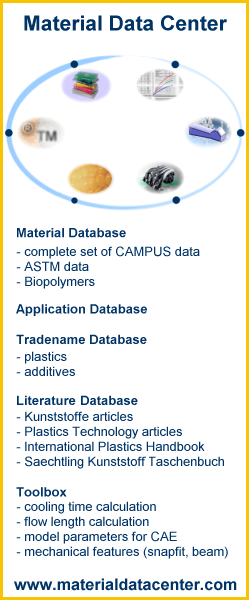
Material datasheets available free. Online registration at: www.materialdatacenter.com
Powder - PA11 - Arkema
Material Data Center is a leading international information system for the plastics industry. Material Data Center offers a comprehensive plastics database, calculation tools, CAE interfaces, a literature database and an application database. For more information about Material Data Center visit www.materialdatacenter.com.
A search for "Powder" in Material Data Center leads to the following information:
|
|
Material Data Center offers information about the following products with the requested tradename. To view a datasheet, please click on the relevant product.
...o aging. These properties must be guaranteed over a wide temperature spectrum [2]. The original compound [3] for the production of the plastic roofing membranes is a rubber-bitumen mixture, which is conventionally produced on the basis of rubber powder from ethylene-propylene-diene rubber (EPDM) as the main raw material in a discontinuous process with internal punch kneaders. However, this type of machine has some disadvantages. For the compounding process only powdery basic raw materials can be...
Kunststoffe international, Excellent Resistance at Reduced Weight
...ng cannot be usefully transferred to thermoset processing. In contrast, thermosets can be chemically foamed because no major modification of the plant engineering is required. The chemical blowing agent is mixed as a powder with the thermoset molding compound and fed into the injection molding machine. During injection into the hot mold, the reaction temperature of the blowing agent is reached and it is released, forming a foam structure. This is fixed by the parallel crosslinking reaction (Fig....
Kunststoffe international, Foamed and Still Extruded in One Step
...imulation GmbH, Dortmund, Germany, which could be confirmed in first test runs on the actual extruder (Fig. 5). A typical window profile formulation of PVC powder and different ‧additives, such as thermal and light stabilizers, lubricants, acrylic impact mod‧ifiers and fillers, was used. Problems with the Die Both the PVC outer layer and the PS foam could be very easily extruded in the first tests in separate operations. However, since the die heated up to about 190 °C in the coextrusion proces...
Kunststoffe international, Green Shape Changers
...e used, as well as a partially biobased thermoplastic polyurethane (TPU), a partially biobased polyamide 6.10 (PA610), and a polyketone (PK) based on the greenhouse gas carbon monoxide. The swellable fillers trialed were wood flour, cellulose powder, and a natural sodium bentonite. Filaments with a diameter of 1.75 mm were extruded on a laboratory extruder from Collin in Maitenbeth, Germany. To ‧ensure optimum processing on standard commercially available filament printers, the maximum diameter...
Kunststoffe international, Medical Applications of Additive ‧Manufacturing
... and product manufacturing will take place closer to the customers. Reducing logistic overhead contributes to achieving climate goals. Classic material groups include metal, ceramics, and plastics. For the metals and the LaserCusing procedure, a powder bed-based metal laser melting process developed by me (market share approx. 80 % of all metal AM systems worldwide), very early adoption for medical applications was possible because we were always able to use certified original materials in powd...
Kunststoffe international, Polymer Materials
...ncludes deliberately manufactured small plastics particles for specific products such as cosmetics, polymer abrasives, laser sintering powder for 3D printing and semi-finished product powder. Type B microplastics originate through usage or abrasion processes, e. g. abrasion of rubber tires (highest share of 81 %), textile fiber fragments released during laundering of textiles, weathering of colorants and paints and agricultural plastics such as films. Deposition and layering of these microplasti...
