hz can arise. Also of relevance here are the sliding speeds (circumferential velocity of the screw) in the plasticising system, where values of up to 1.5m/s are reached. For high-speed applications and high-performance plasticising systems, circumferential velocities of up to 2m/s can be expected in the future. Finally, mention should also be ...
Kunststoffe international, 2005-11-21, Polycarbonate instead of Glass: Large Car Windows from an Injection Moulding Machine
... flow paths of up to 1m. This is the reason why the PC glazing for the sunroof module is produced via injection compression moulding. Using this technique, the melt is injected into a partially open cavity, thus reducing the pressure and velocity gradients during the filling phase considerably (details regarding this are presented in the next section). Final distribution of the melt within the cavity and compensation for shrinkage of the melt through the closing motion of the mould take place wi...
Kunststoffe international, 2005-11-21, Polymer Characterisation by Means of Microwaves
...h the maximum possible bandwidths currently being 1 to 2 GHz. FMCW radar sensors already exist, which are based on a single chip only a few square millimetres in size [8]. The applications of microwave radar sensors used hitherto concentrate on the velocity and distance determination, e. g., for determining the content of storage tanks for liquids and bulk materials, or for increasing safety in the automotive engineering [7]. Depending on the application, various frequencies are used, and the di...
Kunststoffe international, 2005-11-21, Polymer Electronics: From Polymer Transistor to Printed Electronics
...urrent can flow from the source to the drain electrode. The strength of the current depends on the gate voltage, which governs the number of charge carriers, and on the charge carrier mobility µ, which is a measure of the charge carrier velocity. Physically, the maximum switching frequency of an organic transistor is described by the equation f~µxUds/L2. In other words, the shorter the channel length L and the higher the charge carrier mobility µ, the faster the transistors switch, whereby the c...
Kunststoffe international, 2005-11-21, Process Optimisation: Running Smoothly
... flow anomaly, the “wall slippage” effect, occurs at a shear stress of about 12000 Pa. In this case, the melt has lost its adhesion to the wall; it no longer has a wetting effect. The moulding compound slides along the wall at a particular velocity. The term “ideal wall slippage” is used to indicate a sort of “block flow”, though in reality (Fig.2), shear flow is superimposed on the wall slippage [2]. At melt temperatures of 200 and 210°C, slip-stick effects were also found to occur after the w...
Kunststoffe international, 2005-11-21, Process Technology: Polyurethane Processing Systems
...ve utilises a coaxial sleeve to throttle the flow (Fig. 10). The adjustable sleeve creates an annular channel that is variable in height. The chamfer at the lower end of the sleeve provides for gentler redirection of the flow and a reduced velocity of the reaction mixture as it is dispensed. Mixhead for long fibres. While the RRIM process can accommodate maximum fibre lengths of 0.1 to 0.2mm, various manufacturers have developed techniques that permit processing of long fibres of up to 100mm i...
Kunststoffe international, 2005-11-21, Process Variant for Thin-wall Injection Moulding: Injection Moulding with Precompression
...ding machine: over the short term, the hydraulic version is able to deliver many times its installed load, but an electric drive is unable to store power and therefore has to be designed with its maximum load in mind). With increasing injection velocity and rising pressures, the compressibility of the melt becomes more important. This effect and the elastic elongation of the injection unit mean that the flow front velocity decreases in comparison with the screw speed (Fig.2) [1]. In accordance w...
Kunststoffe international, 2005-11-21, Product Developments: Polyamides in the Engine Compartment
... Particular attention was focused on the impact strength of the polyamide, since the oil sump is directly exposed to flying stones. In tests, iron spheres weighing both 52g and 4kg were “fired at” the oil sump at a velocity of 270 and 50km/h respectively, without the sump fracturing. This result confirms the simulations that were conducted beforehand for working out the design of the part. The oil sump also fares very well in terms of structural rigidity. It does not suffer any damage if the com...
Kunststoffe international, 2005-11-21, PVC Processing: The Historical Development of the Counter-rotating Twin-screw Extruder
...bine two pairs of screws in one barrel. One twin-screw assembly is replaced by the central screw (of 220mm diameter) with which, from opposing sides, a small screw engages (of 110mm diameter) (Fig. 14). The same peripheral velocity is obtained by halving the screw speed of the central screw relative to the side screws. The more favourable ratio of surface area to throughput obtained with smaller screw diameters enables a great deal of heat energy to be input from outside. Heat is also introduced...
Kunststoffe international, 2005-11-21, Quality Assurance for Class A
...sure sensor pV logs the vacuum curve because vacuum technology is used with Class-A components. With the aid of four inductive stroke transducers S1 to S4, mounted in the corners of the mould, the closing movement of the press is documented and the velocity profile derived from this. These stroke sensors permit parallelism during mould closure to be checked and can be used to optimise the mould mounting position among other things. During the start-up and proving phase in particular, exact deter...
Kunststoffe international, 2005-11-21, Quality Assurance: New Scope for Process Control in Ultrasonic Weldin
...ding, there are definitely advantages to be derived from the use of the digital power supply, given the possibility of extended process monitoring. Aside from controlling the process via the joining velocity, the servo press enables the welding force to be applied faster and more directly through shorter control times. A possible advantage for the future could lie in the faster application of the welding force in a “novel” quality criterion for ultrasonic welding: For many other welding process...
Kunststoffe international, 2005-11-21, Quality Assurance: Residence-time Measurements and Detection of Melt Heterogeneities
... transillumination methods [2] are described in the literature, these are restricted to transparent materials. Ultrasonic techniques have been used for some time to perform in-line monitoring of extrusion [3, 4, 5]. It has been shown that ultrasonic velocity and attenuation can be linked to the viscoelastic properties, the melt viscosity, the filler content, the blend composition and the copolymer content. It seems obvious, then, that ultrasonic measurements might also be suitable for revealing ...
Kunststoffe international, 2005-11-21, Quality Testing: Criteria for Optical Sheet Inspection
...ket extends from transparent and non-transparent sheets to wafer-thin stretched films, and is therefore much broader than in, for example, the steel or paper industry. The variety of grades can be illustrated by means of some key data: - velocity 1m/min to 500m/min, - material thickness: 5mm to 20mm, - light transmission: highly transparent, via coloured to opaque, - web widths: 10mm to 8000mm. Web inspection systems must be able to handle this product range. Not only The success of a system is ...
Kunststoffe international, 2005-11-21, Runner Design for High-Quality Surfaces
...ult can also be obtained by means of a special runner design. A pre-manifold of tailored diameter and length has the function of splitting the melt flow shortly before it enters the cavity, so that the central melt flow enters the cavity at reduced velocity (Fig. 5). The advantage for a reduction of injection velocity by process-engineering measures lies in the fact that it is specific to a particular mould. Since, in practice, moulds are very often exchanged between machines, and the new parame...
Kunststoffe international, 2005-11-21, Shear Punching of Thermoplastic Film
... and cooling in actual production. - Final punching: In the last stage, the stop travels back hydraulically and the punching cylinder cuts through the film completely. Maximum Force as a Measure of the Machine Load Measurement of the distance and velocity was carried out via an inductive displacement transducer between the upper and lower platen. The forces were recorded with a force transducer. The amplified, digitised signal was saved on a PC and further processed. In the typical measuring c...
Kunststoffe international, 2005-11-21, Short-Term Shrinkage in Multi-Component Injection Moulding
...ocess parameters on the shrinkage behaviour of polypropylene (grade: Novolen 1100N, manufacturer: BASF AG) Schwindung = Shrinkage, Werkzeugtemperatur = Mould temperature, Schwindungsanteil = Shrinkage component, Einspritzgeschwindigkeit = Injection velocity, Kühlzeit = Cooling time, Nachdruck = Holding pressure, Nachdruckzeit = Holding pressure time, Massetemperatur = Melt temperature, Schwindung nach = Shrinkage after, radiale Schwindungen = Radial shrinkage, tangentiale Schwindungen = Tangenti...
Kunststoffe international, 2005-11-21, Shortened Product Cycles: The Changing Face of Extrusion Technology
...e still not considered state-of-the-art in single-screw extrusion, while high-speed machines have now become firmly established in twin-screw extrusion. High-speed machines is the designation used for extruders whose screws achieve a circumferential velocity of more than 1m/s. Although this limit was set in 1979, it can still be regarded as valid today [3]. The possibility of using high-speed machines was examined at the start of the 1960s already. When the results of the studies were analysed, ...
