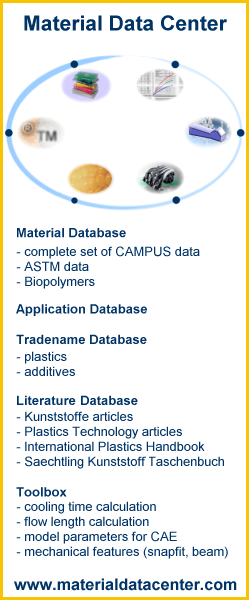
Material datasheets available free. Online registration at: www.materialdatacenter.com
Hybrid - PC+ABS, PC+PBT, PC+PET - Ravago Manufacturing Americas
Material Data Center is a leading international information system for the plastics industry. Material Data Center offers a comprehensive plastics database, calculation tools, CAE interfaces, a literature database and an application database. For more information about Material Data Center visit www.materialdatacenter.com.
A search for "Hybrid" in Material Data Center leads to the following information:
|
|
Material Data Center offers information about the following products with the requested tradename. To view a datasheet, please click on the relevant product.
Plastic-metal hybrids are replacing all-steel structures in automotive front-end modules at an accelerated rate. What"s more, technical approaches to hybrids are multiplying as more resin suppli...
Plastics Technology, 2004-06-30, Plastic-Metal Hybrids" Momentum Is Building
Prospects for metal replacement with plastic-metal hybrid (PMH) structures continue to improve, one advance being the launch of an unconventional PMH process by the British-based Corus Group. A Dutch ...
Plastics Technology, 2006-06-08, What to See at NPE 2006: Materials
...opments are flame-retardant PC/ABS blends made with nanoparticles, extension of plastic-metal "hybrid" technology into all-plastic versions, a new line of PC/polyester alloys from PolyOne, a...
Plastics Technology, 2007-10-04, Long-Glass PP Makes InroadsIn Automotive Front Ends
...trong candidate for replacing compression molded PP glass-mat thermoplastic (GMT) sheet, as well as hybrid systems made by overmolding engineering plastics onto metal.
Plastics Technology, 2010-11-02, Algae to Replace Starch in Bio-Hybrid Compounds
In the continuing search for renewable raw materials to replace petroleum feedstocks in plastics, the newest candidate is … seaweed.
Plastics Technology, 2010-12-07, 'Organic Hybrid' Composites Highlighted at K Show
...month’s K 2010 show in Dusseldorf was the replacement of plastic-metal “hybrid” composites with all-plastic “organic hybrids” in s...
Kunststoffe international, 3D Printing with Pellet Extruded Plastics on Metal
...anisotropy, the 3D-printed test specimens reach the property range of injection molded parts. Why Does 3D Printing Plastics Need Metal? The integration of metal components in 3D-printing is advantageous for several reasons. Firstly, hybrid structures offer the opportunity to use materials according to requirements. Secondly, flat structures, which can only be printed inadequately by hatching operations, can be easily integrated. The flat, aerial pattern is simply added to the process as a semi-...
Kunststoffe international, Alternatives to Gluing and Mechanical Joining
...s is a special challenge for joining technology. Thermal direct joining together with suitable surface treatments enables stable joints between very dissimilar materials combinations, thus ‧offering an alternative to classic procedures for joining hybrid parts. Plastic/metal hybrid parts are being used increasingly in numerous branches, such as the automotive, aerospace, or electronics industries. The joining of dissimilar materials continues to present a special challenge to joining technology....
Kunststoffe international, Amorphous Metals Combined with Elastomers
...mponent injection molding opens up new opportunities for designing housing frames that are almost indestructible while enjoying better protection from dust, water and radio waves. “Fully automated hybrid production is unlocking huge potential, especially for the consumer electronics industry,” Gerhard Dimmler, Senior Vice President of product research and development at Engel Austria, states. “Our development work has confirmed that, in multi-component injection molding, it is possible to create...
Kunststoffe international, An Impact Way beyond its Small Market Share
...e phones, tablets and electric tools are a promising growth market for PVDF. The field of electrical mobility is seeing a similar sharp increase in demand for powerful, lightweight and cost-efficient batteries for hybrid and electric ‧vehicles. PVDF is used as an electrode binder and separator coating in these batteries. Manufacturers such as Solvay, Brussels, Belgium, and Arkema, Colombes, France, have been constantly expanding their product range in this sector over recent years. Electrode bin...
Kunststoffe international, Bring on Electromobility!
...remains the world’s biggest auto manufacturer. Daimler and BMW also increased their sales figures in the past year. There are also the first ‧indications that the market for electric cars is picking up speed. VW, for example, sold 140,000 hybrid and all-electric cars last year – an increase of 80 %. And Tesla, too, with 367,500 units in 2019, increased its electric car sales by 50 % year on year. The planned Gigafactory in Brandenburg, Germany, also shows that the Americans are confident about s...
Kunststoffe international, Delivering Efficiency Even in Harsh Environments
...subject to fundamental change. Government reg‧‧ulators are demanding more CO2-efficient solutions and the environmental awareness of customers is growing. The result is a wave of OEM vehicle launches in battery electric vehicles (BEV), plug-in-hybrid electric vehicles (PHEV), hybrid electric vehicles (HEV), eVTOL (electric vertical take-off and landing), electric buses, e-scooters, and e-bikes. Across a variety of under-the-hood applications, PEEK has already become a material of choice for OEMs...
Kunststoffe international, Diverse Shapes and Applications
...ide a perfect surface even for high gloss aesthetic applications. It can be combined with the hot stamping technology and helps to reduce production cost. Luran S also makes inroads into the development of new electric and hybrid vehicles. An example is Lixiang that builds unpainted exterior applications with the help of the AS) material. For Lixiang, Beijing, China, the enhanced UV resistance and lasting premium high gloss appearance with mold-in pitch black color of the ASA grade were the key...
Kunststoffe international, Drivers of Electromobility
...rds electromobility, the automotive industry is facing a radical change. In the transition period, manufacturers will strongly diversify the powertrain. By optimizing internal combustion engines (ICEs), switching to alternative fuels and introducing hybrid cars, they are reducing their overall fleet emissions. At the same time, they are building competences in electric engines expand their offers of fully electric vehicles (EVs). The fuel cell vehicles developed by some manufacturers are also dr...
Kunststoffe international, Fast and Effective Start of Production
...llenges are emerging for services related to molds. This is where the global, high-performance infrastructure of Barnes Molding Solutions enters the picture. The slogan here is “globally qualified local manufacturing.” The so-called “Global Hybrid Qualification” offered by Molding Solutions, a strategic business unit within Barnes Group (see Box p. 8) involves technology transfer based on global manufacturing capability, for which all units are tailored and harmonized for qualification of custo...
Kunststoffe international, Foam Beads in Gliding Flight
...an urgent need for action. One year after the status report “Schaumperlen im Aufwind” (Kunst‧stoffe 2/2019, pp. 21–28, only available in German), it is time to take stock. Even after the SamPa joint research project (Integral Production of Hybrid Lightweight Sandwich Structures by Multicomponent Particle Foam Injection Molding for Large Series, Forel Platform) came to an end, the work is continuing – with new partners – though behind the scenes and in “gliding flight.” A key role in this is play...
Kunststoffe international, Green Shape Changers
...putational Design (ICD) at the University of Stuttgart, Germany, have undertaken a joint research project. In this project, a bioplastic-based structure was developed that changes shape in a pre-calculated way in response to humidity. The layered hybrid structure responsible for the shape change was manufactured generatively by a strand-laying process using two filaments with different sensitivity to humidity. Smart Structures Produced by a Strand-Laying Process The strand-laying process (fused...
Kunststoffe international, Half a Million More Parts
... Their production involves them in producing parts for the automotive industry, communication industry, electronics, and electrical engineering. For this purpose, the plastic production is equipped with 25 injection mold machines, on which the hybrid parts are extrusion-coated with the plastics at temperatures between 250 °C and 400 °C. In order to guarantee high product quality, the filigree forms (Fig. 1) were removed from the tool maintenance an average of once a week. They were cleaned in an...
Kunststoffe international, Killing Problem Microbes
...stroys the cell membrane of the germs without allowing them to adapt. It is applied in an online process after extrusion or thermoforming and then cured thermally or using UV light. ViaClean Technologies LLC has developed proprietary thermal, UV and hybrid cure antimicrobial treatment formulations, either water based or solids, which can produce a durable, non-leaching, and non-migrating antimicrobial treatment to a wide range of plastic surfaces. The treatments were tested and found to be effec...
Kunststoffe international, Present in a Multitude of Trends
...ruction where space is limited. There are numerous automated processes available for their economical and large-scale processing, such as automatic tape laying (ATL), automatic fiber positioning (AFP) or hybrid molding. The latter integrates the forming of composites into injection molding, enabling the direct functionalization of a component, for instance with fastening elements, guides and fixtures. This makes it possible to produce complex components in a one-shot process. As thermoplastic sy...
Kunststoffe international, Putting Hybrid Components to the Test
The different thermal expansion of plastics compared with metals makes it difficult to design components that combine both materials. A new test procedure simulates in a time lapse the aging process of plastic-metal hybrid components when temperatures change. Using two contrasting test procedures, reliable information can be ‧derived to assist in the designer. Metal or plastic? Traditionally, many automotive components are made from either one or the other material. But in the field of e-mobilit...
Kunststoffe international, The Potential of Redesign and Part Consolidation
Hybrid production chains have been increasingly in the spotlight in recent years. This also applies to the ‧combination of conventional manufacturing and additive processes in tool construction. With the example of an injection molding tool, it is shown how mold inserts produced by additive manufacturing can greatly shorten cycle times, and thereby significantly reduce unit costs. The important thing is to find a suitable combination of processes from the variety available. Over recent years, ad...
Kunststoffe international, Ultrafast 3D Printing
...d with conventional 3D printers. Because of the short manufacturing times, a closed material loop and the possibility of being able to subsequently subtractively process the components in one clamping (additive-subtractive hybrid manufacturing), the component costs can be reduced to a fraction, in particular for small series and prototyping, while achieving the same surface quality as for the standard FLM process. Variable Wall Thickness Conventional injection molded parts are usually designed a...
Kunststoffe international, What Can You Do at Fall Fairtime, When There Aren’t Any?
...ot by the HiQ Flow assistance tool. Sustainability Underlined The applications exhibited at Dr. Boy’s technical center in Neustadt-Fernthal, Germany, strongly emphasize sustainability and resource conservation. A Boy 80 E hybrid machine is the mechanical engineering highlight. It is equipped with a newly developed E-Drive injection unit where the injection and metering movements are driven by two servomotors. The rotary and axial movements of this Servo-Plast Unit are performed electromechanical...
Kunststoffe international, Zero-Waste Concept for Carbon SMC
Composite materials are often the key to lightweight design for many applications. However, these hybrid ‧materials face a major challenge where recycling is concerned. There is still no solution to the recovery of long and continuous fiber-reinforced materials. Where it is possible at all, only downcycling has been feasible until now. Four research partners have therefore set themselves the goal of developing a new press forming technology as part of a zero-waste project. Whether for automotive...
Kunststoffe international, 2005-11-21, 42V Power Systems: More Power in Cars of Tomorrow
...d with 42V power are shown in Fig.1. Implications for Components and Engineering Plastics In the course of technological development, an immediate, complete changeover to 42V will be avoided because that would be too costly. Instead, dual 12/42V hybrid architectures will be used in cars for a transition period in order to introduce new technologies based on 42V step-by-step. The gradual implementation of this new basic technology will set in train far-reaching changes in presentday automotive ...
Kunststoffe international, 2005-11-21, A Comparison of Drive Technologies
... A wide-ranging survey was conducted with the aim of providing an objective basis for the debate on electrical and hydraulic drive technologies in injection moulding machines. This investigation is based on measurements on electrical, hydraulic and hybrid drives for injection moulding machines. The machines are in industrial service with various plastics processors, some of whom have been using the various drive technologies for several years. The controversy on alternative drive technologies...