Kunststoffe international, Rattle-Free Part
...lus’ big brother in turn removes the fully assembled subassembly and places it on a conveyor belt. This is now ejected from the system and subsequently finished to customer specifications, for example with a wood decor or powder enamel coating. “In this way, around 1.6 million of these products will be produced for the automotive industry over the course of the project,” emphasizes Dan Saari. He confidently adds: “We are ideally positioned to meet the demanding requirements of the automotive in...
Kunststoffe international, Sanitary Prototypes with High Requirements
...e SLS systems proved to be impractical for the project due to their complex material change processes: “On the Sintratec S1, which has a small printing area, I can immediately carry out a test print with relatively little powder,” continues Hugo Arnold. So, printing small individual parts on large-scale SLS systems is impractical. 3D Printing Has Largely Replaced ‧Conventional Methods That SLS systems like the Sintratec S1 create competitive advantages is also confirmed by Roger Baggenstos, who ...
Kunststoffe international, 2005-11-21, A Short Time-To-Market Process
...sint M 250 Xtended is becoming increasingly popular. It is the only commercial system in the world for direct laser sintering of mould inserts (Fig. 2) for injection moulding and vulcanisation as well as for prototyping using steel or other metallic powders. The well-known automobile supplier Mannesmann VDO Automotive, Villingen-Schwenningen, was convinced by the efficiency of the direct tooling system. In a first project, which the enterprise carried out in co-operation with the RP service ente...
Kunststoffe international, 2005-11-21, A Wider Area of Application: Compounders and Pelletisers
...through to the new compact Ultima Continous Mixer, were featured in [2]. Large Plants: Higher Outputs and Variable-speed Drive The plastics processing industry uses large compounders to produce process-ready pellets from the raw polymer (often in powder form) and additives. Because of the unrelenting pressure on costs, the capacity of single-strand units for polyethylene (polypropylene) has increased from about 320kt/a (210kt/a) in 1995 [3] to around 600kt/a (450kt/a) today. Further capacity ...
Kunststoffe international, 2005-11-21, Additives: Custom-engineered Plastics
...e the cable properties to a great extent. Following the trend to lead-free stabilisers, Chemson offers calcium-zinc- and magnesium-aluminium-zinc-based systems under the tradename Naftosafe. By offering material in various forms such as powder, tablet, flake, micropellet, pellet and stabiliser blends, the company is addressing the varying requirement profiles of processors. Baerlocher has also introduced dust-free product forms for solid CaZn stabilisers and can now offer the PVC industry CaZn s...
Kunststoffe international, 2005-11-21, Adhesives: What Do Adhesives Accomplish in Practical Processes?
...#34;. This involves manufacturing the prepreg, generally as a natural fibre polypropylene hybrid mat, and turning it into the finished component by compression moulding. Additives like bonding agents can be incorporated into the composite by the powder technology, which involves sprinkling them onto the substrate as it passes underneath (Fig. 2). A more elegant bonding method involves spinning fibres with the adhesive already incorporated. This dispenses with metering and handling problems for ...
Kunststoffe international, 2005-11-21, CAD/FEA Integration: Water Pump with Improved Long-term Performance
...s on account of their good dimensional stability. Because of their low density and negligible flammability, they are also often employed in other electronic and electrical applications. Vyncolit supplies the base material for the phenolic resin as a powder, which is then further processed by the customer or a sub-contractor. Since the moulding processes for phenolic resin differ from those for metal and thermoplastics, Vyncolit frequently provides consulting services. Analysis with CAD Systems ...
Kunststoffe international, 2005-11-21, Calcium Silicate as a Functional Filler: Wollastonite – a High-performance Filler
...rformance Filler Calcium Silicate as a Functional Filler. It is only in the last 30 years that the plastics industry has discovered the mineral, wollastonite, which was previously used mainly in the ceramics industry. The more refined wollastonite powders have gained considerably increased importance as reinforcing materials for plastics. Bettina Nolte-Ernsting For a long time now, fillers have ceased to be a simple means of extending plastics compounds to reduce the cost and now play a very ke...