Kunststoffe international, 2005-11-21, Simulation and Practice
...onal heat during cavity filling, and the viscosity of the melt is reduced. If these low-viscosity melt regions flow to the outer region of the part, irregular advance of the flow front can occur. Fig.3 shows the qualitative relationship between the velocity, shear rate, temperature and viscosity profile across half the part cross-section. Multilayer Flow If two melts with different viscosities are caused to flow, the low-viscosity melt will attempt to flow in the vicinity of the mould wall to ...
Kunststoffe international, 2005-11-21, Simulation Model Confirmed
...mulations were made isothermally. To provide a precise description of the viscosity on shear rate within the widest possible shear-rate range, this relationship is described by means of the Carreau equation. The results are evaluated by means of the velocity profile at the die outlet, which is superimposed over the half die width in dimensionless form. In all simulations an improvement of volume flow distribution at the die outlet is found when a die land is used (Fig.1). It is clear that the do...
Kunststoffe international, 2005-11-21, Simulation of the Injection Moulding of EPDM
... behaviour of the compound, the viscosity increases only slowly again. To describe this phenomenon in the program, the local viscosity data can be transported in accordance with the melt flow. As a result of the simulation, the flow front, pressure, velocity and temperature can be analysed in the mould filling phase. The scorch index is calculated during the filling phase in order to identify any premature crosslinking. Material damage can be recognised by an excessive shear rate. By entering an...
Kunststoffe international, 2005-11-21, Simulation: Describing Processing Operations with Models
...introduction of digital computers. It forms the basis of most programs for static and dynamic structure calculations as well as for flow calculations. This method involves the area being divided up into elements, and parameters such as pressure, velocity and temperature being described by means of approximation calculations in the element. Figure 1b shows a two-dimensional area that has been divided up into triangular elements. In plastics processing, the most widespread simulation based on fini...
Kunststoffe international, 2005-11-21, Simulation: Even Faster Development of Cylinder Head Covers
...ling test arrangement for cylinder head covers Noise measurement Fig. 9A. Structure-borne noise measurement of a thermoplastic cylinder head cover Fig. 9B. The characteristic tested is the structure-borne noise velocity on the component surface Manufacturer TiK-Technologie in Kunststoff GmbH Engesserstr. 4a D-79108 Freiburg Germany Phone +49 (0) 7 61/50 31 25-62 Fax +49 (0) 7 61/50 31 25-68 www.tik-center.com
Kunststoffe international, 2005-11-21, Size Reduction of Thermoplastics by Cutting
...ius was chosen as r = 0.01 mm, corresponding to a newly sharpened knife after the first run. The knife clearance was set at 0.3 mm. The ambient temperature was 20 ± 2°C. The feed stock was cut parallel to the extrusion direction with a cutting velocity of 0.2 mm/s. In the investigations, the cutting force (acting in the cutting direction) FS, and the passive force FK perpendicular to the cutting force are recorded as a function of the cutting displacement. The Cutting Operation for the Basi...
Kunststoffe international, 2005-11-21, Software: The Optimum Screw Diameter at the Click of a Mouse
Injection Moulding The Optimum Screw Diameter at the Click of a Mouse Software. Selecting the right screw diameter is guaranteed to give high-quality parts. All the new ScrewSelection software requires to do this is a few items of basic data and a few clicks of the mouse. August Burr Andreas Müller Martin Hetschel The residence time of the moulding compound and the metering path are the key criteria when it comes to selecting the correct screw diameter and hence determining the quality level...
Kunststoffe international, 2005-11-21, Spiral Mandrel Dies: Uniform Melt Flow from the Spiral Mandrel
... through a large angle in the tangential direction. After first flowing through a manifold land, it flows axially through the die virtually in an axial direction. If a particle reaches a maximum predetermined lifetime during the simulation, or its velocity falls below a lower limit, the computation of its flow line is terminated. A premature termination of flow lines may therefore occur during the simulation (Fig.4, left). This is thus a termination of the simulation before the flow line under c...
Kunststoffe international, 2005-11-21, Surface Technology: In-Line Plasma Processes
Surface Finishing In-Line Plasma Processes Surface Technology. The Openair plasma process has, for some years now, been creating a variety of new applications, especially for the cleaning, activation and coating of moulded parts and film. Now, a modular system has been developed for the in-line pretreatment of PP film that works with flexible widths and allows a high level of activation. Christian Buske Alexander Knospe Plasma – the "fourth state of matter" – describes a materia...
Kunststoffe international, 2005-11-21, The Intensive Plasticator: An Inexpensive Concept for Melting Thermoplastics
...nveyed in the screw flights [2]. This is promoted by the fact that the channel depths in the cylinder and screw vary in complementary manners. Because of the different conveying rates of the solid transported in the spiral groove and screw flight, a velocity gradient occurs in the gap, which permits the work of friction to be converted into heat and thereby permit plastication of the material being processed. This fact is shown schematically in Fig.3. The machine concept originally used for the ...
Kunststoffe international, 2005-11-21, The Right Speed
... material. During the tests, it was found that the cutting speed had a considerable influence on the shape of the cutting force-deformation curve. Fig.3 shows the curves plotted for speeds between 0.0002m/s (quasi-static cut) and 4m/s. In the velocity range between 0.0002 and 0.02m/s, it can be seen that the general shape of the curve is retained and that the total deformation up until the material is cut right through remains constant, but that the level of force rises in the first third of the...
Kunststoffe international, 2005-11-21, The Tip Decides
... the screw tip with the result that the melt can flow into the screw antechamber. The screw tip moves at the speed of the screw while the sealing ring is either stationary on account of friction at the cylinder wall, or rotates at a lower peripheral velocity. Worn Flights Cause Fluctuations in Processes The relative motions of the screw tip and the sealing ring cause increased wear of the flights. This leads to stroke enlargement, which manifests itself in fluctuations in melt cushion. Wear at...
Kunststoffe international, 2005-11-21, Thermoforming by Radiation Crosslinking
...r of 255 mm and heated by means of a quartz lamp heater under constant conditions to equal thermoforming temperature (Fig. 2 left). Immediately afterwards, the film was stretched with a height-adjustable stamp mounted on the desk (D = 200 mm) at a velocity of 160 mm/s. The stretch ratio could be adjusted steplessly between 5.1 and 8.7. The degree of stretching is the quotient of the surface area of the thermoformed article and the non-formed circular area between the stamp and the frame. To avoi...
Kunststoffe international, 2005-11-21, Thoroughly Mixed?
... (Fig. 3). Good homogenisation requires both dispersion and distribution [2]. Ideally, dispersion should occur before distribution. In the metering zone of a three-zone screw, the melt is only agitated and is not intimately mixed. Figure 2 shows the velocity distribution in the channel direction of the metering zone for a specific mass flow rate and a certain back pressure. This velocity distribution causes shear stress to act on and disperse the melt particles. However, distributive mixing is f...
Kunststoffe international, 2005-11-21, Three Weeks Until the Start
...enthusiasts at the start of June 1999. The goal was to enter a Swiss team into the World Solar Cycle Challenge in Australia on a specially constructed racing vehicle. Responsibility for technical project development lay in the hands of the companies Velocity Engineering AG (E-bike producer), Proform AG, Marly/Switzerland, (rapid prototyping) and Creaholic SA, Biel/Switzerland, (project management). The companies had just four months to assemble a racing team. The project team sketched out variou...
Kunststoffe international, 2005-11-21, Transparency in Injection Moulding
...ßem Auge sichtbar = Visible with naked eye; Partikel = Particle Fig. 11. Triangular rear window in the Smart Explanation of important optical quality characteristics - Birefringence Light transmission in all directions at the same velocity -> optically isotropic Light transmission dependent on the direction of dispersion -> optically anisotropic - Refractive index Indicates, through its ratio to the velocity of the light, the extent to which a ray of light, which impacts at a given angle, is d...
Kunststoffe international, 2005-11-21, Ultrasonic Measurement Technology: Online Process Control
... Fig.1 shows a diagram of the measurement signal generation. The ultrasonic pulse transmitted through the material and detected by the receiver conveys two different items of information. From the run-time, it is possible to compute the velocity of the ultrasound and the relative amplitude gives a measure of the attenuation of the laminate between the two test heads. The two signal routings change during the progress of injection and curing, and log the individual RTM process steps. While the ch...