Kunststoffe international, 2005-11-21, A Comparison of Hybrid Machines
A Comparison of Hybrid Machines Injection Moulding with a Combined Drive Concept Ansgar Jaeger, Schwaig/Germany Thin-wall, high-precision parts require a high plasticization capacity, high dynamic response of injection and accurate reproducibility. Practical examples show that a drive concept with hydraulic accumulator and electrically driven clamping unit can meet these requirements with low energy consumption. A high-performance injection machine should allow short cycle times, operate...
Kunststoffe international, 2005-11-21, A Short Time-To-Market Process
...their core competencies for co-operative development of integral front-end modules for motor vehicles. The advantages of integrated front-end modules could be demonstrated using a prototype in the context of the development study. By integrating the hybrid assembly carrier, illumination engineering, radiator and condenser modules into a system the entire module became smaller and lighter. With the exception of the headlight glass all parts of the prototype for the front-end module (hybrid assemb...
Kunststoffe international, 2005-11-21, Additives: Tough and Heat-resistant: New Silicone Particles for Thermosets
...en Ebenhoch, born in 1966, has been involved in research into novel silicone copolymers and silicone nanoparticles at Wacker since 1997. He has been head of strategic marketing for the Hybrid Materials Project House at Wacker Silicones since the beginning of 2004; genioperl@wacker.com. Fig. 1. Nanoscale silicone spheres: homogeneous, opalescent solution of silicone particles with a diameter of about 100 nm Fig. 2. Core-shell particles: soft flexible silicone core with a grafted-on acrylate p...
Kunststoffe international, 2005-11-21, Adhesives: What Do Adhesives Accomplish in Practical Processes?
... testing a selection of bonding agents [6]. Incorporation of the Bonding Agent The production of NFRP is dominated by what can be termed "mat processes". This involves manufacturing the prepreg, generally as a natural fibre polypropylene hybrid mat, and turning it into the finished component by compression moulding. Additives like bonding agents can be incorporated into the composite by the powder technology, which involves sprinkling them onto the substrate as it passes underneath (Fig....
Kunststoffe international, 2005-11-21, All-plastic Hybrids: Thermoplastic Hybrid Structures
Reinforced Plastics Thermoplastic Hybrid Structures All-plastic Hybrids. Light alloy hybrids were yesterday, the future belong to plastic-plastic combinations. Hybrid structures made of thermoplastics with continuous fibre-reinforced reinforcement elements have high integration variability with low weight and good economy at the same time. Ralph Funck Markus Steffens Light, lighter, lightest. The use of light alloys and highly specialised steel alloys is natural today. What will be the next inn...
Kunststoffe international, 2005-11-21, All-round Talent: Polyvinyl Chloride (PVC)
...n recent years. For selective control over product properties, especially rheology, different variants of these two methods are to be found, such as predispersion, or a combination of emulsion and microsuspension methods for the manufacture of hybrid products. Further developments are headed in the direction of seed-swell methods for producing highly disperse and monodisperse particles. Overall, unlike the case for the suspension method, the situation is characterised by highly heterogeneous tec...
Kunststoffe international, 2005-11-21, Automotive Conference: Lightweight Construction as Magic Phrase
...s were implemented. Steel and magnesium then drew level in the property profile. And soon the buzz phrase amongst all the experts was "competition among materials". Nowadays, innovations are more likely to be found in the material mix. Hybrid construction with steel, aluminium and plastic now holds out the promise of success as still measured in terms of weight savings and improving comfort. Competition among Materials Spawns the Material Mix In the bodywork of the new BMW 6 series (Tit...
Kunststoffe international, 2005-11-21, Bonding of Plastics
...ow quantities of heat and, unlike bolting, it does not damage the parts. Bonding allows maximum exploitation of material properties during production and enables new designs, such as lightweight structures, to be practised. Even in the by now common hybrid design, i. e. the joining of the most diverse materials of metals and/or plastics, bonding technology demonstrates its superiority. While thermoplastic polymers are weldable, thermosets are not. Bonding is the only method other than mechanical...
Kunststoffe international, 2005-11-21, Close Cooperation Ensures Success
...perations. The low-shot weights also need new plasticising units, while the raw materials themselves have to satisfy the demands made on the final product yet nevertheless have low enough viscosity in the molten form to fill the cavity exactly. The hybrid technology, i. e. the combination of various types of material in one product (e. g. a metal encapsulated by a thermoplastic), makes it possible to synergistically combine the specific advantages of both materials. A much cited example is the ...
Kunststoffe international, 2005-11-21, Continue to Improve Productivity and Quality
...ay in building large discontinuously operating co-extrusion blowing installations and in the production of large volume articles (for instance storage vessels for the chemical and foodstuffs industries, rain water cisterns and white water canoes). Hybrid and Completely Electric Clamping Units Next to the clamping unit the extruder unit with parison die is a central component of a blowing machine. Particularly with packaging machines the trend is toward all-electric blowing machines. Fischer W....
Kunststoffe international, 2005-11-21, Control Engineering: New Technical Beginning in Machine Control
...rburg is reacting to the increasing requirements of the fields of - automation, - processing methods (multi-component equipment and turntable machines) as well as - propulsion technology of the machines with the three concepts hydraulic, hybrid and electric. Continued development adapts the controller constantly to current needs in the injection moulding market. With Selogica Arburg developed an instrument that lastingly advanced control engineering due to its high flexibility, integration cap...
Kunststoffe international, 2005-11-21, Costs and Performance: A Comparison of Drive Technologies
Costs and Performance: A Comparison of Drive Technologies Far-reaching studies based on measurements on electric, hydraulic and hybrid injection moulding machine drives used in production were carried out to clarify any open questions regarding drive technologies in injection moulding machines. These comprehensive tests are in addition to the comparisons carried out in previous studies. Johannes Wortberg, Thomas Kamps A practically relevant comparison of the various types of drive includes...
Kunststoffe international, 2005-11-21, Crash Simulation: Computer Modelling
...plications, plastics today have so far only been used in the form of energy-absorbing foams. In recent times, however, there has been a clear trend towards using plastics for intelligent reinforcement of structural components. Examples include many hybrid components, i.e. components that combine metal and plastic in a specifically targeted way. But all-plastic parts can also be sensibly used in many applications. In the area of pedestrian protection, in particular, there is great potential for p...
Kunststoffe international, 2005-11-21, Cutting Costs by Insert Moulding
...thout the need for any downstream operations. To make this possible, designers try to integrate a number of functions into a single component, with operational reliability taking first priority. This line of development has led to insert moulding, a hybrid technology. In insert moulding, inserts (normally made of metal) that have undergone punching, bending, turning etc. in a prior fabrication process, are placed in an injection mould and encapsulated in plastic. The combination of metal and pla...
Kunststoffe international, 2005-11-21, Developing Customised Compounds
...d. The bearing bush shown in Fig. 2 was made from an anti-friction-modified, carbon-fibre reinforced polyamide 66. In addition to the known properties of carbon fibres, polyamide 66 also meets the requirements for oil resistance and heat resistance. Hybrid-reinforced thermoplastics, i. e. products with reinforcing and filler combinations, e. g. of carbon fibre, glass fibre, glass spheres or various minerals, allow selective adjustment of mechanical properties and the shrinkage and warpage of cor...
Kunststoffe international, 2005-11-21, Drive and Applications Technology: All-Electric Broadside
...d as a vertical unit so as not to enlarge the footprint. The nozzle extension and retraction and the nozzle contact pressure are realised with a small integrated hydraulic unit. The weakening of the all-electric philosophy in favour of hybrid drive technologies was in many cases forced by practical necessities. Many moulds are still equipped with hydraulic core pullers. In the case of servo-electric rotary tables, locking is by means of an index pin and often hydraulic because of the dynamic adv...
Kunststoffe international, 2005-11-21, Drive Technology: Reproducibility and Costs Are Primary Concerns
...ract definitive information about control quality from the recorded curves without additional data such as speed and pressure curves. Irrespective of the control quality, it is possible to determine that: in both cases, the fully electric and hybrid machines record increased dynamics (Figs.2 and 3). However, no reservoir techniques were used in the hydraulic injection moulding machines surveyed here. If suitable reservoir and/or servo techniques were employed in the hydraulic system, a differen...
Kunststoffe international, 2005-11-21, Elastomers
...d mixing times. The increasing assault by TPE-Vs as substitutes for EPDM for profiles in partial applications is increasingly leading to creative combined solutions made from hybrid materials TPE-V/EPDM based on new expanded machine concepts: For example, LWB-Steinl presented an injection moulding system for the corners (VCE, 500kN C-frame press), and Krupp Elastomertechnik, together with DSM, presented a process and plant concept for coextrusion of EPDM/TPE-V, for which a patent application ha...
Kunststoffe international, 2005-11-21, Electrifying: Emphatic Confidence
...nd cosmetics. The SynErgy series had increased its share of Group sales from 41 to 44% (Fig. 2). Netstal's customers could choose between two different drive concepts for the production of optical storage media, he said. Both the Discjet with hybrid drives, 4000 models of which had been sold, and the all-electric e-Jet, sales of which were in excess of 150 since its release in May 2003, could be integrated as subsystems into all replication lines. Merki said that the market volume in the opt...
Kunststoffe international, 2005-11-21, Energy Consumption: How Much Energy Does a Drive System Need?
...weight and cycle time, because we can directly derive from this the product-related energy saving. The figures for the specific energy consumption without heating (only drive and control systems) were - with machines having electrical or hybrid drive systems, in the range between 470Ws/g (0.132kWh/kg) and 3,696Ws/g (1.026kWh/kg), - with hydraulic machines, in the range between 1054Ws/g (0.292kWh/kg) and 13226Ws/g (3.673kWh/kg). The percentage comparison of the specific energy consumption in Fig...
Kunststoffe international, 2005-11-21, Engineering Plastics: Products for Innovative Processes
...to 40% higher output rates. For structural components and underhood applications, Lanxess is supplying a new 60% glass-fibre-filled Durethan PA6 grade with a tensile modulus of 20000MPa at room temperature and a value of 6700MPa, even at 170°C. In hybrid technology, particularly, use of the new material leads to components with higher rigidity and flexural/torsional strength. In the second generation of Durethan-B-Easy-Flow grades, flowability has been improved by around 22%, while mechanical p...
Kunststoffe international, 2005-11-21, Escalators Made of Plastics
...displays sufficient inherent stability in the region of the front edge and the riser, the rear edge requires an additional support. Pure ribbing would have been highly complex at this point, and would have increased the weight of the component. The hybrid solution that was chosen, with a thin-walled steel pipe clipped into the reinforcing rib on the rear edge after injection moulding, also has further advantages: it simplifies the injection mould, and the pipe subsequently forms a sound connecti...
Kunststoffe international, 2005-11-21, Evolution, Not Revolution
...e cooling channels into the mould. In the authors' view, rapid tooling techniques have the potential to at least challenge spark erosion in terms of costs and time. Quality-wise, they are still at the quick-and-dirty stage of development. The hybrid tooling mould combines perhaps the synergies of conventional and rapid tooling technologies. Process Chain Completed Aside from observing and taking on board new technical developments, the most successful service providers are putting themselv...
Kunststoffe international, 2005-11-21, Exhibition Preview: North American and Canadian Products at K 2004
...ne Plastics Technology have assembled a selection of the most important developments. With this thematically structured preliminary report you can effectively prepare your visit at the K show. Injection Moulding News from includes all-electric and hybrid machines, large two-platen presses, multi-layer PET preform systems, and structural-foam presses. Plenty of new hot-runner nozzles and controls will also debut in Dusseldorf. All-electrics or Hybrids Demag Plastics Group, Strongsville/Ohio, pl...
Kunststoffe international, 2005-11-21, Expansion Injection Moulding: Amazingly Thin
...thickness ratios of up to 400:1). X-Melt can be used with engineering plastics such as PC, PBT, LCP, PA, POM and ABS+PC. Suitable machines for expansion injection moulding are all-electric machines of the Engel E-Motion and hybrid machines of the Engel Victory electric series. References 1 N. N.: Company brochure: Firmenschrift über Hydrospeicher. Hydac International GmbH, Sulzbach, 2004 2 Steinbichler, G.: Präzisionsspritzgießen – Maschinen- und prozesstechnische Besonderheiten. 17. Leobener K...