Kunststoffe international, 2005-11-21, Carbon Nanotubes
...oss two graphite electrodes in an inert atmosphere to produce an arc between them. In this arc, the carbon atoms form the MWNTs, which are found as a deposit on the cathode. SWNT is made by filling a catalyst (nickel, yttrium), mixed with graphite powder, into a drill-hole in the anode (Fig. 3). The yield of MWNT in this process is roughly 30 %, the rest being so-called turbostratic graphite and amorphous carbon. A higher yield may be obtained with catalytic processes. The disadvantage of these ...
Kunststoffe international, 2005-11-21, Centralized Supply for 59 Injection Moulding Machines
...ying modules, whose volumes range between 100 l and 400 l. These drying modules, including the insulation are rectangular in form and equipped with individually adjustable heating and automatic air control (ALAV). The surface of the drying module is powder coated, the side walls and the conical part are made of stainless steel. The large cleaning door with integrated viewing glass allows easy cleaning of the module. The hoppers, pipelines and switch cabinet are integrated into one console. The m...
Kunststoffe international, 2005-11-21, Ceramic Injection Moulding in Practice
... items per unit time, is superior to all other ceramic forming processes [2, 3]. Production Boundary Conditions As raw material a zirconium oxide injection moulding mass from Inmatec GmbH, Rheinbach, is used. Here a mixture of a zirconium oxide powder and a special plastic mixture called a binder for plasticising the ceramic powder is used [4]. Zirconium oxide is the material of which ferrules are usually made. For production of the blanks an injection moulding machine (manufacturer: Arburg; g...
Kunststoffe international, 2005-11-21, Colourfast Window Profiles
...ng conditions, weld factors of 0.9 to 0.95 can be attained with styrene copolymers. One possible alternative is to use some sort of plug-and-socket connection (inserts). Extrusion lines 70 to 80 % of polyvinyl chloride is processed in the form of powder. As a rule, PVC is therefore processed on counter- rotating, tightly intermeshing twin screw extruders. Twin-screw extruders are noted for their gentle plastication and outstanding compatibility with PVC powder. The relatively complex structure...
Kunststoffe international, 2005-11-21, Combined Process: Foamed Parts with Excellent Surface Quality
...at a blowing agent dissolved in the molten material foams and forms the cell structure as soon as the pressure during injection into the mould falls below the expansion pressure of the blowing agent. Chemical blowing agents in the form of a powder or masterbatch are added to the pellet moulding compound and, as the polymer melts, are broken down to initiate the foaming process. Physical blowing agents are usually added to the melt during plastication or the injection phase [1]. Chemical blowing ...
Kunststoffe international, 2005-11-21, Compounding: The Intelligent Alternative
...of bimodal plastics with a viscosity ratio of significantly above 10, the shear flow does not play a part; only two-dimensional stretching flow is suitable for breaking down high-molecular particles. Consequently, the melting of plastic powder and homogeneous incorporation of the high-molecular component into the low-molecular matrix are process steps that are completely different, even contradictory, from the point of view of the process engineering. Melting preferably requires high shear rates...
Kunststoffe international, 2005-11-21, Compounding: Throughput-determining
...k over the TSK division (Theysohn screw kneaders) from Theysohn Maschinenbau GmbH at the beginning of this year further extended the Braunschweig/Germany competence centre for processing applications of synthetic raw materials, such as plastics, powder paints and rubber coatings. The BTSK-30 presented at K2004 by Bühler TSK Extrusion Systems is the latest extension to the TSK extruder series (Fig.2). As the smallest compounder of the series, designed both for laboratory and production use, it is...
Kunststoffe international, 2005-11-21, Compounds and Blends Made to Measure
... load cases, at Lehmann & Voss each tribological system is adjusted individually to the application. Here the compounds used are based on high molecular weight polymers with admixtures of PTFE, UHMPF, silicones, graphite, molybdenum alloys, bronze powders and aramid, carbon, glass and mineral fibres. In this way the friction values, the wear characteristics and the intake behaviour of the material combinations can be adjusted over a wide range. Tailoring Additives and Compounding Materials Dif...