Kunststoffe international, 2005-11-21, Ultrasonic Production Control
...path, whereas any reflections occurring arrive at a later time (Fig. 2). This considerably facilitates the automatic identification of the moulding compound pulse. Automatic Signal Analysis The aim of automatic signal analysis is to compute the velocity of sound in the moulding compound as a function of the process time. The signal propagation time in the moulding compound is therefore first determined. The propagation time of the moulding compound pulse (Fig. 2, top), is composed of the propa...
Kunststoffe international, 2005-11-21, Viscosity Measurement: Determining Rheological Data Directly at the Machine
...shear-rate profile. The measurement nozzle can also determine flow anomalies in highly filled plastic compounds. Christian Gornik Viscosity is defined as the ratio between the shear stress and shear rate. When a flat plate is drawn over a liquid, a velocity profile is set up in the liquid. Furthermore, a force is required to move the plate, which is greater the higher are the values of the viscosity and velocity gradient, the so-called shear rate. Whereas water has a viscosity of 1mPas, the vis...
Kunststoffe international, 2005-11-21, Wood extrusion: Wood from the Extruder
...= wood terrace; Dachschindeln = shingled roof cladding; Paletten = pallets; Andere = others Fig. 4. Extruded profile, photo: Fasalex GmbH, Kopfing/Austria Fig. 5. Door frame, twin-orifice extrusion (PP 15%, wood fibre 85%), line velocity: 2x 2.5m/min, photo: ProPolyTec GmbH, Lichtenfels Fig. 6. Wood for coextrusion, photo: Technoplast Kunststofftechnik GmbH, Micheldorf/ Austria Table 1. Raw materials: Chief characteristics of some varieties [6] Table 2. Comparison: Mechanical properties of...
Kunststoffe international, 2005-11-30, Extrusion Dies: Variety by the Meter
Special Variety by the Meter Stefan Seibel Extrusion Dies. Production of high-quality semi-finished plastic goods requires product-specific extrusion lines that incorporate a number of critical processing operations. Regardless of where the extrusion die is located in this sequence of important components, there is no doubt that it is ultimately responsible for the shape of the product. It is this responsibility that results in the variety of products that can be produced via extrusion. Within...
Kunststoffe international, 2005-12-07, Case Study (6): Hot-Runner Solution for a Light Guiding Optical Part
... unit. A Process with Many Hurdles At the beginning of the project, a prototype mould was built in which the parts are gated via a conventional sprue with tunnel gate. The poor filling characteristics makes it necessary to use a large injection velocity to fill the cavities; this process control caused high shear rates in the gate and considerable material damage. Venting of air from the cavity, which is necessary to prevent diesel effects, posed an additional problem under these conditions. Th...
Kunststoffe international, 2005-12-08, A Status Report (1): Versatility for Mass Production in MuCell Injection Moulding
...so-called SCF unit; SCF = super-critical fluid), - process-specific software for controlling the processes in the injection unit, and - an accumulator (optional) for rapid injection with an adaptive, self-optimising control of the injection velocity. Effects on the Mechanical Properties The morphology of the microfoam – and therefore the mechanical properties of the part – are influenced by process parameters such as injection velocity, the type and concentration of the blowing gas (N2, CO2), t...
Kunststoffe international, 2006-01-15, Preliminary Exhibition Report: Winter in Milan
...ning rotor, and the unit is fitted with a monitor for quality control. The company will also present its gravimetric metering system, CWS 2023 (Fig. 4), which offers real-time recording of the material weight in the hopper and of the linear velocity of the extruded product. By controlling the extruder on the basis of these data, the machine operator can considerably improve take-off speed and thus the reproducibility of the products. Dipiemme S.r.l., Cassano Magnago, will showcase its latest uni...
Kunststoffe international, 2006-01-25, Die Design: Simulation of Extrusion Dies
...s of semi-finished and finished products. The dimensions of the extrudate are the most important quality factor and are dependent to a large extent on the melt distribution in the die. One of the aims of extrusion die design is to achieve a uniform velocity and temperature profile at the die exit. The focus here is on slit or flat film die manifolds, for which various design processes exist. In the analytical method, the die geometry can be calculated for slit dies and mandrels for given materia...
Kunststoffe international, 2006-01-26, Injection Moulding: Tailor-made for Cleanroom Production
...ighly accurate recovery and the performance of the injection unit. The shaft for the injection unit is driven by a servomotor with a high sensing rate and, in conjunction with a double gear rack, achieves highly accurate control of the injection velocity and transfer from position control to pressure control. This makes it possible to transfer to holding pressure at a high velocity and within a short deceleration stroke. The metering (screw rotate) shaft is also driven by a servomotor with a hig...
Kunststoffe international, 2006-03-23, PET Beverage Bottles: External Bottle Coating in a Stretch Blow Module
...n in the volume close to the surface - diffusion through the plastic and - desorption at the opposite surface. These stages, set out in Fig. 2, correspond to the solution diffusion model. Here, the permeation rate depends not only on the diffusion velocity but also on the solubility of the permeant in the plastic [3]. Although it is possible to compare an uncoated bottle with a coated one on the basis of absolute figures, this is a highly complex procedure. For this reason, use is generally made...
Kunststoffe international, 2006-04-25, Filler Dispersion: Ultrasonic Spectroscopy for In-Line Monitoring
...ansformation from the time domain to the frequency domain (Fig.4). The phase spectra of the transmitted signal φ0( ω) and received signal φ(ω) and the sample thickness s can then be used to determine the frequency-dependent phase velocity c(ω). Since the amplitude spectrum of the acoustic signal A0( ω) entering the sample is not usually known, the ultrasonic attenuation spectrum α(ω) is computed from the amplitude spectrum of the sample AP(ω), a ...
Kunststoffe international, 2006-04-25, Marking: Coding at Full Speed
...sed. “The time, date, article number, company name and number of the shift in which the profile was produced serve primarily for tracing production within the factory," says Hofmair. Reliable Coding A dedicated control system optimises the velocity and viscosity of the ink jet within the printing head. An integrated temperature control system checks the viscosity of the ink to provide a uniform print quality, and increases the reliability of the Linx 6800 when it operates at the limits of t...
Kunststoffe international, 2006-07-04, Company History (3): The Road to Global Player
...or and position sensors provide the prerequisites for new ideas in the area of control technology. Closed-loop control of injection ensures sensitive, but at the same time dynamic, control of the process parameters pressure, position and velocity (injection rate). Improved reproducibility in this regard assures the processor better product quality. In 1983 the modular concept for injection moulding machines is pushed further with the Allrounder CMD models. The operator now controls machine seque...
Kunststoffe international, 2006-09-26, Material Handling: Basis of Product Quality
...) and polyethylene (PE), in particular, heat up very easily and this may result in “angel hair”. However, reliable and cheap mechanical solutions are at hand today to counter-act these problems. These instruments can restrict the conveyor air velocity to 25m/s, using neither electricity nor compressed air [1–3]. Dedusting. More and more processors are considering dedusting before metering and drying indispensable (Fig. 1). In particular, when it comes to the injection moulding of highly transpa...
Kunststoffe international, 2006-09-26, Twin-screw Compounders: Is Faster Better?
...om 6.7 Nm/cm3 to 11,6 Nm/cm3, making it possible to process material with a higher degree of loading. The increased output from these machines, however, affects the quality of the polymer. As a consequence of increasing the screw rpm, the peripheral velocity also changes: if, for an otherwise identical process, a screw speed n0 of 1000 min-1 is chosen instead of 500 min-1, the peripheral velocity v also doubles: where D = screw diameter. This, in turn, results in an increase in the shear rates ...
Kunststoffe international, 2006-11-24, Direct Addition: Calcium Carbonate – Joker When Extruding PVC
...ur during pneumatic conveying of the dry blend from the mixer to the intermediate storage silo because of the density differences between PVC (1.4g/cm3) and calcium carbonate (2.7 /cm3) must be viewed more critically. Depending on the air velocity, the vertical elevation to be overcome and the length of the conveying distance, the unbound calcium carbonate can separate during conveying. This leads to unstable extrusion behaviour, varying mechanical properties and possibly even to visible defects...
Kunststoffe international, 2006-11-24, Filler Systems: How Conductive Compounds Work
Compounds. How Conductive Compounds Work. Stefan Apelt et al. Filler Systems. The fillers in a plastic compound give rise to different conductivities depending on their type and structure. In the case of polyamide, in particular, this conductivity is also affected by the moisture content. Special investigations consider the phenomena of electrical conductivity and look into the possibility of using the corresponding polyamide 66 compounds for bipolar plates in a fuel cell. Conductive plastics ...