Kunststoffe international, 2005-11-21, Export Champion: Changeover Completed
...e Asian Plastic is Taiwan’s number one. The mother company, the Chen Hsong Group, belongs to the largest manufacturers world-wide of injection moulding machines. Among the products are double toggle lever, hydraulic clamping system, two-plate, hybrid and electrical machines. At the K2004 among other things the injection moulding machine SM-5EJ with a 5 tonnes closing force and an injecting speed of 800mm/s was shown, with which precision parts under 1g for were produced for medical technology. V...
Kunststoffe international, 2005-11-21, Extremely Fast
...g the raw material industry, system producers and polyurea users. At the first international PDA conference in New Orleans in early December 2000, an exact definition of the term "polyurea", particularly as distinct from pure polyurethane or hybrid systems, was proposed as the basis for future certification. Other objectives include the achievement of uniform standards in training users and user safety. Those interested in obtaining further information about the PDA please contact: kenb@...
Kunststoffe international, 2005-11-21, Hard-soft Composites with Metal Inserts: New Generation of Plastic-Metal Hybrids
Automotive New Generation of Plastic-Metal Hybrids Hard-soft Composites with Metal Inserts. Technical and functional advantages can be generated by using a combination of different materials. Metal-hybrid parts consist of metal support structures over-moulded with functional plastic elements. A damping inter-layer to reduce loading and warpage can be introduced between the metal and plastic by means of MCDS (multi-component damping system) technology. Gottfried Steiner Ralf Gerndorf The charac...
Kunststoffe international, 2005-11-21, High Increase in Consumption: Polyamides (PA)
...and electronic systems. The causes for this impressive success are always the same: the advantages of PA design as a result of lower weight with increased functionality and significantly lower costs. The combination of plastics and metal results in hybrid parts that integrate numerous functions and therefore permit new manufacturing processes, such as modular design. But challenging design solutions in the engine compartment, such as the engine cover for eight-cylinder engines at BMW can be mad...
Kunststoffe international, 2005-11-21, High-grade Bath Concepts: Pampering the Senses
...s, too, greatly appreciate the clean surface on the back of the polyurethane-reinforced bathtubs and shower trays because they no longer run the risk that a protruding glass fibre will break off and become lodged under the skin. The Hybrid Bathtub A completely different bath concept also makes use of the excellent properties of polyurethane: A hybrid acrylic and steel tub, held together by a layer of polyurethane. The firm Kaldewei has been offering this interesting hybrid solution for a good...
Kunststoffe international, 2005-11-21, How Much Drive Would You Like Then?
...ion moulding or blow moulding, translatory movements predominate; these can generally be achieved through central, electrohydraulic drives, although they could also be generated by decentralized, electromechanical or electrohydraulic drives [1, 2]. Hybrid Machine Offering Enhanced Efficiency Adaptation to the power requirements poses no problems with electromechanical drives in the case of continuously- operating machines, which means that there is no superfluous power to be eliminated. With a...
Kunststoffe international, 2005-11-21, Hybrid Moulding: Getting the Combination Right
Getting the Combination Right Hybrid Moulding. Production of injection moulds needs to be fast, flexible, inexpensive and durable. Problem is, however, that none of the standard mould making techniques actually combines all of these requirements. A way out of this conundrum is to combine the various standard processes with novel ones. Hybrid moulding is one such solution. Thorsten Hickmann Eric Klemp Injection moulds are used to produce plastic parts made from elastomers, thermoplastics and t...
Kunststoffe international, 2005-11-21, Hybrid Profiles in EPDM and TPV
Hybrid Profiles in EPDM and TPV Production with Single-Step Technology Ger Vroomen, Heerlen/Netherlands and Lothar Köster, Hamburg/Germany Multi-component applications in EPDM and thermoplastic vulcanisates (TPV) can be economically produced by a newly developed and patented hybrid coextrusion technique. The main advantages of the process are the high freedom of design of components produced in this way and the reduced number of production stages. Rubber, with its flexible, elastic and e...
Kunststoffe international, 2005-11-21, Hybrid Technology with Braided Preforms: Ski Poles by Multilayer Technology
Composite Material Ski Poles by Multilayer Technology Heiner Becker Hubert Schneider Hybrid Technology with Braided Preforms. Modern plastic technology, if intelligently applied and developed, offers the possibility of injection moulding thermoplastics with endless-fibre reinforcement. These plastic-plastic hybrids can solve problems of conventional designs and replace traditional composites in selected applications. Thermoplastic materials with endless fibre reinforcement are principally use...
Kunststoffe international, 2005-11-21, Hybrid Technology: Tailor-made Thermoplastics with Layer Structures and Continuous Fibre Reinforcement
Hybrid Technology: Tailor-made Thermoplastics with Layer Structures and Continuous Fibre Reinforcement Novel, complex, multi-layer thermoplastic composite parts for lightweight applications in the transport sector are being manufactured on an application-specific basis by multi-layer/sandwich injection moulding with embedded reinforcements made from continuous fibre preforms. Optimised microstructure and interfacial adhesion are crucial to the outstanding mechanical properties of this new clas...
Kunststoffe international, 2005-11-21, Hydraulic and All-electric Injection Moulding Machines in Practice
... on conversations and interviews with injection moulders, some of whom have been producing on injection moulding machines with different types of drives for many years. Drives for injection moulding machines – all-hydraulic, electromechanical or hybrid – have been the subject of hot debate for some considerable time. For many years, the number of suppliers of electromechanically driven injection moulding machines was restricted to a few manufacturers. In recent years, though, it has increased ...
Kunststoffe international, 2005-11-21, Injection Moulding (1): Innovation at Closer Inspection
...mselves at closer inspection. To summarise roughly, the trend is to increase component priority in order to remain in the international competition. Thus the well-known procedures are re-combined – with surprising results … Production of Metal/Hybrid Parts The production of metal parts from magnesium alloys with the injection moulding process (thixomoulding) is not new and at least in Asia well established. According to Stephen LeBeau, Executive Vice President with Thixomat, altogether about 2...
Kunststoffe international, 2005-11-21, Injection Moulding (2): Increasing Productivity and Cost Efficiency
...extents. This holds true of all the market segments that are served by injection moulding machine manufacturers: from packaging technology and the automotive sector, right through to precision and medical-engineering applications. Trend towards the Hybrid Machine One trend that was already clear at the last K and which was similarly in evi-dence this time round is machine concepts that can be classified under the heading of "hybrid". A number of manufacturers offer modular machines whic...
Kunststoffe international, 2005-11-21, Injection Moulding Technology for the Packaging Industry (1): Pace Setters Reduce Costs
...ons that help the customer control operating costs and remain competitive have always been the focal point of this program. Reduced Energy Consumption and Clamping Force At its plants in Bolton/Canada and Dudelange/Luxemburg Husky also builds the (hybrid) injection moulding machines belonging to the Hylectric series that forms the basis for system solutions for containers and lids. The Hylectric, which is available with clamping forces from 1200 to 10000kN, combines the energy efficiency of a...
Kunststoffe international, 2005-11-21, Injection Moulding Technology for the Packaging Industry (4): Differentiation of Products for Thick and Thin
...eased economy", says Catoen. "The combination of our machine and mould technology with Hekuma's robots offers cycle times that are much shorter than before, with the same high product quality." The heart of the system is a Hylectric hybrid injection moulding machine. With the widest tiebar spacing in its class in the industry, it not only gives scope for customised mould layout, but also leaves sufficient space for side-entry labelling robots. Guidance of the movable platen on l...
Kunststoffe international, 2005-11-21, Injection Moulding Trends: Increased Complexity and Tighter Specifications
...posed on the injection moulding can only be met by a flexible system which permits both drive variants to be combined in a single machine. On this point, it is important for a mechanical engineering company not to supply fixed-configuration hybrid machines but to have the full range of machines, from all-hydraulic to all-electric, on offer instead. Only in this way can customers put together a machine specially tailored to their requirements and thus exploit the advantages of both drive variants...
Kunststoffe international, 2005-11-21, Injection Moulding under Clean Room Conditions: Machine and Process Technology for Medical Products
...higher-grade execution of the machine, there are surely reasons for this decision, for instance, preparing in advance for use of the machine in a more stringent clean room class. Between the hydraulically powered and fully electric machine there are hybrid solutions in which various drive types are possible for the individual axes (Fig.1). The processor can select the type of drive for the machine components on the basis of product requirements. The sum total of the benefits should be the decidi...
Kunststoffe international, 2005-11-21, Innovation and Efficiency: Bayer: Success by Splitting the Plastics Activities?
...blends with a high polystyrene content. “We want to take our products and technologies that are already successful in Europe into other regions of the world,” Fink explained, and as an example quoted hybrid technology and applications in the car engine compartment, both based on polyamides from the Durethan product line. Fink underscored that “For Lanxess, too, technology will remain an important part of the added value.” “The market for styrene plastics is characterised by distinct regional dif...
Kunststoffe international, 2005-11-21, Innovative Direct Processing of Natural Fibres
... lower material costs and easier recycling and handling, there is now a growing trend towards thermoplastic matrix materials, such as polypropylene. So-called natural-fibre-mat-reinforced thermoplastics (NMTs) are primarily processed in the form of hybrid fabrics consisting of variable proportions of natural and synthetic fibres. Conspicuous by their Absence in Automotive Construction Up to now, injection moulding and extrusion have played a minor role in the production of natural-fibre compos...
Kunststoffe international, 2005-11-21, Integrated Automation: Manufacture Economically – Exploit Resources
...ectronics. Multi-axis industrial and linear robots that can be configured in a modular manner to the specific requirements are available for each machine size and type. Starting with standard solutions, the supplier can offer even hybrid solutions based on a combination of several robots and robot types in order to fulfil the customer’s request. Usually, the processor must expend a great deal of time and expense to have the production cell that it puts into operation tested for CE conformity. Up...
Kunststoffe international, 2005-11-21, Interface Definition: Design of Fabric-reinforced Thermoplastics
... the non-linear stress/strain behaviour was examined by means of consolidated flat sample bodies. Among others, samples of Twintex from Saint Gobain Vetrotex, Cambery/France were tested in short-term tests. Twintex consists of a PP/glass hybrid roving. This is processed to form fabrics and can be consolidated into sheets. Fig.3 compares test results and FE analyses for cases in which the fibres of the reinforcing fabric are oriented at ±45° to the loading direction. Because of the large deviatio...
Kunststoffe international, 2005-11-21, Interview: Quo Vadis Polycarbonate Glazing?
...spoiler. The part can be multicoloured and that fact creates additional freedom in design. The requisite part rigidity can be obtained by corresponding geometries as well as by using plastic-metal composite technology, otherwise known as hybrid technology. This can easily produce systems whose rigidity matches that of corresponding solutions in glass and metal. At the moment, we have various glazing projects with modular assemblies in the development phase. ? Don’t you fear competition from othe...
Kunststoffe international, 2005-11-21, Interview: “With the Four Pillar Strategy, We Are on the Right Track“
...t new developments this generator of know-how produced that the Division was able to launch on the market? What new innovations are planned? Spindler: Concerning new developments of new marketable products, the emphasis is on the hybrid polymers division (key word: nanocomposites). Polymers with innovative characteristics due to the use of nanomaterials and the representation of three-dimensional items in Lucite blocks (laser marking & welding) are other topics of interest. We began our investig...
Kunststoffe international, 2005-11-21, It All Depends on the Blend
...lly very brittle thermoset matrix resins [2]. The disadvantages of modification include high production costs and a greater or lesser drop in stiffness and thermal resistance of the composites. Another way of improving resistance to damage is to use hybrid fibre materials, such as hybrids of carbon or glass filaments with polyethylene, aramid or polyester fibres [3]. The disadvantages of this approach, however, are the high production costs for the hybrid fibres and the reduced mechanical proper...