Kunststoffe international, 2005-11-21, Compounds and Masterbatches
...ers, compounders and masterbatch producers are found to be much more complex. For example, many compounders are also masterbatch producers, and polymer producers are also compounders. Compounders typically produce their compounds by the addition of powdery additives, but masterbatches are also widely used to obtain the desired colours. Polymer manufacturers are thus suppliers for the masterbatch manufacturers and can also be their customers for masterbatches for colouring compounds. Compounders ...
Kunststoffe international, 2005-11-21, Compression Moulding of Long-fibre-reinforced Plastics
...are also stored. The operator has no influence on the weighing process. Because of the different product consistencies handled, the weighing unit is divided into two sections: - bulk liquid components such as resins and thermoplastic solutions and - powder substances such as fillers. Before the finished paste batches are passed to the SMC plant for processing, their properties such as viscosity, color and reactivity are tested. The technology of a modern SMC production plant has reached a high s...
Kunststoffe international, 2005-11-21, Cosmetics Packaging: Trend towards Transparency
...rlyn to combine the chemical inertness of the former with the design freedom of the latter. Where only a combination of chemical inertness and break resistance is needed, this polymer can also be used in transparent or pigmented form to powder-coat glass. A new development from DuPont in the area of coextrusion blow moulding is that of thick-wall technology, a patent for which has been applied for. Together with its partner Crown Raku, Rastatt/Germany, DuPont uses Surlyn to cost-efficiently achi...
Kunststoffe international, 2005-11-21, Dashboards Meet Highest Requirements
...he USA, e. g. by DaimlerChrysler (title picture; source DaimlerChrysler). This material is being tested worldwide for many new car models at present being developed. In slush moulding, a closed mould rotates around several axes and the material in powder form melts on the hot mould surface and fuses together. After the cooling phase, a three-dimensional skin is formed with very uniform wall thickness, irrespective of the design complexity of the component. In this way, wall thickness can be defi...
Kunststoffe international, 2005-11-21, Decorative Surfaces in the Automotive Interior
...pends on a number of factors. The automotive industry's efforts to eliminate the inexpensive, but environmentally harmful PVC from the automotive interior has opened an opportunity for alternative materials. Polyurethane mould skins, such as the powder slush skin of aliphatic TPU come into their own here. The PU all-rounder meets the most stringent demands for technology, safety and aesthetics - even in highly integrated cockpit solutions. Polyurethane slush skins have high ageing resistance...
Kunststoffe international, 2005-11-21, Desktop Manufacturing and Biofunctional Processing
...hich is marketed by Z-Corporation, Burlington, MA/USA, for concept model making, and commercialised for biotechnology applications by Therics Corporation, Princeton/USA. It involves the layer-by-layer construction through solidification of applied powder layers by printing of binders by means of ink jet technology. The ink activates an adhesive in the powder that provides the strength when dry. Very often, post treatment is required, e. g. to crosslink the water-soluble polymers. The diameter of...
Kunststoffe international, 2005-11-21, Direct Colouring: Producing Colour Masterbatches Economically
... between 20 to 30%, and only in exceptional cases are concentrations up to the maximally dispersable pigment concentration needed. The Conventional Production of Masterbatches The major part of colour masterbatches is still produced directly with powdery pigments. The pigments needed for an individual colour are intensively mixed with powder plastic using dispersion aids, e.g. waxes, and then dispersed in twin-screw extruders with high energy input and thus embedded in the plastic. Since dispe...
Kunststoffe international, 2005-11-21, Direct Laser Forming: New Structures Built up Layer by Layer
...e already well established in the plastics industry for the series production of components. In the metal sector, however, the use of these processes, e.g. for making injection moulds, is still new and extremely promising. In a similar way to other powder-based generative processes, laser forming makes it possible to build up components with complex geometry layer by layer directly from a 3D CAD model. But unlike processes such as laser sintering, direct laser forming uses only pure metal powde...