Kunststoffe international, 2007-01-22, Complex Moulds for Foam
...d direction 1. On the ejector plate, shafts are fixed, which move the lifters (blue) in direction 2. The shafts are fixed on the ejector plate via slides, which permit relative movement. A wedge below the slides can be used to influence the velocity in direction 2. The angle of the wedge points in direction 3, the relative velocity between the ejector plate and the shaft/lifter. The same direction thus occurs for the relative movement between the part to be ejected and the lifter, since the part...
Kunststoffe international, 2007-01-22, Third Generation Unveiled
...ans of servomotors with satellite roller screw and transmitted to the tables via double toggles. To prevent transverse forces on the column guides of the forming tables, the force is transmitted centrally to the double toggle. The precisely designed velocity profile of the double toggle permits maximum force transmission during punching. The table travel distances and velocities are adjustable. Together with the separately driven top and bottom clamping frames, ten different forming programmes a...
Kunststoffe international, 2007-02-13, Process for Quality Moulds
...of smooth cooperation between companies and their partners in global innovation networks. Its portfolio includes NX (digital product development), Team Centre (digital lifecycle management), Tecnomatix (digital manufacturing) and Velocity (PLM for SMEs). Particularly for tool makers and mould makers, UGS offers wizards that automate and significantly shorten the process of development and production planning of injection moulding, progressives dies and pressing moulds. www.ugs.com
Kunststoffe international, 2007-03-15, Industrial Production of Optical Parts
...ess window. Finally, injection-compression moulding also yields a cost advantage for both the manufacturer and the customer for the products. Moreover, the additional parameters of this process, such as the compression gap, compression velocity, compression pressure, and the associated times and delays, offer further possibilities for increasing production quality. An example of this is the compression pressure: Since the holding pressure is not transmitted centrally via the sprue, but over the ...
Kunststoffe international, 2007-08-14, Mathematical Optimization of Annular Non-Return Valves
... the layout of the non-return valve geometry on the basis of empirical knowledge. Once the calculation has been completed, the results graph outputs the following (Fig. 5) - the development in the throughput over the metering path, - the rotational velocity of the locking ring over the coefficient of friction between the locking ring and the blades of the locking device tip and - the position of the screw and locking ring over time. For the metering phase, the outputs also include the numerical ...
Kunststoffe international, 2007-09-19, A Design Tailored to Requirements
...taining a dry-running time of only slightly above 1 s and with an opening width of 150 mm. The injection unit on the E-Max is similarly driven via a spindle with a toothed belt and, for design reasons, has a low inertia. The maximum injection velocity is 450 mm/s, with high pressures at the same time. To give an example: the 200 injection unit with a screw diameter of 30 mm attains the maximum injection velocity of 330 mm/s up to the maximum pressure of 2,000 bar. Water-cooled frequency converte...
Kunststoffe international, 2007-09-19, It’s the Pressure that Keeps the Balance
...ancing (Fig.3). In a first step, different parameters for the balancing are sought (Table1). Starting from the central point in the steady-state condition, multiple parameters are systematically varied. It is found that the injection velocity has a large influence on the hot-runner balancing. Its increase leads to a faster rise in the cavity pressure. This reduces the time difference between the cavity pressure curves of the individual cavities. In the steady-state process with 17cm3/s, the inje...
Kunststoffe international, 2007-09-19, Technology Barometer Indicates Fair Weather
...expensive compressor that is otherwise used can be dispensed with, and a simple double-acting cylinder that supplies the necessary amount of pressurized water per cycle can be employed (Fig. 6). The motion of the piston and thus the flow velocity of the water can be regulated exactly just like the injection velocity. The project exhibited at the K 2007 is based on a tiebarless multi-shot injection molding machine with two injection units for coinjection of two plastic melts and a third, piston i...
Kunststoffe international, 2007-10-21, Film Production with an Open Bubble
...ystem, nozzles blow the air tangentially against the film. The hot air is extracted from the bubble higher up. The air blown tangentially against the film cools the bubble at the most effective point. The tangential air flow allows the relative velocity difference between the bubble and the cooling air to be increased, which considerably increased the heat transfer coefficient. Air as Production Factor The increase in web speed is limited by several factors. One is the cooling intensity. Recen...
Kunststoffe international, 2007-11-21, Capillary Rheometry Optimizes Injection Molding
...e capillary rheometer (Fig.3a), like the instrument for determining the melt flow rate, consists of a reservoir cylinder and a measurement nozzle (capillary). However, in a capillary rheometer, the polymer melt is forced through the capillary by a velocity-controlled piston (Fig.3b). Therefore, for a measurement, it can be assumed that the volume flow rate through the capillary nozzle is constant. The pressure loss in the capillary is measured by a pressure sensor. The inlet pressure losses caus...
Kunststoffe international, 2007-11-21, Outer Body Skin with an Integrated Antenna
...ctric and hence radiation-permeable behavior towards electromagnetic waves, the additives and bonding layers in the multilayer polymer structure can have a key influence on the material-specific relative permittivity – as a measure of the phase velocity of the waves – and also on the dissipation factor. Building up complex multilayer plastics systems on the basis of film requires the holistic optimization of the production processes that all interact – starting with the material selection and go...
Kunststoffe international, 2007-11-21, Water Injection via an Additional Injection Unit
Water Injection via an Additional Injection Unit Molded Parts with a Hollow Core Water injection technology in injection molding allows the manufacture of molded parts with hollow cross-sections and is used in particular when such parts cannot be produced by blow molding or conventional injection molding techniques, i.e. using cores or slides. For the first time a new process integrates the water injection entirely within the injection molding machine via an additional injection unit. Flori...
Kunststoffe international, 2007-12-17, Many Improved Details
...ing and injection motions (Fig. 10). In this design, the linear motor is coupled to the toggle mechanism of the clamping unit as well as to the injection piston and can operate the two axes alternately. The maximum injection velocity achieved is 2.5m/s. Economical Production Although the K show did not offer any truly new developments this year, there were many improved details. The solutions presented often provide enhanced benefits for the user, e.g. the ability to mount larger molds or long...
Kunststoffe international, 2007-12-17, Marriage between Specialists
...d off by the movement of the mold insert, i.e. the edge at the stationary mold half is of moderate quality. The holding pressure necessary to compensate for the cooling shrinkage is built up, in a similar way to solid bar extrusion, by means of the velocity of the core insert and the volume melt flow generated by the injection stroke of the screw. If the insert moves slowly, a higher pressure builds up in front of the screw – a higher holding pressure therefore acts in the region of the flow fro...
Kunststoffe international, 2007-12-17, Meeting Application Demands with Accuracy
...n of high-pressure capillary rheometers (Fig.6). There are three versions available, i.e. with 25, 75 or 120kN piston forces, comprising a single, twin or triple barrel system. Having optimized the drive system, maximum piston velocity was doubled to 40mm/s, leading to double the range of speeds. Calibration of collected pressure data is 10 times as detailed, and the pressure sensors’ handling was significantly facilitated. While using the company’s brand of pressure sensors, no data must be ent...
Kunststoffe international, 2007-12-17, More Complexity, Speed and Intelligence
... the injection nozzle. At the K, the mold was in fact mounted on a fully electric injection molding machine, since the screw’s advance rate (melt stream generated) can be quite easily synchronized with the slide velocity of the mold insert. However, the developer says there would be no problem employing such a mold on machines with hydraulic drives. As long as we are talking about world novelties in injection molding and mold technology, we mustn’t forget PU flexible foam sealing material straig...
Kunststoffe international, 2007-12-17, Not off the Rack
... system features high precision (±1mm) and a lower noise level. A cutting system combined with a caterpillar take-off unit was presented by Rolf Schlicht GmbH of Hamburg, Germany (Fig.10). The conveyor system features very constant velocity and maximum take-off forces, the sectioning device features high precision in the 1/10mm range, short reaction times and clean cut faces. Graewe GmbH of Neuenburg, Germany, presented a fully automatic twin-windup unit. It has two separate high-speed binders t...
Kunststoffe international, 2008-01-15, Complete Solutions Sought
...of central generation of vacuum via the option of two vacuum pumps operating in parallel, decentralized vacuum distributors make it possible to divide the suction among different material loaders. This permits flexible matching of the conveying velocity to individual parameters such as the distance to be conveyed, volume to be conveyed and material to be conveyed. Control Networks As all exhibitors indicated, electronic recording and monitoring of material flow is becoming increasingly importa...