Kunststoffe international, 2005-11-21, It’s the Benefit Alone that Counts
It’s the Benefit Alone that Counts Comparison of the Performance of a Hybrid and an All-electric Machine Gerd Liebig, Schwaig/Germany Injection moulding machines with electric drives generally offer greater accuracy and a lower energy consumption than hydraulic variants. On the Ergotech El-Exis E which has electric drives for the main movements, the injection time, cycle time, switchover point and switchover pressure are well within the tolerances specified for demanding engineering parts....
Kunststoffe international, 2005-11-21, Joining Technologies: Lightweight Hybrid Structures
Transportation Lightweight Hybrid Structures Joining Technologies. The development of loadbearing hybrid structures has a key role to play in the competitive use of continuous-filament- and textile-reinforced plastics for high-performance products made by lightweight construction. The joining technologies required for this must be optimally matched to the material structure of the joint components to ensure transfer of high load forces. Werner Hufenbach Lothar Kroll Olaf Helms In modern lightw...
Kunststoffe international, 2005-11-21, Laser Welding A Mature Joining Technique
... of the different refraction. Welding Carbon-Black Parts by Laser The Institute for Plastics Processing (IKV), Aachen/Germany, is studying laser transmission welding for microsystem engineering as part of its special research on "Assembly of Hybrid Microsystems". In addition to pursuing technology advances, it is closely examining the influence of the carbon black during laser transmission welding. Often, laser transmission welding utilizes carbon black particles for the absorbing join...
Kunststoffe international, 2005-11-21, Lightweight Construction: Hybrid Front-end Combines Contradictions
Automotive Hybrid Front-end Combines Contradictions Lightweight Construction. Hybrid front-end frames appear to have become established as standards in the development of new vehicles. The trend is driven by the possibilities for optimising crash behaviour, weight, overall size and ease of assembly. Samuel Kiefer Important development aims for the front-end frames of the new A8 were improved ODB crash behaviour (offset-crash with deformable barrier), further reduction of the part weight, and ...
Kunststoffe international, 2005-11-21, Lightweight Construction: Natural Fibres in Automotive Interiors
...hermoset concepts, in these cases, the matrices such as EP resins or PU are applied to the fibres by spraying (e.g. the Duo-Conti process and NafPurTec), and subsequently consolidated and shaped in the press mould. For thermoplastic-bound systems, hybrid mats (natural fibres and PP fibres) are predominantly used and are formed in a cold mould by means of a preheating station. For both systems, various bodies are currently examining whether hemp fibres can potentially be used. Cost-Effective and...
Kunststoffe international, 2005-11-21, Locally Reinforced Parts: Tailor-made Light
...o a further development in process engineering, materials tailored from a combination of long and continuous fibre reinforced thermoplastics in combination with flow-optimised polymer melt geometries constitute a serious alternative to metal-plastic hybrid structures. The term tailored LFT refers to parts made of long fibre reinforced thermoplastics (LFT) with integrated local part reinforcements in the form of fabric, profiles or parts-specific unidirectional fibre reinforcements. Depending o...
Kunststoffe international, 2005-11-21, Market Report: Taiwan’s Plastics Industry
...icted that the focus of all future efforts will be on the development of full electric-driven system, hydraulic-driven system and hybrid system (electric and hydraulic). In regard to the plastic injection moulding technology, the trend will be to develop high speed and productivity, micro and light shaping and supercritical fluid foams. On the other hand, the emphasis will also be on high speed and torsion, innovation of control system, moulding manufacturing techniques, and ultra-high speed wit...
Kunststoffe international, 2005-11-21, Materials Recycling
... at the same time. As a rule, the recycled material - at least from the production scrap that is predominantly available - can be returned to the original application. In the engine compartment, we frequently find metal inserts, clips, plastic/metal hybrid constructions and plastic/plastic composites. Because of the difference in the stress/strain properties between plastics and metals, it is relatively easy to separate plastic/metal composites by grinding the component down. Ferromagnetic metal...
Kunststoffe international, 2005-11-21, Microsystems Technology: In-mould Assembly via Microinjection Moulding
...ng competes with processes such as gluing, soldering and bonding. To permit a comparison of the processes and evaluate the advantages and disadvantages, the bond strengths of the various systems must be known. To test the bond strength of the hybrid test specimen, an experimental setup (Fig. 6) based on the principle of the pull-out test was used [7]. In the setup shown, the insert is cylindrical in shape and is overmoulded with a plastic ring. To investigate the adhesion between the cylindrica...
Kunststoffe international, 2005-11-21, Minutes of a Development Record: From Zero to the Road in Seven Months
...reinforcement elements. Afterwards the CAD data was passed on to NC programming. Seven weeks still remained to the planned completion date for production of all the model parts. While almost all external skin model parts were developed using the hybrid approach with mixed mesh and surface data, for engineering reasons this procedure was not possible for production of the windows and some lighting components. Here there are polynomial surfaces with class A surface quality requiring curvature and ...
Kunststoffe international, 2005-11-21, Modular Drive Systems in the Spotlight
...actual power requirement steplessly through a frequency converter ohne/mit = without/with Fig. 4. Presenting the new modular drive unit with hydraulic and hybrid injection moulding machines: (l. to r.) Herbert Kraibühler, managing director technology, Michael and Juliane Hehl, managing partners of Arburg, and Michael Grandt, managing director sales and controlling
Kunststoffe international, 2005-11-21, Modular Drive Technology
...ility As a measure of the precision of the machine and the attainable process consistency, we should look at the minimal fluctuations in the shot weight. In the production of a lightweight blade holder for one-way shavers (shot weight 15.7 g), the hybrid machine shows a better result in direct comparison with the Ergotech system - which is already very good. Whereas the fluctuation tolerance of the shot weight over 15 cycles is around 0.07 g with the hydro-mechanical machine, it is down to 0.03...
Kunststoffe international, 2005-11-21, Modular Systems for Hydraulic Drives: Tailor-made “off the Peg”
...ance. Hydraulic drives have been continuously developed over years. They currently offer not only more performance together with significantly improved precision and lower energy consumption than, for example, ten years ago. For some time, “hybrid” drive concepts have also been available, in which hydraulic machines use a plastication unit with an electromechanically driven screw. An electric motor is particularly suitable for the rotational movement of the screw during plastication, since it i...
Kunststoffe international, 2005-11-21, Modularity: Multitalented Machine for Economical Injection Moulding
Injection Moulding Multitalented Machine for Economical Injection Moulding Modularity. The modular design of the new CX Series from Krauss-Maffei increases the number of variations available and offers the processor a wide spectrum of hybrid drive configurations. In this way the injection moulding machines can be individually matched to specific production requirements. Thomas Hörl Markus Betsche The new CX Series of injection moulding machines introduced at the K 2004 (manufacturer: Krauss-Ma...
Kunststoffe international, 2005-11-21, More Transparency and Greater Production Area
... that the Allrounder C, with clamp forces from 300 to 2200 kN, accounts for about 50 % of total production. For K'2001, a new machine with a clamp force of 800 kN is to be presented, which will then be available with, optionally, all-hydraulic, hybrid, or all-electric drive. The Allrounder S, with 3200 kN clamp force, is also to be presented at K'2001. Michael Kömpf Sales growth at Arburg GmbH + Co. acc. to regions
Kunststoffe international, 2005-11-21, Mould-making 2000
...on steels no. 1.2767 and no. 1.2343 (for improving wear resistance on sliding surfaces) were the state of art. Only small sections were produced in highly heat-conductive beryllium copper (BeCu). Nowadays cavity inserts in heat-conductive alloys and hybrid cores (steel-Amcoloy/Moldmax) are state of the art and are subject to continuous, progressive development. Efficient cooling layout demands a more elaborate design of the cavity inserts (Fig. 7), requiring a greater number of components each. ...
Kunststoffe international, 2005-11-21, MuCell Process: Microcellular Parts from the Injection Moulding Machine
...on and perpendicular to it, to that found in PA6GF25. Summary The possible applications of the MuCell process have certainly not yet been exhausted. In many cases (such as in-mould decoration and hybrid moulding), it can be expected to provide a suitable complement to established special injection moulding processes. Its advantages include the increased flow-path/wall-thickness ratio and increased freedom of design. However, material savings are only gained in the case of parts without critica...
Kunststoffe international, 2005-11-21, Multi Mould-carrier Technology: Equipping the Injection Moulding Machine with Two Moulds
...laten injection moulding machines of the Quadloc series (13500–54000kN). The clamping unit on these machines is equipped with the Reflex plates developed by Husky, whose platen area shows even pressure distribution at full clamping force. The hybrid machines – with a hydromechanical clamping unit and an electric drive for plastication – of the Hylectric series are also available in a Tandem design (6500– 10000kN). They are particularly suitable for thin-walled parts with ...
Kunststoffe international, 2005-11-21, Nanocomposites - En Route to Application
...resins, have been used for a number of years now to increase the impact strength of epoxy resins (e. g. Albidur from Hanse Chemie). One broad field of application for nanocomposites is the development of ceramic materials and inorganic/organic hybrid materials by the sol-gel process for use in scratch-resistant coatings on glass, for example. Development work here has produced a series of inorganic nanoparticles that are dispersible in aqueous and organic media. Examples include synthetic, dispe...
Kunststoffe international, 2005-11-21, Nanostructured Coating Materials: High Quality Plastic Surfaces
Nanotechnology High Quality Plastic Surfaces Nanostructured Coating Materials. Hybrid polymers, or nanocomposites that are produced via the sol-gel process from organo (alkoxy) silanes, main group or transition metal alkoxides and other components have become important products of chemical nanotechnology. Surface treatment of engineering thermoplastics represents one specific field of application. Gerhard Schottner Klaus Rose Sabine Amberg-Schwab Chemical nanotechnology represents one of the k...
Kunststoffe international, 2005-11-21, New Service Forms
New Service Forms Hybrid Drive System and "Pay-as-You-Use" Scheme for Injection Moulding Machines In 1999, Demag Ergotech GmbH, Schwaig/Germany, managed to maintain its market position in the declining European customer markets. All in all, the company booked orders last year for 2,000 machines. The consolidated sales of Demag Ergotech Group amounted to DM 477 million in the last financial year. Overall, the Demag Ergotech Group was able to consolidate its market position during la...
Kunststoffe international, 2005-11-21, Only the Application Determines the Prototype
..., one or more material prototypes will be dispensed with in the future. Realistic parts tests on functional prototypes or technical prototypes will remain an irreplaceable link in the development chain and stimulate a constant demand for prototypes. Hybrid prototypes and the hybrid moulding tool enable the economics of many specifications to be tested. The demand for such prototypes and moulds has the potential to rise disproportionately. We would like to thank the companies who provided intervi...
Kunststoffe international, 2005-11-21, Optimising Safety Systems: Modern Chainmail
... (Fig.1), woods, aluminium foam and thermoplastics. For this project, the developers at the Technical University of Ingolstadt are seeking an industrial partner in the plastics processing field who can support this hybrid technology in medium-sized to large production runs. It should be capable of producing large-area chainmails, i.e. in a size from 2m¥20m, which are necessary for safety systems. Where thermosets or thermoplastic matrices are used as embedding materials in conjunction with chain...
Kunststoffe international, 2005-11-21, Past the Trough
...nd special processes. In the meantime, with their offerings in the field of electric drives the Europeans caught up with the lead of the Japanese and American producers. Today almost all machine manufacturers have electrical and/or hybrid machines in their programmes. However, so far according to data of the VDMA this technology is only hesitantly accepted by European processing plants. The share of newly installed machines with electric drives amounts to 3% in Europe while in North America it i...
Kunststoffe international, 2005-11-21, Perfect optical symbiosis
...s already described using the same paint system. The parts are then joined already after the cathode deposition coating and/or primer paint finish. While the development just described is based on purely thermal hardening by precipitation, so-called hybrid procedures achieve their goal using a two-stage hardening by precipitation process. In the first step the bonding molecules are cross-linked using ultraviolet (UV) radiation without external heating. The following final hardening by precipitat...
Kunststoffe international, 2005-11-21, Perspectives at the Start of a New Millennium
...de with current efforts by the automotive manufacturers. It is said that, in just five years' time, a fuel cell will be standard on selected car marques. The new drive systems, methanol or hydrogen fuel cell coupled with electric drive or even a hybrid drive (combination of combustion engine and electric motor) imbue plastics with additional chances on the market. The central element of the fuel cell, namely the proton-exchange membrane (PEM) is a polymer film with polyelectrolytic propertie...