Kunststoffe international, 2005-11-21, Economic Compounding: Nanocomposites
...um oxides (Fig.1 left). A chemical pretreatment, in which the sodium ions are replaced by long-chain, organic ions, increases the layer spacing from around 1nm to 1.8 to 3.8nm (Fig.1 right). These so-called nanoclays are then in the form of a bulky powder with particle sizes from about 8 to 40µm; each particle contains several hundred to several thousand layers. Basic Principles of Compounding Nanoclays In compounding nanoclays to produce nanocomposites, two processes have to take place (Fig.2...
Kunststoffe international, 2005-11-21, Economic PVC Pelletisation
...ility and place importance on processing the widest spectrum of materials with maximum quality. This can be achieved with carefully matched processing units, allowing full control over the process. PVC pellets are easier to store and transport than powder dry blends. They absorb much less moisture on storage. Their feed behaviour to the extruder is much better, and higher throughputs are achieved. Dust-free processing is critical in cases where it is essential to keep a tight control over cleanl...
Kunststoffe international, 2005-11-21, Efficiency Comparison: Microspheres – a Universal, Effective Blowing Agent
... soles (see title photo). Other fields of application include the extrusion of sawdust-filled thermoplastics, power cables and carpet backings. Thermoplastics and TPEs in General The microspheres (Fig.1), which are supplied in the form of a fine powder or as a masterbatch blended with EVA, are suitable generally for most thermoplastics and thermoplastic elastomers (TPE), as long as their processing temperature lies between 130°C and 210°C. The grades in the Expancel range are geared to differe...
Kunststoffe international, 2005-11-21, Electrical Component Parts: Thermal Metal Spraying of Conductor Lines on Plastic
...er substrates also. Thus at present in addition to technical plastics also materials such as paper, wood, stone or ceramic can be coated (Fig.2). For structuring of plastic the most varied procedures in the range of sandblasting, gluing on metallic powder, thermal fixation of metallic powders (so-called nucleation layers) or even previous thermal injection are being investigated. It is decisive that no process-determined mask is needed. Sprayed metal layers and/or line thicknesses greater than 2...
Kunststoffe international, 2005-11-21, Electronic Components and Displays: Intrinsically Conductive Polymers
...itor is described in Fig. 2: the process can be divided into the steps of anode production, anodic oxidation, polymer impregnation, contact creation and encapsulation. To produce the tantalum anode, tantalum powder is pressed and then sintered to form a fractal structure with a large internal surface area. Through anodic oxidation, a 10 to 100 nm thin tantalum oxide layer is created that serves as the dielectric medium. Manganese dioxide is produced as the opposing contact through impregnation a...
Kunststoffe international, 2005-11-21, Engineering Plastics: Products for Innovative Processes
...w production line in 2005. By designing this “White Room” facility, the requirements of GMP (Good Manufacturing Practice) have been taken into account. A good example of an innovative application in medical technology is the SkyeHalerTM dry powder inhaler produced by the Swiss company Skye Pharma AG (Fig.4). The main target market for Hostaform MR130ACS (manufacturer: Ticona) is the fluid handling and electrical household appliances industry. This newly developed Hostaform grade is resistant to...
Kunststoffe international, 2005-11-21, Epoxy Resins (EP)
...ties. As the electronics industry advances, developments in new epoxy products will ensure that they remain the material of choice for these applications. Another growing market today for epoxies is performance coatings like can, marine, industrial, powder and photocure coatings. Epoxy-based powder coatings are used in many different applications, including metal parts, automotive, appliances, furniture and many others. Formulators turn to powder coating resins for a variety of performance advan...