Kunststoffe international, 2008-02-17, Efficient Design of Pneumatic Conveying Systems
... not subject to the abrasion typical of pellets and anyhow generally have a following granulation step. In dilute-phase conveying systems the particles of solid material are moved individually through the conveying line. At about 20 to 30m/s the gas velocity is substantially greater than the settling velocity of an individual particle of bulk material. Depending on the solids-to-air ratio μ the particles are accelerated to 60 to 90% of the gas velocity, collide many times with the pipe wall w...
Kunststoffe international, 2008-02-29, Noise under the Hood
...also to be used later on for assessing the calculations performed with viscoelastic material data on the basis of the DMA measured values established. The spectrum set out in Figure 6 shows the influence of the stiffness on the mean surface velocity of the cylinder-head cover. The basic value (5,742 MPa) corresponds to a reduced static Young’s modulus for the PA66-GF35 with conditioning in a standard climate. Since a clearly lower degree of fiber orientation generally prevails in real-life parts...
Kunststoffe international, 2008-04-14, Controlling Discharge
...ce, when removing an adhesive tape, electrostatic charging is generated. The principle underlying is the same as in contact charging. The stronger the contact, the higher will be the amount of static electricity produced. Another aspect is the velocity applied while separating the two objects. If separation is slow, electrostatic charging is low, because there is time for many little static dischargings to take place. In case of quick separation, electrostatic charging is more pronounced, since ...
Kunststoffe international, 2008-04-14, Streets ahead of Injection Molding
...ts to move counter to the injection direction even before the melt has passed through the heated supply section that is about 100mm long and emerges into the open air. The injection process is primarily pressure-controlled, with the flow front velocity and the carriage movement being harmonized. This means that the gate follows the flow front. During the filling operation with frontal flow, a uniform pressure profile develops on the basis of the melt viscosity (Fig. 2). This state is a virtually...
Kunststoffe international, 2008-06-16, Bright Heads
...such a way that use of a 20 kHz ultrasonic welder handled the application without difficulty (Fig. 2). Also Suitable for Critical Applications This servo-pneumatic-controlled welding machine with process-optimized force profiling and integral velocity and force control is well-suited for moderate to large welding operations as well as textile die-cutting. To achieve maximum weld strength in the multi-phase structure of semi-crystalline polymers, welding presses in the Dynamic Series feature f...
Kunststoffe international, 2008-06-16, Calculating the Layout of Inserts
...profile of the simulated curve shows a linear increase in the deformation. Up to this point, the gate system in the cavity is being filled. The linear increase in the deformation corresponds to the expected profile, assuming a constant injection velocity for the melt. The measurement results only indicate deformation as of a degree of filling of around 65% – which then increases further up to the point of complete filling. The curve recorded with the aid of the strain gauge has a steeper gradien...
Kunststoffe international, 2008-06-16, Using Real-Time Control for Microprecision
...n of the stroke – this makes the process as a whole more controllable. To prevent premature solidification of the melt front during injection and ensure complete replication of the microcavities, micro-injection molding requires a high injection velocity. Irregularities during preplasticizing are reflected in the injection process. Even minimal fluctuations can lead to overfilling or underfilling of the microcavities. To address this problem, premetering – as employed in the Microsystem 50 (man...
Kunststoffe international, 2008-07-15, Intelligent Sprinters
...ormance achievable by both types reflects the interplay between kinematic system and drive technology. In hydraulic drives, maximum platen speed of up to 2 m/s is determined by the dimensioning of the hydraulic valves, by the maximum permissible oil velocity in the system lines (up to 30 m/s) and by system pressure (over 200 bar). In electro-mechanical drives, the top platen speed depends on the power provided by the motor and, above all, on the circumferential speed of the ball screw. That is w...
Kunststoffe international, 2008-08-14, Pearlescent Polymers
...maximum throughput. The Do/Di = diameter ratio determines the shearing, degassing and powder feed. The shear stress t acting to disperse the particles is the product of viscosity and shear rate ??? (t ???? [N/mm2]). The shear velocity itself is calculated from the circumferential velocity v of the screws at the housing wall divided by the maximum filling level in the screw flight (Fig. 4). For a constant viscosity, the following relationship can be educed: The deeper the screw fl...
Kunststoffe international, 2008-09-23, Wear Protection for Ring Non-Return Valves
...r on the flights of the screw tip. To generate a simple model of this, the check ring is conceptually unrolled in the plane and the draft angles of the screw tip are considered as wedges that move past the check ring with the average circumferential velocity vcirc (Fig. 4). Furthermore, simplifications are made on the model, so that an analytical solution of the equations can be found. An important assumption for the validity of the model is also that the wedge gap heights H0 and H1 are ...
Kunststoffe international, 2008-11-20, Water Combined with Air
...lar orifice and over the external surface of the bubble. Today, dual-orifice air rings for external cooling of the blown film are considered the state-of-the-art. In the air ring, the air exiting from the upper orifice is discharged at a higher mean velocity than the air from the lower orifice. At the same time, the Venturi effect assures that the bubble conforms to the shape of the air ring, causing the mean velocity of the air to increase and thereby improving heat transfer. Regardless of the ...
Kunststoffe international, 2009-02-17, A Method for Sound Component Design
... simulation chain. Consistent Simulation Chain The orientation of the reinforcing fibers is determined by the flow conditions that prevail during cavity filling. As a general rule, the reinforcing fibers are oriented along lines with an identical velocity. Shear flows cause the fibers to be oriented in the direction of flow, while extensional flows, by contrast, produce orientation perpendicular to the direction of flow on account of the transverse velocity component. A characteristic layer stru...
Kunststoffe international, 2009-06-16, Quality Problems during Mold Start-Up?
... even though the pressure peak on the electric machine, with its more rigid, direct drive cannot readily be imitated on the hydraulic machine. The other way round, this can be achieved considerably more easily through a lower injection velocity. If the parts are produced in the test using the production settings and the reproduced pressure curve in the screw antechamber, then it is possible to reduce the original weight difference by 67 % (Fig. 6). Conclusion: The investigations conducted on a t...
Kunststoffe international, 2009-07-16, Automatically Optimizing Profile Dies
...(reciprocal shear rate at the transition from Newtonian to non-Newtonian flow) and C (increase in the linear non-Newtonian range). ??? The implementation is checked on a simple geometry by comparing the state variables of pressure loss and velocity at the die outlet from XNS simulations with those from analytical computations. The outlet velocity distribution is an important characteristic, since it should be as uniform as possible to achieve good profile quality. The pressure loss in the die sh...
Kunststoffe international, 2009-10-14, A Fascinating Foray
...e was chosen, there are greater possibilities for controlling needle valves at positions intermediate between full open and full closed. This results in advantages for different cavities in families of molds, for velocity profiles with ''''gentle movement to the closed position to avoid pressure peaks and to prevent pressure breakdown due to temporary coverage of the melt streams during cascade filling. Where synchronous needle movements are sufficient, mold costs can be saved by means of a comm...
Kunststoffe international, 2009-11-19, Flow Control with Valves
...s must be met: Flow-optimized melt channels in the valve, maximum possible separate temperature control of melt channels, pressure-tight separation, clean purging of the channels in which the skin and core melts flow successively, and avoidance of velocity or pressure drops and pressure peaks. From these points results a harmonization of the two melt flow rates, which leads to an acceptable sandwich structure. The sensitivity of the temperature control in the sandwich valve must match the chosen...
Kunststoffe international, 2010-03-17, Practically Reliable Viscosities for Simulations
... injection mold in position, together with the measurement sensors. The measurement starts with the melt being injected into the heated mold. In semi-automatic operation, up to ten injection cycles are run with a constant setting for the injection velocity in each case. The sensors measure pressures and temperatures in the slit capillary, as well as the piston return speed. The data is recorded by a standard commercial data acquisition system. Measuring the Pressure Dependence of the Viscosity I...
Kunststoffe international, 2010-04-20, Hot and Cold Molds
...mediately on the end of the cooling time, and may continue for the duration of the mold movement, demolding and ultimately until the beginning of the next injection phase. A time of 7 s is initially plausible for a standard mold. Reaction Velocity in Practice As a practical test, a test mold was constructed, which has two flat cavities, each with an opening for a weld seam and different surface roughnesses (Fig. 4). Only the tests with one heating-cooling circuit and an aluminum heat sink are sh...