Kunststoffe international, 2005-11-21, PET in Packaging
...The "Stehning" process from OHL, which was implemented on an industrial scale in Germany in 1999, works by a similar principle. Here, the washed post-consumer PET flakes are first extruded and post-condensated in discontinuous processes. The hybrid "UnPET" process from URRC is another development that has already been implemented in Europe. This process works with a chemical stage in which the surface of the PET flakes - and thus any contamination sticking to the surface, such as...
Kunststoffe international, 2005-11-21, Pipe and Profile Extrusion: Continually Increased
... suitable for the production of blanks, since the use of a knife allows the very precise output to be exploited. The plant can also be used for profile extrusion. Berstorff also presented a plant concept for the production of high quality rubber and hybrid profiles. The centrepiece of this profile line is the high-performance rubber extruder VAC GE 90 SC x 16D (Fig.2), which is driven by four three-phase asynchronous motors via a pinion shaft. The specially developed barrel venting and Stiftconv...
Kunststoffe international, 2005-11-21, Planning Future Scenarios: Automotive Applications in the Distant Future
...affic infrastructure, alternative drives, macroeconomic and technological advances and social values. Input from the “Alternative drives” sphere of influence, for example, included the descriptors fuel-cell drive, hydrogen engine and hybrid drive. Possible applications yielded by the scenario analysis included nonbonded, flexible, flat conductor systems based on polycarbonate film (smart wiring) that is back-injected and processed into fully switched modules. Such film would be a space-saving al...
Kunststoffe international, 2005-11-21, Plastic Bodies
...d be to apply a backing to a facing film by means of in-mould injection lamination or foaming with highly filled polymers. However, work still needs to be done on films pigmented in automotive colours, especially on colour matching metallic paints. Hybrid Semistructures Semistructure part are parts that meet mechanical requirements while allowing integration of functions. Typical examples include door interiors, hatch doors and front modules. Traditionally, steel doors and steel hatch doors ar...
Kunststoffe international, 2005-11-21, Plastic Spare-Wheel Well
...plastication into a processable compound. Compounding is carried out by the semifinished goods producer. GFT (glass fabric reinforced thermoplastic) Fabric serves as the reinforcing element in this class of materials. There is a choice of glass or hybrid fabric available. When the requirements of the spare-wheel well project for the S-class were analysed, it was decided to use a UD-reinforced material because it deforms like metal. This decision was essentially based on the results of crash tes...
Kunststoffe international, 2005-11-21, Plastic-Metal Hybrids
Plastic-Metal Hybrids Possibilities of Producing Structural Components Marcel Op de Laak, Gerhard Pötsch und Klaus Schwitzer, Freiburg/Germany The mechanical characteristics of hybrid metal components can be improved by more than 50 % by applying new concepts. Costs can be reduced by making use of the possibility to integrate additional functions for instance in a front end module. "The result of crossing two genetically different individuals is called a hybrid. The most different ch...
Kunststoffe international, 2005-11-21, Plastic/Plastic Hybrids: It Doesn’t Always Have to be Steel
Composites It Doesn’t Always Have to be Steel Plastic/Plastic Hybrids. Plastics are conquering new ground which used to be primarily the preserve of metals. Hybrid structures comprising inserts made up of either fabric-reinforced or glass mat-reinforced thermoplastics or thermosets, with injected-on plastic ribbing, have the same load-bearing capacity as comparable structures in steel. Sonja Pongratz Hans Laich If an individual material comes up against its limits, new horizons can be opened u...
Kunststoffe international, 2005-11-21, Plastics Packaging in the 21sup>st/sup> Century
...awson Mardon new generations of laminating adhesives (producers include Henkel, and Rohm & Haas) and also substitution of the laminating process through the application of sealable coatings (such as by Quix Rotoflex) development of organic/inorganic hybrid polymers which, when used in combination with the inorganic barrier layers, can increase barrier properties several times over again (example: Ormocer coating and adhesive systems developed by the Fraunhofer Gesellschaft) development of multi-...
Kunststoffe international, 2005-11-21, Plastics Processing in the Future
...uition. Let us recall, for example, that the injection moulding technique with internal gas pressure was patented back at the beginning of the seventies and took one and a half decades to become a broadly accepted process in plastics processing. The hybrid technology (injection moulding of large area plastics/metal parts) also deserved to have been implemented more quickly because it admirably combines the processing advantages and design benefits of plastics with the high rigidity of metals for...
Kunststoffe international, 2005-11-21, Polyvinyl Chloride (PVC)
...nnolit technology, via internal cooler reactors, in which the cooling coil is in direct contact with the suspension. New developments for the manufacture of paste PVC include swelling processes for highly monodisperse particle distributions and hybrid technologies, such as combinations of emulsion and microsuspension processes. It remains to be seen what cost and competitive advantages can be gained by these measures. Product Developments and Applications With a consumption of about 1.5million...
Kunststoffe international, 2005-11-21, Pressure Vessels: A Question of Curvature
...thout increasing their weight significantly. Pressing is likewise considered extremely economical. For average requirements domes made of glass mat thermoplastics (GMT) are appropriate. For high requirements the spherical membrane bases made of hybrid fabrics are pressed. Preliminary tests showed that at the usual temperature load of +80°C a fabric reinforcement with high fibre volume fraction is most suitable. The connection openings of the vessel can be pierced in the fabric layers of the dome...
Kunststoffe international, 2005-11-21, Process combinations: Intelligent Machine Technology for Flat, Lightweight Components
...y. The many different possibilities offered by this machine are aimed particularly at efficient production of functionally integrated, flat, lightweight components by low-flow film or textile in-mould lamination, microcellular foaming technology and hybrid technology. Plastics are being increasingly used in the transport sector for flat, lightweight components in various modes of transport such as motor vehicles (Fig.2), railway trains or aircraft. With their versatile properties, they offer c...
Kunststoffe international, 2005-11-21, Processes and Trends in Injection Moulding
... made from transparent plastics, e.g., vehicle glazing, mirrors and prisms, must also satisfy very high optical demands. They must be free of distortion and internal stress in all axes. Injection-compression moulding is a suitable process here [5]. Hybrid Technology Hybrid technology affords a suitable means of combining the advantages of metals with those of plastics. Metals typically have a high elastic modulus, high rigidity, good accident properties and high heat resistance. There are variou...
Kunststoffe international, 2005-11-21, Project “Colorado”: Rapid Prototypes for Rapid Cars
...es to obtain prototype parts that are as close as possible to the final product in an early phase of the development of a plastic component. The company protoform Konrad Hofmann GmbH, Fürth/Germany, works exclusively with this hybrid technique for production of prototypes. First of all, SPM rapidly provides simple injection moulds with which, secondly, plastic parts and assemblies can be produced in the desired material via all common methods and in all of the usual plastic resins. For this reas...
Kunststoffe international, 2005-11-21, Railroad Rolling Stock: On Track with Lightweight Construction Techniques
...ly since the end of 2002. The train conceived with wide wagons using the construction block principle unites 100% low floors with great passenger comfort taking modern materials into account. The power supply units (choice of diesel, electrical, hybrid and in the future fuel cell) are placed on the roof to save space and are covered with hand-laminated glass fibre reinforced roof aprons. For repair and maintenance purposes the train heads attached to both ends in the so-called A-wagons are imple...
Kunststoffe international, 2005-11-21, Reinforced Plastics: Caught Up Again
...ystems, such as BOPP film systems. Ralf Schledjewski Fig. 1. Low-wear, lightweight underbody system in SymaLite (photo: Quadrant Plastic Composites) Fig. 2. Profiles in thermoplastic with endless fibre reinforcement and its use in a hybrid structure (photo: Comat) Fig. 3. Front end module in Tailored LFT-D (photo: Dieffenbacher, Fraunhofer ICT) Fig. 4. Property comparison of a soggy wooden panel and a LaminaeX composite panel. Contrary to the case for plywood panels (rear), LaminaeX panels...
Kunststoffe international, 2005-11-21, Replacing Established Plastics. . .
...Established Plastics. . . By PP/Flax Compounds Impact-Modified with PET Fibres Günther Pflug and Stefan Reinemann, Rudolstadt/Germany The toughness of polypropylene/flax and polypropylene/-flax/wollastonite composites can be increased using a hybrid construction involving ductile, high-strength PET fibres. The prerequisites are optimum composition and gentle extrusion conditions. To date, natural fibre/polymer composites with notched weak points at edges and walls are greatly limited in ...
Kunststoffe international, 2005-11-21, Retrospective: The Development of Injection Moulding
...lectrohydraulic (so-called “hydraulic“) drive (1932 to 1950) - IMMs with preplasticising and plunger injection (1950 to 1956) - IMMs with a screw-equipped assembly for melting and injection, the screw having either electric (so-called ” hybrid machine”) or hydraulic drive (since 1956) - Automation of IMMs, machines with closed-loop control (since 1960) - Process control (since 1970) - Automated injection moulding plants (since 1980) - Massive introduction of special techniques (since 1985, some...
Kunststoffe international, 2005-11-21, Rubber Processing: Smaller Batch Sizes and Automated Processes
...ith integrated gear pump. New Laboratory Extruder For many years now, the Model EEK 32.12 L laboratory extruder from rubicon, which was designed specifically for the rubber industry, has been among the market leaders in this sector. The hybrid system just introduced is an extruder with which both rubber mixtures and thermoplastic elastomers (TPEs) can be processed (Fig.3). In contrast to rubber extrusion, a greater range of screw speeds is required for processing of TPEs. In addition, the screw...
Kunststoffe international, 2005-11-21, Safeguarding the Economic Viability of Production Sites: Adding Value through Innovation in Injection Moulding
...ost benefit after an amortisation period of just one year. The same applies to the high reproducibility, with regard to both the shot weight consistency and the mechanical reproducibility of the entire mechanical movements (Fig. 4). Hybrid Machines for High-speed Applications Hybrid concepts have, for many years, been a useful variation for making the transition from a fully hydraulic to an all-electric drive. The term 'hybrid solution' is traditionally used to describe electric drives ...
Kunststoffe international, 2005-11-21, Simulation right through to Failure
Simulation right through to Failure Crash Simulations with Plastic/Metal Hybrid Parts Frank Lutter, Michael Münker and Martin Wanders, Leverkusen/Germany Structural parts for the automotive sector are being increasingly produced by hybrid technology. Newly-developed computation methods developed specially for crash simulation assist the design engineer with part design. Crash simulations provide a means of assessing the deformation behaviour, load-bearing behaviour and energy absorption ...
Kunststoffe international, 2005-11-21, Simulation Tools: Vibro-acoustic Design of Composites
...es. Moreover, in the future, modern lightweight applications will have to satisfy increasingly demanding vibro-acoustic requirements. Full exploitation of the acoustic potential of lightweight structures – especially fibre-reinforced multi-layered hybrid composites – requires suitable simulation tools for appropriate vibro-acoustic design. Olaf Täger Lothar Kroll Werner Hufenbach In addition to high specific stiffness and strength, lightweight structures of fibre-reinforced plastic composites ...
Kunststoffe international, 2005-11-21, Sports Equipment: Plastics at all Events
... to allow the boot studs to sink in better and dampen the impact of the ball. Because no sand rises to the surface, there is less risk of those dreaded skin grazes. The elastic layer also cushions the impact on the players' joints. Hybrid versions of artificial and natural grass are also possible. One of the Greek stadia, which was the venue for some of the Olympic soccer games, made use of this version from Desso called DDGrassMaster. A computer-controlled machine implanted over 20 million ...
Kunststoffe international, 2005-11-21, Strong Growth in Polyamides: Polyamide (PA)
...moulding machines with lower clamping forces, which provides more flexibility in machine selection and production planning. The easy-flowing grades have so far been used to produce housings, door handles, engine covers and radiator grilles. Hybrid technology has now secured a firm place in the automotive industry. With the use of Easy Flow variants, it is now possible in some cases to further reduce component weight through lower wall thickness. Special highly filled polyamide grades that are no...