Kunststoffe international, 2005-11-21, Escalators Made of Plastics
...tage for customers and operators is the greater use of colour in the design of the steps and hence the possibility of consistently implementing the corporate design right through to the escalator steps. Coloured aluminum steps are either painted or powder-coated and lose their intended effect when the colour wears off. With the plastic step, by contrast, the moulding compound itself is already coloured throughout, making it resistant to scratches. Even the unavoidable wear due to abrasion on the...
Kunststoffe international, 2005-11-21, Europe is the Largest Market: Polyaryletherketones (PAEK)
...ns involving less than 30 days blood contact. This new PEEK fills a gap between the PEEK-Optima grades for long-term implants and the Victrex PEEK engineering grades Strategic Market Development and New Applications For coating purposes, a fine-powder PEEK has been developed, which can be purchased as a ready-to-use dispersion from Victrex’s development and marketing partners STE Ges. f. Dichtungstechnik mbH and Ilag Industrielacke in Europe, Tech Line Coatings Inc. in the USA and Okitsumo Inc...
Kunststoffe international, 2005-11-21, Evolution, Not Revolution
...er parts quality combined with 30 % higher productivity relative to older systems. The new software improves build chamber utilisation by arranging the prototypes spatially. This "stacking" in the build chamber is facilitated by using the powder bed for support during laser sintering. The quality of laser-sintered parts is now so good that they can serve as master patterns for vacuum casting. Stereolithography prototypes are unbeatable when it comes to reproducing the finest of structure...
Kunststoffe international, 2005-11-21, Exhibition Preview: North American and Canadian Products at K 2004
...55 and 65 Shore A, respectively. The Versollan RU series exhibits strong chemical adhesion to PC, PC/ABS, and ABS, and offers faster cycles than straight TPU. DuPont is developing novel modified powder forms of its Hytrel copolyester TPE for slush molding of auto dashboard covers to replace PVC. The soft Hytrel skin would be backed by a Hytrel foam layer and mounted on a rigid support of Crastin PBT--thereby creating the first all-polyester dashboard structure, which could be recycled without se...
Kunststoffe international, 2005-11-21, Expandable Thermoplastic Polyurethanes: On Light Soles
...an excessively high level of shear due to an incorrect mould layout. Blowing Agents and Colours The used blowing agent consists of a masterbatch in form of granules. This means that the dust encountered with conventional TPU blowing agent systems (powdered blowing agent) can be avoided right from the start. This permits clean conditions from the industrial hygiene angle plus easy handling of the components and, above all, it prevents the formation of powder agglomerates and deposits in the proc...
Kunststoffe international, 2005-11-21, Filled PU: Solid Metering for Reactive PU Systems
...larly important for special applications. Metering Solid The mixing head for the direct metering of solids into the mixing chamber is based on Desma’s original low-pressure mixing system – enhanced with a radial conveying screw for feeding powder or pellet stock (Fig.3). The solid is fed to the screw in a dry state and then passes to the plane of the valves, where it is mixed with the components and pigments. In contrast to premixing of pulverised solids in the component tanks, this technology ...
Kunststoffe international, 2005-11-21, Fillers: Improved Properties and Processing
Trade Fair Report Improved Properties and Processing Fillers. The trend that was obvious during the past decade continued at this year’s K-Show. The consequences of the increased price of energy, especially oil, together with developments regarding the exchange rate of the U.S. dollar, have had a significant effect on all materials, but especially the filler industry because of the very high freight costs in relation to the value of the product. Increasing transportation costs, in particular, pr...
Kunststoffe international, 2005-11-21, Film Extrusion: PET Extrusion without Pre-drying?
... of below 50ppm. The granules should subsequently be conveyed to the extruder using dry air, because hot dry granules have a tendency to absorb water very fast. Relevant literature puts the figure as high as 3–8ppm/min (granules) and 40ppm/min (powder), depending on the geometry of the bulk material [2-4]. Dispensing with the Pre-drying The degassing technology is a real alternative to pre-drying or at least a sensible addition to it. We must distinguish in this context above all between the h...