Kunststoffe international, 2010-04-20, Square Meters in CD Quality
...on line, these functional lines would be separated. Great attention was also paid to the conveying process itself, which takes place very gently. With dilute phase conveying according to the vacuum principle used here, the velocity must not exceed 20 m/s, since the pellets can plastify on the inside wall due to the high friction, and the molecular chains could be damaged, or “angel’s hair” could even occur. Conveying, too should be as far as possible dust free, since this can also have a negat...
Kunststoffe international, 2010-07-22, Thick-Walled Plastic Parts for LED Cycle Headlamps
...umption: 2.8 kWh. It makes full use of the advantages of the all-electric Elion series (Fig. 1, manufacturer: Netstal-Maschinen AG). The reproducible mold movements, precise metering and highly precise control responses of the injection velocity and holding pressure result in a high part quality and less than 1 % rejects. Manufacturing Poses Many Challenges The Elion takes full account of the ecological aspects that are becoming more important for processors, such as noise and emissions, and ene...
Kunststoffe international, 2010-08-19, WPC Has Different Filling Behavior
...tour, the flow front begins to advance further in the cavity (Figs. 1 and 2). Effect of Process Parameters and Wood Content In an example, the effect of the process parameters with a wood content of 45 wt.-% was investigated. With a higher injection velocity, there is a faster flowfront advance until the beginning of melt stagnation. In addition, the stagnation phase is shorter. With a higher barrel and melt temperature (and therefore with a lower melt viscosity), the melt stagnates at an earlie...
Kunststoffe international, 2010-09-24, An Industry on Tenterhooks
...r with an electrically adjustable control pump. Specially developed software for operating point optimization sets the best servomotor speed and swivel angle of the control pump to ensure maximum efficiency of the drive system for each velocity and pressure size. Engel is meeting the market’s high demand for closure cap production with an all-electric solution. The newly designed e-cap (Fig. 3) is equipped with an improved premium design of the injection unit, increased ejector force and a more ...
Kunststoffe international, 2010-09-24, As Far as My Soles Will Carry Me
...ective parameters are not yet taken into account by the mechanical test. The biomechanical investigating methods are used to analyze parameters such as impact loading, rate of pronation (inwards turning of the foot), and pronation velocity by means of measurements with the subjects. In subjective test procedures, runners evaluate the running shoe properties like fit, pressure points, and comfort. Therefore, only the combination of mechanical, biomechanical, and subjective measurement procedures ...
Kunststoffe international, 2010-09-24, Integrating Product Decoration into a Process Chain
...ry thin, heat-sensitive substrates. Due to the laminar flow behavior, the plasma spreads uniformly on the surface and penetrates even into very small cavities or fine gaps (Fig. 1). The nozzle can also be used for cleanroom applications. With a velocity of up to 600 m/min and a width of up to 40 mm per nozzle, the Plasma Brush System PB2 is designed for high productivity and efficiency during pretreatment. The plasma is generated by pulsed arc discharge and reaches 120–250°C under normal ambient...
Kunststoffe international, 2010-09-24, Melt Flow in a Circular Distributor
...st manufacture – the system also offers a series of process-engineering and operational-engineering advantages: Short flow paths and a low melt volume, leading to short residence times and rapid material and color changes, low wall-shear velocity, and hence low dissipation (temperature increase), low pressure losses, and hence a high throughput potential, high flexibility in terms of layer structure (thick layers/thin layers, materials/layer structures) and number of layers, thermal separation a...
Kunststoffe international, 2010-09-24, Plastics Processing – Rapid and Reliable
...tion behavior; “vibration control” reduces the natural vibration with long axle dimensions too, and “efficiency control” optimizes the productivity-to-energy-consumption ratio for the robot movement. The selfoptimizing acceleration and velocity values keep the waiting time prior to handling to a minimum, thus avoiding unnecessary loads on the mechanics and power train. Hall 15, booth B42 and C58 Wittmann Protection against Collisions With 70 exhibits from seven different product areas, Wittmann ...
Kunststoffe international, 2010-11-25, Temperature-Related Crash Simulation: Less Work Required
...f the development process. Elaborate Investigation Material data for crash simulations are mainly obtained from uniaxial tensile tests. Determining the characteristic data is very demanding due to several reasons: While impact speed and displacement velocity are high, it is necessary to apply very high take-off speeds. This calls for servo-hydraulic test equipment. If compared to spindle-driven universal test units, these machines have some downsides, though: The measured force signal is superim...
Kunststoffe international, 2011-01-25, Three Steps to a Good Marking Result
Marking a part using a laser as the marking tool is a technically demanding process. The user needs to know the pulse power, the pulse frequency, the beam deflection velocity and the energy settings that are required for the laser in order to refine and optimize the marking result. The wide range of setting options available for the individual parameters on the TruMark meant that, despite the comprehensive training offered by Trumpf, the manufacturers (see box on page 16), those new to laser mar...
Kunststoffe international, 2011-02-21, Better Filling of Polyamides
...th interchangeable inserts. Before processing, the pellet stock was pre-dried (dry air 8 h/80°C) and molded in the injection molding machine according to ISO 1874 with a melt temperature of 305°C, a mold temperature of 80°C and a flow-front velocity of 200 mm/s. The demolded test samples were hermetically packaged until testing. Compounding and injection molding were performed at the German Plastics Institute (Deutsches Kunststoff-Institut, DKI) in Darmstadt, Germany. The tests were carried out ...
Kunststoffe international, 2011-04-25, Multiaxial Textile Grids
... ILK. The grid reinforcement significantly increases both the energy absorption capacity and the impact resistance of the parts. The Temag reinforcement can effectively prevent part failure (Fig. 5). On impact of a 2 kg steel sphere with a velocity of 20 km/h, considerably less damage results in the Temag-reinforced door lining compared to a purely LFI-reinforced part. Summary and Outlook The development of Temag structures and their further processing into fiber composites form the basis for pr...
Kunststoffe international, 2011-05-12, Predictive Forming and Backmolding
...Fig. 3) has a diameter of 180 mm. The necessary sheet metal blanks are laser cut and inserted into the cavity. In the injection-compression trials carried out first, the compression force, mold temperature, melt temperature and compression velocity were varied. The flowpath-independent cavity pressure permits uniform forming of the discrete structures. In subsequent injection molding trials, the holding pressure level is varied in line with the compression force. The temperature effects are not ...
Kunststoffe international, 2011-06-20, Hitting the Nail on the Head
...the second sensor [2]. To do this it is necessary to detect the rise in the signal as close as possible to the moment at which the melt front reaches the two respective sensor positions. Since depending on the separation of the sensors and the velocity of the melt these can be very small time differentials in the millisecond range, the determination of the melt front via a switching threshold in the pressure and temperature signal is fundamentally unsuitable. Even with process control the melt f...
Kunststoffe international, 2011-06-20, Microsystems from Polymer Films
...d wire, which leads across a microchannel, is heated by a constant electric current. When a liquid flows through the channel, it cools the wire and so lowers its electrical resistance. The voltage across the wire is therefore a measure of the flow velocity. Not only simple wires, but also electronic components such as resistors and capacitors have already been embossed in polymer films by ultrasonic hot embossing. This opens up the possibility of integrating the electronics associated with a mec...
Kunststoffe international, 2012-04-20, Two Colors in One Die
...uating volume flow distribution at the die outlet can enable the prediction of ultimate thickness distribution of the PMMA coating on the window profile. The goal is uniform distribution across the entire profile width. Via the standardized exit velocity shown in Figure 5, volume flow can be calculated in relation to the cross-section of the particular outlet gap. In the example illustrated, version 4 (V4) represents a channel geometry with optimum distribution. Channel geometry and volume flow ...
Kunststoffe international, 2012-09-17, Humidity Regulation
...d capillaries are formed. In their centers the particles are located. The process is currently applied to produce pearlized films or microporous films with a high water vapor and oxygen transmission rate [4] or to increase the water vapor absorption velocity of films with dispersed humidity absorbers in it [5]. When salts are applied as humidity absorbers orientation brings the advantage that the particles are detached from the polymer matrix. Well stretchable polymers are polypropylene (PP), po...