Kunststoffe international, 2005-11-21, Strong Joint between Plastic and Metal
Strong Joint between Plastic and Metal Assembly Technology for Plastic-metal Hybrid Structures Ulrich Endemann, Stefan Glaser and Martin Völker, Ludwigshafen/Germany Collar joining is a new technology for joining plastic and metal sheet. It opens up new possibilities for hybrid construction. The joint is amazingly easy to produce, reliable, very cost-effective and offers good mechanical properties. In automotive engineering and other industries, the need for lightweight construction and ...
Kunststoffe international, 2005-11-21, Technology and New Dimensions
... upper limit for the injection moulding machines produced by Arburg. The company is also devoting a considerable amount of work to the development of an all-electric injection moulding machine. Until now, however, the Arburg range has only included hybrid machines, in which individual components such as the metering unit are driven electromechanically. However, the management is adamant that they will also be launching an all-electric machine at some time in the future. Arburg attaches major imp...
Kunststoffe international, 2005-11-21, The Trend towards Electrical Systems
...etition from fully electrical ones. At the Japanese Plastics Fair, IPF 1999, 80 of the 130 machines on show were fully electric. In Chicago at the NPE 2000, 72 % of all the machines displayed were hydraulically driven, 25 % were all-electric and 3 % hybrid [1]. According to estimates, the market share of all-electric injection moulding machines will increase to 30 % during the next five years. This would correspond to the situation currently existing in Japan. Of the 13,000 machines produced the...
Kunststoffe international, 2005-11-21, Trends at the IAA: Shop Window for Innovations in the Motor Industry
...s, there were also many offerings involving system integration or greater modularisation. The suppliers also pioneered a number of new safety and comfort elements and some new developments in materials technology. Fresh Stimulus for Hybrid Tailgates The French supplier Plastic Omnium once again focused its attention at the IAA on the concept of modular-designed engine hoods and tailgates, opting for a combination of thermosets and thermoplastics to save costs and weight. The system involves pane...
Kunststoffe international, 2005-11-21, Trends in Injection Moulding
...ing is a forward-looking technology. European machine manufacturers and processors are developing and producing at a peak technical level. To be successful, it is essential to recognize the trends at an early stage, whether towards fully electric or hybrid injection moulding machines, water injection or external gas moulding. Injection moulding machine manufacturers in Central Europe are showing positive balance sheets. Their international leadership in machine technology is paying for. This s...
Kunststoffe international, 2005-11-21, Trends in Injection Moulding: Specialists Increasingly in Demand
...und. Jürgen Schray The most striking innovations are undoubtedly happening in multi-component injection moulding. That is where more and more workflows are being automated and combinations of various high-tech plastics and of plastics and metals (hybrid technology) are being tried out. A current trend is to apply multi-component injection moulding to heat-resistant moulding materials, such as PEEK, PSU and PPA-LCP, which up until now have been processed alone. Electrical Parts are Being Injec...
Kunststoffe international, 2005-11-21, Varied Requirements: Innovations in Thermoforming
...stems. This is particularly important in Scandinavia because investments in energy-saving machine technology are frequently subject to tax relief. As an alternative to the conventional system of table movement, use can also be made of a hybrid system consisting of a toggle plus a pneumatic cylinder. The pneumatic cylinder balances out the disadvantages of the toggle, namely the low power transmission in an angled position. The volume of air in the cylinder is compressed during the downward move...
Kunststoffe international, 2005-11-21, VDI-K Automotive Congress: Progress in Smaller Steps
...XJ was akin to saving the weight of a baby elephant, or around 200 kilograms. However, the difference in the price of steel and aluminium bodywork means that the latter is only used for top-of-the-range models. Sullivan believes that a hybrid construction of steel and glassfibre-reinforced plastics has a greater chance of finding use in everyday vehicles. He also drew attention to the occasional surprising processing properties of plastics. For instance, a wing made from polymeric material can e...
Kunststoffe international, 2005-11-21, Welcome to the Future
...ew could change - from a complex and expensive melting tool to a simple mixing device. The prices for screws will fall to the same extent as their influence on the complex procedures during the melting declines. Electromagnetic Drive Systems While hybrid and electromechanical drive concepts are currently wrestling for dominance, we decided to look for new, even better solutions. An initial study produced highly promising results for the use of electromagnetic servo motors, above all as regards...
Kunststoffe international, 2005-11-21, What Customer Focus Really Means
...lopment of plastics machinery technology, particularly for the processing of plastics of high added value for the customer branches mentioned above. An increasingly greater role is being played by: - Thin-wall technology - Microinjection moulding - Hybrid technology - Sandwich injection moulding, and - Insert moulding (with high precision, short cycle times and machines dedicated to applications). Injection Moulding Technology Has High Innovation Potential Surface finishing, durability, optica...
Kunststoffe international, 2005-11-21, Which Drive for An Injection Moulding Machine?
...tual analysis to help them decide on the right drive technology. According to a Delphi study, 28 % of injection moulding machines in the year 2010 will be of the all-electric type. The remaining 72 % will be composed of 34 % all-hydraulic and 38 % hybrid machines [1]. More than four years have elapsed since this study appeared and it is now time to take a closer look at drive technology for injection moulding machines. Many advantages have been claimed for all-electric injection moulding machi...
Kunststoffe international, 2005-11-21, “Growth is not everything”
...l-electric ones in many areas of application. The question is which technique is the best for the process, the best for the customer. We have already convinced a large number of people through the performance of our hybrid machines. We get faster cycles and in many cases better shot-to-shot accuracy. Controlling electric machines is not that easy. As far as power consumption is concerned, we will not match that of an electric machine, but we are getting very very close. At K, with Coperion, you...
Kunststoffe international, 2005-11-21, “It Depends on the Part”
...g module is triggered, the film acts as a hinge for the bursting instrument panel. This can reduce the risk of injury to occupants. The film, process and handling were developed or modified specifically for this process. The Advantages of Hybrid Technology The injection moulding of “hybrid parts”, i.e. the combination of heterogeneous materials such as polymer and metal in a single-stage process is employed in the automotive industry essentially as an insert/outsert process. 3D-MID for moulded...
Kunststoffe international, 2005-11-21, “Nano Molding”: Permanent Bond between Aluminium and Polymer
...ld (iron) is approximately half that of aluminum alloy. Without taking this fact into account the pressed aluminum object expands about 0.1% more than the injection mould at processing temperature so that the hybrid parts of aluminium and polymer often became attached to the cavity wall of the injection mould when the mould was opened. As the polymer part is designed to remain on the core, opening the mould appeared to tear both sides. In some occasions, the moulded product was deformed. We carr...
Kunststoffe international, 2005-11-21, ”The Electrical is not Better in Everything, but it is a Viable Alternative”
...at the Alldrive can be downgraded to the hydraulic machine if the customer so wishes, but that we can start from the three main axes to upgrade – if so desired – to create an all-electric version. What do you have against the term hybrid machine? Nothing at all, it is just that the whole topic already has a long history at Arburg and the term hybrid did not exist at that time. We tend to place the emphasis on the modularity of the drive system: We are not building a specifically defined hybrid ...
Kunststoffe international, 2005-12-07, Competition: The Other Chinese
...an (Taiwan). Research and development were concentrated at APM, coming from Hong Kong. The provider offers almost any type of drive in the range from 50 to 32000 kN locking force, from double-knee lever to two-plate designs and hybrid and electrical machines. We spoke with Jerry Yen, European sales manager at Asian Plastics Machinery (APM), who said that machinery made in Taiwan is on the advance at present because it is a good value for money and because of the wide variety of products availa...
Kunststoffe international, 2006-01-09, Continuous Fibres: Local Reinforcement of Injection Moulded Components
...rmore, mechanical stresses are often very localised. So to achieve uniform material exploitation, structural stiffness must be modified. In injection moulding, this could previously only be done by increasing wall thickness, designing ribs or using hybrid constructions. For high stiffness and strength requirements, costly fibre composites have therefore been used – as an alternative to light metal alloys. Cost-efficient thermoplastic melt processing methods have become firmly established for com...
Kunststoffe international, 2006-01-15, Mouldmaking Technology at Fakuma und EuroMold: Engineering Lights Comes Out from Under the Bushel
...uction system, including automated packaging of the moulded parts. A view of their exhibit shows the specialisation: long parts with a handle, e.g. toothbrushes, writing instruments, hand tools and similar parts as 2-component or hybrid components. “In this production scenario, a quick model change is often essential. Through consistent use of a modular concept, which also includes the ejector assembly, we can exchange the part-forming components on the machine in under an hour.“ Even Zahoransky...
Kunststoffe international, 2006-01-31, LFT Parts: Local Continuous-fibre Reinforcement
... the moulding compound. Another process variant (Fig.1) is the manufacture of a wound reinforcing structure inline with the compression moulding operation. The reinforcing structure is preformed from an impregnated roving strand, e.g. based on a hybrid roving, by means of a winder. Welding of the Insert Structure The important prerequisite for the practical suitability of the continuous fibre structure is good adhesion between the continuous fibre-reinforced insert and the moulding compound. Th...
Kunststoffe international, 2006-02-22, Carbon-fibre-reinforced Plastics (CRP): The Black Gold of Lightweight Building
... non-pressurised rear fuselage. Cost-effective pultrusion has been used to make the almost 7-m-long floor beams for the cabins [13]. The wing components, i.e. both the inside front wing flap and the landing flap tracks, have been made from hybrid structures of carbon fibre, titanium and aluminium, primarily for load reasons. They are made by one of the primary suppliers of the A380, the EADS’ Augsburg/Germany plant, which is increasingly leaning towards in-house, patented VAP resin infusion proc...
Kunststoffe international, 2006-02-23, Electronic: Saving Weight and Costs with Flat Conductors
...r flat cable metre goods was developed and constructed in the context of a Bavarian Research Foundation research project at the FAPS institute. We are working with various industrial partners on possibilities for employing flat cable technology for hybrid vehicle electrical systems. The Authors Prof. Dr.-Ing. Klaus Feldmann, born in 1943, is head of the Institute of Manufacturing Automation and Production Systems (FAPS) at the University of Erlangen-Nuremberg and is chairman of the research ass...
Kunststoffe international, 2006-02-24, “Space Puzzle Molding“: Efficient Small Batch Production
...form) (3) The shock absorber parts have to meet strict requirements for precision, quality and strength. For this reason, they are of robust design (photo: Protoform) The Process: The SPM method (space puzzle molding), a hybrid technique as a mix of Rapid Tooling and Rapid Prototyping technologies, provides low-cost, simplified moulding tools made of aluminium based on a specially modified computer aided design. With these moulds, one may produce series of prototypes and small batches of pla...
Kunststoffe international, 2006-05-22, Market Overview: Sun over Taiwan
...pecially cooperation with foreign companies that helps both partners to prosper in the market. The company has 18 years of experience in construction of horizontal and vertical injection moulding machines (Fig. 2). In the area of hybrid machines and so-called high-speed injection moulding machines, Multiplas cooperates with the Japanese company Acess Technology, whose motion control unit is employed in Multiplas machines. There is also a cooperation agreement with the American company Gluco, Mic...
Kunststoffe international, 2006-05-23, Transparent Nanocomposites and Hybrid Materials: Invisible Helpers
Special. Invisible Helpers. Transparent Nanocomposites and Hybrid Materials. There would seem to be no limit to the variety of functional fillers. Inorganic nanoparticles can suitably be used for functionalising transparent plastics, since their small dimensions mean they are not visible to the human eye, yet they still bring completely new functions with them. Stefan Kaskel. Inorganic fillers have traditionally played a decisive role in adjusting the mechanical properties of polymers, suc...
Kunststoffe international, 2006-05-24, Chromogenic Plastics: Thermally Switchable Polymers Open up New Fields of Application
... systems in which temperature-induced colour or intensity changes occur are known as thermochromic [1]. Eight current projects focusing on the application potential of thermochromic polymers clearly demonstrate the great interest in their use as hybrid heat sensors or multifunctional chromogenic materials. Light-transmitting – Heat-reflecting. Although the first developments in this field, the hydrogels, have impressive optical properties [2], they have proved too complicated to process under i...