Kunststoffe international, 2005-11-21, Flat-film Extrusion Lines
...ounding and extrusion in one economic operation known as direct extrusion [7]. These twin-screw extruders meet the specific market requirements for direct extrusion: - good feed of poor-flowing raw materials, - problem-free conveying of slow-flowing powder materials, sticky compounds and fibrous additives, - high, surge-free output, - excellent dispersing and homogenizing action for consistently good product quality, - precise melt temperature control and monitoring, - efficient single- and mult...
Kunststoffe international, 2005-11-21, Focus on Injection Moulding Technology
...s, the so-called Lattice technology. For this reason, the company is able to give one year's full guarantee against abrasion, corrosion and breakage on all return-flow valves. The screws, on the other hand, are protected against wear and tear by powder coating using the flame spraying method. The increasing quantities of filled plastics being processed have made these developments necessary, says Dr. Urbanek, the Technical Managing Director. This special treatment has brought a doubling of a...
Kunststoffe international, 2005-11-21, From Operating Point to Operating Window
...iscosity is to be manufactured, for instance a very fluid product with an MFI (2.16 kg) of 40 g/10 min, the ZSK MEGAcompounder must homogenise and melt the product at a higher speed. The intensive mixing is necessary to avoid aggregates of unmelted powder. During subsequent processing, for instance injection moulding or blow moulding, they would lead to defects in the parts produced. For such a product the throughput is limited by the maximum attainable screw speed, as shown in Fig. 7. A ZSK MEG...
Kunststoffe international, 2005-11-21, Functionality is the Key Factor
...regular taking of medication, has led to numerous sophisticated solutions involving the use of plastics. Plastics technology can provide important assistance in enabling the patient to keep to the prescribed dosages in self-medication. Intelligent powder dosage systems are one of the results developed as an alternative to propellant gas systems. The functionality of such systems is being increasingly adapted to suit the needs of the patient. The advantages of simple handling - which are graduall...
Kunststoffe international, 2005-11-21, Gear Lever in Hand
...e shift rod during gear lever handle assembly. Due to the high ductility of the long-glass-fibre reinforced PP leather can be attached to a framework made of this material thus providing reliable fixation of the leather cuff. In contrast, a talcum powder reinforced PP used previously was inclined to tear. The soft SEBS component of the 2-component composite has advantages compared to the substituted polyurethane such as: - small manufacturing tolerances for the ShoreA hardness scale, - desired m...
Kunststoffe international, 2005-11-21, General-purpose Plastics: Appearance Ever More Important
... mechanical properties of the original metallocene grades with the straightforward processing of standard Ziegler-Natta grades. It is the special metallocene catalyst technology that constitutes the key here. mPE M 3581 UV (pellets) and M 3583 UV (powder) can be sintered more rapidly and then compacted at a higher speed. Bubbles can be removed more efficiently. Additional advantages include excellent dimensional properties, superior impact strength at low temperatures, resistance to chemicals, o...
Kunststoffe international, 2005-11-21, Grooved Feed Sections
...ion designs vary in the number of grooves and the geometrical design of the grooves, which depend, in particular, on the polymer processed and its feeding characteristics. For pelletized polymers, grooves with a rectangular section are used, whereas powders or very small pellets require semi-circular grooves. Triangular or trapezoidal grooves are also possible. The groove depth may be constant or variable in the longitudinal direction (Fig. 1). The groove geometry must be chosen to suit the part...
Kunststoffe international, 2005-11-21, Growth in Rotational Processing: Innovations Rewarded
...urther Technical Development Today rotational technology has technical possibilities that are unique and support the positive trend. Thus at present, and only with rotational technology, it is already possible to treat the raw material (powder) using a plasma modification in such a way that products made of it have certain surface tension and adhesion characteristics. Thus they are suitable for subsequent value added procedures (e.g. lacquer finish or other coating, adhesion to other materials ...