Kunststoffe international, 2012-09-17, Turbo Technology for Injection and Ejection
...ptation of the ejector valve on the El-Exis SP combine greater positioning accuracy of the ejector with increased ejector acceleration. This allows the operator to individually design and precisely adjust the ejection process with flexible velocity control with rapid acceleration and braking processes within a large process window. The ejector operates highly dynamically (Fig. 6) and, for example in the production of screw caps, ensures a defined demolding movement and precise dropping of the pa...
Kunststoffe international, 2012-10-15, Flexibly into the Future
...G, Neutraubling, Germany. The Contiform 3 is Krones’s latest machine generation and offers thorough reworking of individual process steps (Fig. 3). An electromagnetic stretching system provides the prerequisite for flexibly adapting the stretching velocity to the machine’s current production output. The modifications permit continuous production output of up to 2,250 containers per hour and blow molding station. That corresponds to a productivity increase of about 10 % compared to the preceding ...
Kunststoffe international, 2012-11-26, Punching and Welding in a Single Cycle
...responsible for plastification during the welding process. Through graphical monitoring of the various welding parameters on the ultrasonic welding machine it was possible to define a processing window. In this respect a uniformly increasing joining velocity is important as this guarantees uniform melt flow and good weld strength. During ultrasonic welding five different operating modes are available: Time, Energy, Power, Distance Absolute (end point of the weld distance) and RPN distance (refer...
Kunststoffe international, 2013-02-22, Small Energy Director – Large Effect
...process. The machine controll displays the weld process as a graph. After analysis of the graph, the process is further optimized by defining tight process windows with minimum and maximum values. The curve of the joining velocity, in particular, is important; it is a unique “fingerprint” and should ideally have a constant linear gradient, because under normal circumstances a constant joining velocity guarantees a stable welding process with reproducible weld strength (Fig. 3). Biotechnology Dem...
Kunststoffe international, 2013-04-19, Injection Moldings for the Compost
... thin walled, according to Wittgrebe, the machine is set for high injection velocity and pressure. For venting the mold – a critical point in such applications – the range is equipped with the “Easyflow” function. Once the mold is closed, the full clamping force only builds up gradually in several stages on the start of injection – the air can escape via venting channels in the parting line. Peter Steinl is impressed by the all-ele...
Kunststoffe international, 2013-04-19, Melt Filtration on the Injection Molding Machine
...ontinuously, but just as cyclically as the injection unit. The extruded polymer melt is conveyed at a controlled pressure into a cylindrical melt accumulator. The injection plunger then utes a pressure and velocity-controlled forward movement, forcing the melt into the mold. The advantage of the system is that it allows large shot volumes of high melt quality to be processed with comparatively low clamping forces. With small and me...
Kunststoffe international, 2013-04-19, Playing with WPC
... in the wood to evaporate. The steam cannot escape in the closed cylinder and remains in the hot molding compound. During injection into the cavity, the plasticated material is forced at high velocity through a narrow gate, causing a further increase in the pressure and temperature in the molding compound. The injected strand can only expand when it enters the mold. Due to the ratio of the large volume of the counters to the ...
Kunststoffe international, 2013-06-19, Three Levers for Controlling Product Quality
...Zn2, a peripheral speed of 0.2 m/s and two different injection speeds Fig. 5. Comparison of the resulting recovery rate of dry blend (D) with pellets (G) for material CaZn1 and CaZn2 at a peripheral speed of 0.1 m/s and at 10 mm/s injection velocity Fig. 6. The use of dry blend (right) gave rise to a darker initial color compared with that of pellets (left) Fig. 7. The propensity to form silver streaks is greater in PVC-U dry blend processing (right) than in the case of pellets (left) THE AUTHOR...
Kunststoffe international, 2013-07-22, Measuring Melt Temperature with Ultrasound Metrology
... to negative temperature gradients in the space in front of the screw. Computer simulation here yields a more or less radially symmetrical temperature distribution. The higher melt temperature in the region of the barrel axis can be explained by the velocity field of the melt. The backward movement of the screw creates a suction effect which draws the melt from the front portion of the melt cushion to the screw tip. In Search of Non-invasive Methods Many studies have already looked at measuring ...
Kunststoffe international, 2013-07-22, Precision Injection-Compression Molding
...g of the injection phase by the compression gap. The melt is shaped in the cavity by the closing action of the mold during injection. The mold movement is usually subdivided into two phases during injection compression molding. In the first phase, a velocity-controlled movement takes place. As soon as a changeover criterion has been reached, for example a particular cavity pressure, the second phase begins, in which, e.g., the clamping force is controlled. The advantages of injection-compression...
Kunststoffe international, 2013-08-19, Controlled Closing, Highly Constant Shot Weight
...for transparent optical parts of PC and PMMA. The accurately reproducible closing operation of these non-return valves is influenced by a number of factors, such as: Decompression stroke after metering, backpressure at the end of metering, injection velocity, wear, melt viscosity, and design of the non-return valve and screw geometry. In conjunction with a newly developed positive-closing non-return valve (type: Smartshut, manufacturer: Engel Austria GmbH, Schwertberg, Austria), the advantages o...
Kunststoffe international, 2014-01-23, Trend Report: The Devil Is in the Detail
...tting tools, a vortex occurs, which leads to circulation of the material. With the new counter current technology, this vortex does not move in the transportation direction of the extruder, as in the past, but in the opposite direction. The relative velocity in the feed zone thereby increases at the transition from the cutter/compactor to the extruder. The extruder screw forms an additional cutting edge and mills the material out of the vortex. In this way, more material is fed in independently ...
Kunststoffe international, 2014-03-21, Composite Materials (Part 2): Self-Reinforced Thermoplastic Composites
...nificantly from the measurement, its agreement with a viscoelastic computation (Giesekus-Multimode model) is convincing. From the simulation results, however, further information can be extracted, which is not accessible experimentally. The velocity field for the viscoelastic results shows a significant change with respect to the parabolic profile of the Newtonian computation (Fig. 4, right). This also leads to a change of the extensional component of the flow. In Figure 5, the flow form at the ...
Kunststoffe international, 2014-04-14, Trend Report (Part 2): Fiber Composite Systems for Lightweight Construction
...enables a high degree of automation of this process step [3, 15, 16]. The speed of impregnation is dependent on the part dimensions and complexity, but more particularly on the process conditions. In the vacuum-assisted process, the flow velocity is drastically lower than in the HPRTM process (variant 4 in Fig. 2). These and further variants that are described in detail e.g. in [16] permit a short cycle time, a high degree of automation and a very high utilization of the characteristics of the l...
Kunststoffe international, 2014-04-14, Ultrasound Injection Molding: A Screw Is Not Always Necessary
...the energy required for melting and flow of the thermoplastic polymer molecules. The melt is forced into the cavity via a narrow gate. The injection pressure of the machine is maximum 300 bar; the shot volume is about 1 cm3. The injection velocity is not relevant – the material remains fluid as long as the ultrasound is switched on. The cooling time begins when the ultrasound is switched off. Then the polymer solidifies and the parts are removed as soon as the mold is opened. The sprue itself is...
Kunststoffe international, 2014-07-22, Faster to Series Production Through Simulation
...udies etc. to compare simulated and measured pressure profiles with each other. Comparison of the partial filling grade of a test platen mold and the simulated flow front reveals very good agreement (Fig. 2). Darcy’s law states that the flow front velocity ν is a function of the permeability K, the viscosity μ and the pressure gradient ∇p. Fromat a constant flow-front velocity, higher viscosities and lower permeability (less-permeable semi-finished fiber parts) give rise to higher cavity pressur...
Kunststoffe international, 2014-07-22, Making Mixing Transparent
...tretching flow components while simultaneously reducing the shear loading. Theoretical ConsiderationThe shear rate of a fluid moving in the x-direction is defined as:In the case of simple plate flow, a Newtonian fluid can be assumed to have a linear velocity profile (Fig. 1).In the co-rotating twin-screw extruder, the biggest shear rates occur at two places: first in the shear gap between the rotating crest and the stationary interior wall of the barrel, and in the nip between the two rotating k...
Kunststoffe international, 2014-07-22, Smart Color Exchange
...his method makes use of the properties of the polymer itself. At a critical shear stress, the phenomenon of wall slip occurs with many plastics. The presented process makes deliberate use of this phenomenon for color exchange.Injection Velocity Corresponds to Shear RateAs a reference, first a color exchange is carried out without varying the injection velocity, i.e. in a conventional way. The injection velocity is then often not sufficient to achieve wall slip in all hot-runner sections. However...