Kunststoffe international, 2006-07-04, Hybrid Machines: The Best of Both Worlds
Injection Moulding The Best of Both Worlds Hybrid Machines. All-electrics are in vogue. But anyone planning to purchase a new machine - whether all-electric, hydraulic or hybrid – should weigh up certain critical factors before making the decision. Jim Stewart The debate for and against hydraulic, hybrid and all-electric focuses all too often on energy efficiency. On this count, all-electric machine will almost always come off best. However, there are several other significant factors, such ...
Kunststoffe international, 2006-07-31, Sandwich Moulded Components: Atmospheric In-line Plasma in Medical Technology
...ss allows the most varied materials to be combined with one another. By means of rigid-flexible composites it is possible, for example, to provide housing components with a seal, to back inject decorative films with a backing material or to produce hybrid parts (metal-plastic composites). The objective is to combine as many different parts as possible in one and the same cycle. In this way the number of assembly steps can be reduced and process reliability increased. In order that the different ...
Kunststoffe international, 2006-09-05, Viscosity Measurement: Material Characterisation in Powder Injection Moulding
...less steel feedstock (material: 316L, manufacturer: Gabriel Chemie, Gumpoldskirchen). The curves were calculated by Power Approximation. Fig. 4. Flow processes in the melt-filled section of the plastification screw. Fig. 5. Hybrid machine, HM 40/130 type, with an energy-saving, servo-electrical metering drive and an Unilog B4 control unit. Fig. 6. Effect of Mould Temperature: Increased mould temperature reduces the injection integral. The MFQ value, in turn, is not affected by the mould tempe...
Kunststoffe international, 2006-09-10, Company History (4): Heading in New Directions
...ft HV combines both motions within a very small envelope. The Multilift versions V and HV are based on a overhead design. They were subsequently joined by a Multilift V in a cantilever design. In 2001 Arburg joins the discussion on the topic ”hybrid or all-electric machines“ by introducing the Allrounder A series. From the need to adapt the modular de-sign concept to the requirements of the industry, Arburg develops its own indi-vidual concept that is quickly accepted by the market. A practical ...
Kunststoffe international, 2006-09-27, Actuator Materials: Liquid Crystalline Elastomers for Microengineering
...d crystalline elastomers (FULCE) produce movements that make it possible to develop new technical actuators based on the principle of the human muscle. The technology, mode of operation and use of these effectors are described using the example of a hybrid microgripper. Tamás Fischl et al. Seven European research groups in the “FULCE” Research Training Network funded by the European Union have been working on functional liquid crystalline elastomers (FULCE) since 2003. The aim of the Ilmenau re...
Kunststoffe international, 2006-09-27, Trend Outline: Integration and Intelligence
...ast running mode is of major importance. But also hydraulic machines have become more and more sophisticated over recent years. The stress was on drive technology, controllability and energy optimisation, here. Moreover, applying hybrid solutions, a modular machine structure makes it possible to utilize the favourable features of the two drive systems by e.g. furnishing a hydraulic machine with an electromechanical dosing drive. Referring to hydraulic machines, also low-cost standard machines a...
Kunststoffe international, 2006-09-28, Laser Welding: Race with Beams
...rs of vehicles. With complex three-dimensional parts such as vehicle tail lamps, it is often impossible today to use a scanner system, since undercuts or adverse beam angles obstruct beam approach. Therefore they must be contour-welded. The hybrid welding method developed by LPKF provides certain advantages here. For instance, this technique permits for beam guidance by means of a bent-arm robot. The clamping unit required for pressure force is integrated in the welding head. The rolls employed ...
Kunststoffe international, 2006-09-28, Lightweight Construction: Advances in the Processing of Fibre-reinforced Plastics
...ment winding it is preferred to decouple the impregnation step by using semi-finished tape product which has already been fully impregnated. This allows very high fibre volume contents but is also associated with high material costs. Alternatively, hybrid rovings are used, but although they distinctly shorten the impregnation pathways, on account of the necessary input of energy they require costly preheating and relatively low process speeds. For high rates of material throughput at constant ge...
Kunststoffe international, 2006-10-11, News
... decorative paints, and acid, alkali & heat resistant grades for coloration of plastics and construction materials. The product portfolio is rounded off with a new innovative process for manufacturing a high-opacity and therefore economical hybrid pigment based on nickel rutile yellow and bismuth vanadate. Furthermore, the Heubach group in Langelsheim is investing 3 million EUR in an innovative manufacturing technology for the production of inorganic coloured pigments which will expand the capac...
Kunststoffe international, 2006-10-27, Lanxess: Ensuring Sustained Growth
...raw materials, Lanxess sees conservation of resources as a key aspect of sustainable development. In automotive engineering, for example, vehicle weight savings result in lower fuel consumption. This also explains the success of patented hybrid technology, in which heavy steel constructions are being replaced with composites made of thin steel sheets and a specially designed plastic rib structure. To date, according to Dr. Koemm, more than 20 million vehicles have already been produced worldwide...
Kunststoffe international, 2006-10-30, Car Electronics: Producing Intricate Parts Economically
...ion high-contrast laser etching has proved to be a further advantage of the material (title picture). The 16-pin plug for fuse and relay boxes developed by Molex, Ettlingen/Germany, is also used in car interiors. In the case of the so-called Sicma hybrid plug, due to the excellent flowability of the material it was possible to fill this under such mild conditions that the balanced mechanical properties of the plastic are retained. Thus, the elasticity of the component is high enough to accommoda...
Kunststoffe international, 2006-10-30, Injection Moulding: A Mirror Finish with no Visible Weld Seams
... monitor frame were planned to avoid visible welds. - Attractive surfaces are obtained by laminating the three-dimensional contours. Weber has built up an extensive range of in-house skills in special processing technologies. The system chassis is a hybrid part comprising a metal frame and high-strength polymer. This combination meets mechanical requirements from load-bearing through to crash properties, and includes precise bearing and mounting points for the pivotable monitor and fittings. Co...
Kunststoffe international, 2007-01-22, Comparison of Articulated Arm and Linear Robots
...asses, and ensures short paths between moulding removal and transfer to the packaging station Fig. 3. Fully automated installation for an automobile manufacturer: Four 4200kN machines produce hybrid strips as metal-plastic compounds. Demag linear robots insert the metal parts from the nozzle side of the mould, and remove the finished components from the clamp side. Six-axis robots transfer the mouldings to the finishing stations Fig. 4. Manufacturing cell for mobile phone displays with a cleanro...
Kunststoffe international, 2007-04-17, Ceramics Dressed as Plastics
Ceramics Dressed as Plastics Hybrid Parts Overmoulding of powder injection-moulded ceramic inserts opens up interesting possibilities for manufacturing plastics/ceramics hybrids on a large scale. This process was closely examined in a joint research project by the Süddeutsches Kunststoff-Zentrum (SKZ) and the Institute for Materials Research III at the Forschungszentrum Karlsruhe. Volker Piotter et al. The development of novel composites, in which the properties of different materials are ...
Kunststoffe international, 2007-04-17, Develop New Markets with Hybrid Components and Surface Treatments
Develop New Markets with Hybrid Components and Surface Treatments 2007 VDI Injection Moulding Conference For two days, February 14 and 15, Baden-Baden/Germany was once again the centre of the injection moulding industry. Because Germany’s domestic injection moulders are finding it increasingly difficult to compete costwise with the rest of the world in global competition, challenging hybrid components were included in the programme this time. The parallel session dealt with surface treatments ...
Kunststoffe international, 2007-04-17, Forming and Assembly in One Process
...an be dispensed with in a simple and robust process like assembly injection moulding by radiation cross-linking. Clinching and Crimping in Metal-Plastic Structures Complicated handling and joining processes are eliminated in the case of hybrid structures when the melt pressure is used directly for thermoforming the preheated metallic semi-finished product. The method of crimping and clinching makes it possible for form-fitting to contribute to an increased level of bonding strength. In a model...
Kunststoffe international, 2007-04-17, Tailor-made Matrix Systems for FRPs
...the compression moulding process (Fig.6). Pultrusion has the advantage that the least expensive raw materials, such as glass fibre rovings and polymer granules, can be used. There is thus no need for additional refinement stages, such as hybrid rovings. In addition, impregnation takes place in a continuous, fully-automatic process. Further processing can then be performed "inline" to achieve the final product or an intermediate product, which can then be stored for a virtually unlimited ...
Kunststoffe international, 2007-05-14, An Adventure Park for Injection Moulders
...alities with the production of a rechargeable battery housing in a cycle time of 3s and beakers in 2s. A peripheral innovation for feeding in moist polyester (BMC) was presented on an "Allrounder advance" hybrid machine. This was a screw stuffing unit which facilitates the processing of this glass fibre filled thermoset moulding compound. "Mining" Plastics To illustrate the key importance that machine manufacturers attach to service today, Arburg gave pre-sales and after-sales ...
Kunststoffe international, 2007-06-18, Expertise at the Micro-Level
...stem and is a synonym for micro-technology. In micro-technology, a distinction is now drawn between - micro-structures (e.g. micro-mixers), - micro-moulded articles (e.g. gear wheels), - micro-structured surfaces (e.g. reflective surfaces) and - hybrid micro-structures (e.g. metallised chips for capillary electrophoresis). The most important user industries of micro-technology are the automotive industry, the consumer goods industry, medical technology, telecommunications and industrial process ...
Kunststoffe international, 2007-06-18, Production Technology for High-Wage Countries
...uction-science strategy and theory, together with the technological approaches that this requires. Those participating in the research network (Table 1 on page 19) are looking at different development lines for the individualisation, virtualisation, hybridisation and self-optimisation of production, which will allow organisational and technological innovations to be pushed forward (Fig. 1). Plastics Research The IKV Institute of Plastics Processing has been conducting research into production-...
Kunststoffe international, 2007-08-14, A Route to Cost-effective Photovoltaic Technology
A Route to Cost-effective Photovoltaic Technology Polymer Solar Cells The most recent branch of photovoltaics research involves polymer solar cells based on organic conjugated functional polymers. With semiconductor layer thicknesses around one-thousandth the thickness of a human hair, these polymer solar cells represent the thinnest of all thin-layer technologies. With their comparatively low investment and production costs, they are highly attractive. Steffi Sensfuss et al. Photovoltai...
Kunststoffe international, 2007-08-14, Biggest Growth in Our History
...lastic. On the other hand, extrusion does not offer the flexibility for producing parts in defined lengths or with structure and geometrical elements at right angles to the machine direction. The patented technology was developed by Hybrid Composite Products GmbH together with the consulting engineering company Steiner, both of Spielberg, Austria, with Engel closely supporting the project with its E-Motion all-electric injection molding machine. It allows long profiles with integrated fastening,...
Kunststoffe international, 2007-08-14, Goal: Quicker Return on Investment
....2). An example is the handle made of PA6 Durethan BKV30 Z FN50 for the pipe of a vacuum cleaner from Vorwerk. - Pedal support bracket for the new Mercedes-Benz C-Class based on the plastic/metal composite technology – also called hybrid technology – patented by Lanxess. With Durethan DP BKV 60 EF, the weight of structural components for the automotive industry can be reduced by almost 40% with a loss in mechanical performance (see the article in the September edition). - A highly filled glass f...
Kunststoffe international, 2007-08-14, New Start after Transitional Period
...d to twelve. Up to 2009, Demag will increasingly promote the concentration to three platforms, after which the company intends to focus on worldwide marketing of the all-hydraulic series Systec, the all-electric series IntElect, and the high-speed hybrid EL-Exis S machines. In this context, Dr. Erkes mentioned a slogan-like target: As a manufacturer of high-end, fully modular toggle-operated machines, DPG aims to be the "toggle king in Lego style". In future, there won’t be an own multi-...
Kunststoffe international, 2007-08-14, Preserving and Changing
... Näfels Netstal will be presenting new machines for all three of its business units at the K exhibition. Dr. Thomas Robers, Head of Marketing, Sales and Application Technology, explained the advantages of the new Evos series. This hybrid machine with an electric screw drive has initially been introduced in six sizes, covering a clamp range of 2,000 to 5,000 kN and is intended to replace the models in the SynErgy series over the medium term. All the axes, including the ancillary movements, have ...