Kunststoffe international, 2014-08-19, All-Electric Even for High Clamping Forces
...ons that cap the load peaks.The prerequisite for rapid movement of the mold mounting plate is new spindle types that Engel has developed together with its supplier. Thanks to a greater spindle pitch, they permit a higher platen velocity for the same rotational speed than is the case with a hydraulic injection molding machine. The motor, too, was enhanced in cooperation with a long-term supplier for use in the new machine. In addition, controlled cooling of the lubricant was integrated. In the 6,...
Kunststoffe international, 2014-08-19, Further Increases in Heat Resistance
...n polymers are generally problematic, since in aging processes a large number of reactions take place in parallel and no reaction can be considered in isolation. In this case, however, there is a reciprocal relationship between the reaction velocity and layer thickness. The dependency on temperature is expressed by means of an exponential function. This describes the dependency of the layer thickness on the exposure temperature by means of an Arrhenius equation:t: layer thickness; A: pre-exponen...
Kunststoffe international, 2014-10-10, Simulated Thickness Distribution
...n the throughput distribution in pre-distributors is to be analyzed in order to derive measures for homogenizing the pre-distribution. The most important objective in the design of spiral mandrel dies for blown film extrusion is to ensure a uniform velocity distribution at the die outlet. This is a prerequisite for a homogeneous wall thickness distribution over the circumference of the extruded annular film, which in turn is crucial for the economy of the process and the quality of the film. A ...
Kunststoffe international, 2014-11-26, The Right Changeover Point for Each Shot
..., is precisely controlled and characterized by high reproducibility [1]. Conventional approaches to stabilize the process constancy are principally based on controlling machine parameters such as temperatures, positions and pressures. The screw velocity is kept constant during the injection phase and the melt pressure is kept constant during the packing phase, However, experience shows that injection molding machines do not always produce parts of identical quality, even with precisely reproduce...
Kunststoffe international, 2014-12-18, A Little Extra?
...changing the part properties, as regards the process technology, within certain limits. For example, a lower gas content usually involves the formation of a thicker non-foamed outer layer. The mold temperature, or melt temperature, and the injection velocity influence the sandwich structure and therefore the properties of the part. Detailed investigations on the influence of the processing parameters are described, for example, in [4].Different Process Goals in Combination with Negative CoiningA...
Kunststoffe international, 2015-02-28, High-Tech for Mature Markets
...me. This solution results into a constant performance of approximately -65 °C with an advantage of consistent efficiently processing. The honeycomb solution cannot reach this efficiency, neither in terms of energy consumption nor in processing velocity.The first of such units was developed within two months. However it was soon detected that a 12,000 dm3 hopper, which contains up to 10 t of granulate and a throughput of 1,500 kg/h, requires a process airflow of 3,750 m3/h and static pressure of ...
Kunststoffe international, 2015-02-28, Laser-Based Dynamic Mold Temperature Control
...0, 100 and 200 µm) and two fields have peaked structures (50 and 100 µm). The beam diameter is 14 mm. The microstructured region is heated by different laser tracking paths. Based on this heating study, the rectangular shape at a travel velocity of 8,000 mm/s was chosen for the further evaluation (Fig. 4).In this case, a maximum temperature of 340 °C and a resulting temperature during injection of 240 °C could be achieved. Since there is a linear relationship between the resulting temperatures a...
Kunststoffe international, 2015-05-21, Wrinkling – How to Prevent It?
...itive Molding …First of all, wrinkling in the molded part can be influenced through the machine settings. For instance, the compression rate of the material, which is critical for the formation of wrinkles, can be reduced by lowering the velocity of the air escaping from mold during forming. The risk of wrinkling is also reduced if the material is not cooled to quickly, i. e. the mold is not operated at too low a temperature. At the same time, however, it must be kept in mind that overly hot mat...
Kunststoffe international, 2015-07-20, Clear Sight with New Light
... input in absorber-free laser transmission welding and to limit the vertical expansion of the HAZ. One approach is irradiating the welding contour quasi-simultaneously by guiding the laser beam multiple times along the contour at a high velocity (> 1 m/s). It was originally introduced to obtain a larger gap-bridging capability resulting from the nearly uniform heating of the entire contour, which in turn allows a joining path comparable to that of ultrasonic or hot plate welding [6]. In absorber...
Kunststoffe international, 2015-07-20, Do Not Forget the Cooling
...aging. As regards production performance data, the packaging industry plays in the Champions League. Whether it makes a profit or loss depends on the cycle times. To be among the winners, it is necessary to make adjustments at two points: first, the velocity of the machine movements, for example during opening and closing the mold halves or during ejection of the parts and, second, the cooling time. The latter is obtained from the part shape and the temperatures of the melt and mold surface. The...
Kunststoffe international, 2015-07-20, Quality Rarely Comes Alone
...n the mixed material was processed and the viscosity control was activated. The Priamus control system (type: 7080A Fillcontrol Control P) controls the viscosity of the melt cycle for cycle by automatically adapting the injection velocity (= shear rate) and the melt temperatures (= shear stress) [3].In the tests, a basic setting was again chosen at which the molded parts are not completely filled in order to allow even the most minor changes to the process to be optically tracked. The evaluation...
Kunststoffe international, 2015-07-20, When Do Moldings Have Chill Marks?
...ature difference between mold segment or pre-stretcher and the heated thermoplastic at the point of contact, andthe contact time.By analogy, the parameters when cooling with a concentrated air current are:The temperature of the air, andthe air velocity.Several Possibilities for Reducing Chill MarksThere are numerous approaches to reducing, minimizing or even preventing the formation of chill marks. One possibility is to reduce the temperature difference between mold segment or pre-stretcher and...
Kunststoffe international, 2015-08-17, Additive Preforming for High-Volume Production
...the outlet of the fiber guide unit, the orientated fibers impinge onto the spray-up mold where they are temporary fixed by vacuum. The binder is activated by hot air.The investigations have shown that beside the fiber guide unit the lay-up velocity, with which the robot moves the fiber spraying head, has a decisive influence on the achievable fiber orientation. Figure 2 shows the flexural strength (DIN EN ISO 14125, three point bending test) of components, which were manufactured in an RTM-proce...
Kunststoffe international, 2015-08-17, Exhaust Air Cross-Sections – How Large, How Many?
...ding of the finished part, the required air is generally injected through the same channels. Only in exceptional cases, when, for example, chill marks could be produced on the molding at certain channel cross-sections due to an excessively high flow velocity during pre-blowing, the channels for pre-blowing and evacuation are designed separately. Really important is that the air is extracted in the whole area of the molding surface, i. e., also in the waste section of the molding that is later cu...
Kunststoffe international, 2015-08-17, Giving Pressure Greater Weight
...ce data provided for the polypropylene material were consulted.The following approximation applies for the pressure drop in a thin cavity whose width W is far greater than the thickness H:(5)Here v_ represents the mean velocity of the melt front. The representative viscosity ηrep can be computed with the help of the representative shear rate(6)according to the Carreau model(7)with the material-dependent parameters η0, λ and n .η0 designates zero viscosity and λ designates the reciprocal value of...
Kunststoffe international, 2015-09-18, Tool Deflection More than Halved
...turer: HRSflow, a division of the INglass Group S.p.A., San Polo di Piave, Italy) permits precise and flexible control of pressures and flow rates throughout the injection molding process. It was designed to allow individual control of the position, velocity and acceleration of the individual valve pins. In addition, the aim was to prove that, thanks to the combination of such a system and cascade injection molding, tool deflection significantly decreases. The demonstrator component is geared to...
Kunststoffe international, 2015-10-12, High Tech in Thin Layers
...his is most successful on ever faster and wider production lines. The latest generation of film-stretching lines from Brückner Maschinenbau GmbH & Co. KG, Siegsdorf, Germany, permits a production capacity of 7,500 kg/h with a width of 10.4 m and a velocity of 525 m/min. (Fig. 2). According to the manufacturer, the first plants that are already in operation show high production stability with the appropriately good film qualities. They thereby fulfill the film manufacturers’ requirements for ever...
Additional information about this tradename, like producer contact address, etc. can be found at www.materialdatacenter.com. For access to this extra information a registration is requested. Free online registration is available.
Note: the information in Material Data Center was collected with maximum care, based on information from material producers. They are subject to short term changes at the market. There is no warranty for the correctness of this information. In no way this information can be seen as a legal advice, whether certain tradenames are protected or not.