Kunststoffe international, 2007-09-19, A Design Tailored to Requirements
...st classical question of “electric or hydraulic” that is the focus of attention but rather the overall drive train-package for all the different machine axles. Virtually all machine manufacturers now have series with all-electro-mechanical or hybrid drive systems in their portfolios. Electro-mechanical Drive Systems The new all-electric creation from Engel Austria GmbH, Schwertberg, Austria, is the E-Max (Fig. 1). This has been designed to offer injection molders who have so far shied away fro...
Kunststoffe international, 2007-09-19, Designing with New Freedoms
Designing with New Freedoms Improved Performance Highly filled polyamide 6 grades are extremely rigid and open up entirely new possibilities for design. All-plastic and plastic-metal hybrid components are not only lighter, more compact and more economical to produce; they are also characterized by improved mechanical performance. In addition, such components can be optimized with regard to weight and performance capability through the use of topological optimization and integrative simulatio...
Kunststoffe international, 2007-09-19, Energy Efficiency Taking on Increasing Importance
...ghts and roof-rail or water-management components. By replacing sheet steel with aluminum, weight savings of 15% were achieved on the front end of the Audi TT when it was produced as a plastic/ aluminum composite for the first time (Fig. 2). This hybrid part is made up of three sheets of aluminum that are encapsulated with Durethan BKV 30 from Lanxess – the polyamide 6 that has become established for hybrid technology. The front end includes a range of functions such as openings for the headlam...
Kunststoffe international, 2007-09-19, Face Lifts for Molded Parts
...continues to gather pace. Batch sizes are shrinking and short setup times are becoming ever more important. Theses demands also apply to pad printing. Tampoprint AG, Korntal-Münchingen, Germany, achieves this with the integrated laser in their Hybrid 90 2-color printing machine which etches the artwork directly into a plastic cliché. The clichés are mounted as a 25m tape in a cassette and during a change of artwork are automatically fed to the printing position and engraved by the laser. Since a...
Kunststoffe international, 2007-09-19, Faster – More Specific – More Efficient
...from innumerable applications. In order to access even more application areas and continuously expand the range of use for plastics, producers and processors of polymers have been developing new materials that employ materials combinations or hybrid materials. But two ever more powerful rivals, time and costs, have been working against such new developments. Growing Demands for Specific Formulations Since the 1990’s, two strategic trends have become dominant in the R&D departments of large pol...
Kunststoffe international, 2007-09-19, For High-End Applications
... PA66 and over 60% lower moisture pick-up help reduce thermomechanical stress on the encapsulated components. Typical applications include speed, pressure and transmission sensors as well as high-voltage cable connectors in electric and hybrid vehicles. The requirements for the electronic consumer goods sector are completely different. Here materials without brominated flame retardants are needed. The answer lies in the halogen-free, flame-retardant, UL94 V0-approved grades Zytel HTN FR52G30NH a...
Kunststoffe international, 2007-09-19, Molded by Air
..., in early stages of development, the developer can use simulations to conduct detailed investigations into the blow molding process and parts properties. At the stand of Uniloy Milacron of Batavia, Ohio, USA, the UMS 16H.S can be viewed, a hybrid machine model capable of producing a 10 liter hollow body with a net weight of 350g at an output of approx. 180 items per hour. Uniloy Milacron claims it could achieve energy savings of up to approx. 22% by switching from hydraulic to electric drives ...
Kunststoffe international, 2007-09-19, Nothing but Bottle Caps
...ns. The caps are demolded by ejectors synchronized to mold opening and, after falling vertically, are carried away by an integrated conveyor belt. Even so-called "cold caps" are always ejected thanks to the high ejection force. Hybrid Machine with Short Cycle Times The hybrid machine equipped with electric screw drive (Fig.4) can perform parallel functions such as plastifying during mold movements. This procedure enables very short cycle times and also contributes to energy efficiency....
Kunststoffe international, 2007-09-19, Technology Barometer Indicates Fair Weather
...el Austria GmbH, Schwertberg, Austria, will be exhibiting a very unusual solution for producing long, profiled plastic parts. In conjunction with an all-electric injection molding machine, the company has refined the process invented and patented by Hybrid Composite Products GmbH and Ingenieurbüro Steiner, both of Spielberg, Austria, and is introducing it under the trade name Exjection. The technique involves a combination of injection molding and extrusion (Fig. 1). A mold insert that creates a...
Kunststoffe international, 2007-09-19, Therefore Test, Who Wants to Bind Himself Forever
...textiles (Fig.2). In addition a shuttle service is provided to transport interested visitors to the pilot plant in nearby Würselen. LPKF Laser & Electronics AG, Erlangen, Germany, is presenting a further development of laser welding in the form of hybrid laser welding. The method combines laser light with infrared raddiation and is primarily suitable for joining large plastic parts. The advantages of this method are demonstrated on the basis of a part drawn from practice, a vehicle light fitting...
Kunststoffe international, 2007-10-21, Complete Control
...n Data Acquisition (PDA) system. In case of deviation, the operator is alerted fully automatically. "At-Line" Rheology The rheometer of the newly patented OCS technology (manufacturer: OCS Optical Control Systems, Witten, Germany) is a hybrid between measurement of granules and extruded films. Highly precise off-line laboratory measurement following ASTM 1283 and ISO 1133 is carried out continuously as well as right "at line" next to the production facility, thus giving the ope...
Kunststoffe international, 2007-10-21, Flexible Where It Matters
...lastic/TPE combinations, - the process combination of multicomponent injection molding and fluid-assisted injection molding for producing two-layer and sequentially composed fluid lines, and - the manufacture of plastic/metal hybrid parts by combination of the processes metal diecasting and plastic injection molding. On November 28 and 29, 2007, the IKV will host a conference on the theme of "Gas- and Water-Assisted Injection Molding Technology – Exploiting Potentials and Overcoming Challeng...
Kunststoffe international, 2007-10-21, Perfect Eyes
...are currently three fundamentally differing concepts available which can be clearly distinguished in terms of certain aspects of their performance, availability and ability to communicate: - Intelligent cameras with an integrated computer, - Hybrid systems or embedded PC systems with the computer located close to the process, - Surface inspection systems with the computer located far from the process. Using an "intelligent line scan camera", data analysis and evaluation take place in the...
Kunststoffe international, 2007-10-21, Polyamides (PA)
... support members at critical points, so enhancing vehicle safety and reducing vehicle weight: In this example, 15kg of polyamide save about 30kg of steel. In terms of weight-saving, Lanxess, is also a leading exponent with its hybrid technology. Recently, it has also been possible to produce hybrid parts with aluminum sheet. Replacement of light metals with plastics is now also complementing steel substitution. For example, to produce the passenger airbag housing in its Q7 model, Audi is relying...
Kunststoffe international, 2007-10-21, Window for the Loading Door
... is more a question of developing complex production lines with robots and integrating other processing technologies, such as processing glass-fiber-reinforced plastics and overmolding a gray cast iron hub (hybrid technology) in the manufacture of washing machine tubs or injection compression molding and multicomponent molding to produce washing machine viewing windows. After a brief pause for thought, Andreas Fried says: "Perhaps it is one of our strengths that we are able to transfer our k...
Kunststoffe international, 2007-11-21, Lighter, More Sustainable, More Economical
...sed by ongoing innovation projects. However, careful analysis of more than 300 newly developed technologies as well as technologies that are being refined further indicates that about only half hold the potential for success. At present, hybrid drives in particular have a good chance of being successful, followed by sequential multi-stage turbochargers, LEDs, intelligent driver-vehicle interfaces and electromechanical brakes. Electronics remains the central "enabler" and driving force be...
Kunststoffe international, 2007-11-21, Lightweight Structures Made of Metal and Fiber-Reinforced Polymers
Lightweight Structures Made of Metal and Fiber-Reinforced Polymers Process Comparison In the production of hybrid compounds made up of metal and a fiber-reinforced polymer, the pre-treatment of the surface has a decisive influence on the quality of the bond. A comparison of induction welding and adhesive bonding shows the bond strength that can be achieved today and permits an assessment for potential fields of application, such as in automotive engineering. Rudi Velthuis, Mark Pascal Kötte...
Kunststoffe international, 2007-11-21, New Boost for Plastic Parts
...laims weight reductions of up to 50 % relative to conventional parts. A backrest with integrated belt as well as a study for a Roadster passenger cell served to demonstrate the method’s potential. Plastic Stabilizes Steel Metal/plastic hybrid structures were showcased by Kirchhoff Automotive GmbH & Co. KG, Iserlohn, Germany. For the first time, the company used plastic to stabilize the hybrid front-end carrier of the current Ford Focus. Development partner was Dynamit Nobel. Since then, Kirchh...
Kunststoffe international, 2007-11-21, Weight-Saving Plastics for Reduced Fuel Consumption
... so that economy is increased in addition to the weight-saving advantages. One prime example for this, which was presented at the IAA by Mann+Hummel, is the plastic oil pan with its high integration potential for car engines. Compared with hybrid components of aluminium and plastic, the all-plastic solution saves about 30% in weight, whilst the advantage can even reach 60% when compared with pure aluminium components. Simply fitting plastic oil pans to all car engines in Germany could result in ...
Kunststoffe international, 2007-12-17, From Miniaturization through to Furniture Design
...ar mirrors, gear system elements, windscreen wiper arms and structural parts for seating components. DuPont is intending to adopt a completely new approach in automotive engineering, among other sectors, with its MetaFuse nanometal/plastic hybrids. This new technology is based on a process in which an extremely robust layer of nanometal is applied to plastic parts. The stiffness of the hybrid is equivalent to that of magnesium and aluminum, and its strength is even higher. This results in a clea...
Kunststoffe international, 2007-12-17, German-Chinese Synergies
...elopment of the Venus model series and already shares responsibility with their German engineers for upgrading HTD to Venus. On the occasion of the K trade show, the holding premiered its new "Haitian Mars Series". With these hybrid machines now available with 16 locking force ranges between 600 and 60,000kN, Haitian closes the gap between their fully hydraulic and fully electric models. A highly dynamic AC servomotor drives a geared pump, thereby achieving energy savings of 20 to 70% co...
Kunststoffe international, 2007-12-17, Hollow Objects
... on a copolyester from Eastman. This container is targeted at the premium packaging market and was being produced in a 2x2-cavity mold on a model BM 406 D blow molding machine. Uniloy Milacron SRL, Magenta, Italy, used the exhibition to introduce a hybrid version of its time-tested Model UMS 16.S blow molding machine. In the UMS 16H.S (Fig. 3), all movements except those of the clamping unit are powered by electric drives. In this way, Uniloy Milacron was able to combine the advantages of conven...
Kunststoffe international, 2007-12-17, Many Improved Details
...rd hydraulic and electric injection molding machines with part-handling robots over the entire range of clamping forces, special processes such as MuCell and gas injection as well as complete systems for producing PET preforms are available. Hybrid Machines for all Applications The trend toward hybrid machines – what is meant here is any electrohydraulic machine with electromechanical screw drive – has expanded into all fields of application. From packaging through automotive applications and ...
Kunststoffe international, 2007-12-17, Marriage between Specialists
...uded semi-finished products, but can have cross-sectional geometries distributed along their lengths and shaped profile ends, which are not feasible with extrusion. The process is the result of a development cooperation by Ingenieurbüro Steiner and Hybrid Composite Products GmbH, both of Spielberg, Austria, and is sponsored by the Austrian Research Promotion Association (FFG). For demonstration, at the Engel Austria GmbH booth, an almost 1-meter strip of ABS with a Y cross-section (Fig.1) was in...
Additional information about this tradename, like producer contact address, etc. can be found at www.materialdatacenter.com. For access to this extra information a registration is requested. Free online registration is available.
Note: the information in Material Data Center was collected with maximum care, based on information from material producers. They are subject to short term changes at the market. There is no warranty for the correctness of this information. In no way this information can be seen as a legal advice, whether certain tradenames are protected or not.