Kunststoffe international, 2005-11-21, Growth Market for Powder Injection Moulding
Growth Market for Powder Injection Moulding Opportunities for Processors Frank Petzoldt, Bremen/Germany The injection moulding of metal and ceramic powder materials (powder injection moulding - PIM) has become established as a competitive technology for precision parts. PIM's success results from the high freedom of shaping allowed by plastics injection moulding technology combined with the wide choice of materials offered by powder technology. This leads to a dynamically growing marke...
Kunststoffe international, 2005-11-21, Headlamp Bonding: Warm Reactive Bonding
...over shield and a body (Fig.1). The cover shield is usually a polycarbonate (PC), which is protected from scratches by a hard layer, e.g. by a UV hardening system. The body is generally polypropylene (PP), which modified with fillers such as talcum powder can have a high scratch resistance. Also polybutylene terephthalate (PBT) or PC are used for production of headlamps. Current Status of the Technology Sealing materials or adhesives have been used for a long time in the production of headlamp...
Kunststoffe international, 2005-11-21, High Growth Rates: Polyphenylene Sulphide (PPS)
...ermoplastic, semi-crystalline polymer produced from dichlorobenzene and a sulphur source. A distinction is made between crosslinked PPS and linear PPS. With both the crosslinked and the linear PPS grades, the synthesis process results in products in powder form. The technology for producing crosslinked PPS was developed in 1953. The linear PPS process is based on the same technology but results in products with improved technical performance. Both products are semi-crystalline and have a meltin...
Kunststoffe international, 2005-11-21, High Throughput and Flexible Systems
...cerned. These developments toward higher outputs and multimodal polymers obviously present no difficulties to the relevant domestic and foreign machine manufacturers. Krupp Werner & Pfleiderer GmbH, Stuttgart/Germany, has several ZSK 280 and 320 for powders and melts and Berstorff GmbH, Hannover/Germany, has an order for a KE 800 for melts. Compounder Installations Increasingly more flexibility is required in compounding. Short change over times for formulation and colour changes with simultan...
Kunststoffe international, 2005-11-21, High-Grade Design
...emperatures of around 170°C [8]. A filled acrylic resin with antibacterial properties is available for sanitary applications in hospitals [8]. Silver salt added to the resin is released on a continuous basis as the resin is cleaned with scouring powder, preventing the growth of widespread bacteria and providing considerable support for disinfection routines in hospitals. To produce the appropriate fittings for hospitals, conventional and antibacterial panels and mouldings are used in combina...
Kunststoffe international, 2005-11-21, High-output Compounding
...amily of Buss Kneaders exhibited for the first time at K2001, is another milestone in this ongoing development. The quantec (Fig.1) is specially designed for compounding shear- and temperature-sensitive products such as rigid and plasticised PVC and powder coatings. The aim in developing quantec was to significantly increase the profitability of the plant operation by at least doubling specific output and cutting installation costs at site. In developing the quantec, it was important to fully re...
Kunststoffe international, 2005-11-21, High-performance Plastics: The Right Material for Future Markets
...y technically interesting niche markets (source: VKE, AA Statistik und Marktforschung) Share of the global market Fig.4. Survey of the share of individual high-performance plastics in the global market in 2003 (based on powder and compounds, including fillers and contents in blends; in the case of PTFE, including solids contents in dispersions; author's estimates) Regional consumption Fig.5. The regional differences that still exist in the consumption pattern of high-performance plastics t...
Kunststoffe international, 2005-11-21, Higher Value Added
...gerwerk Lack- u. Farbenfabrik GmbH & Co. KG, Wels, was founded in 1934. The production program includes lacquers and paints for interior and outdoor applications. A crucial step was taken into a trend-setting technology with the production of Drylac powder coatings. The Tiger Color Batch business was founded in 1976. These masterbatches are used in the plastics processing industry to colour thermoplastics.
Kunststoffe international, 2005-11-21, Highly Filled, Well Dispersed
...ents to re-agglomerate also leads to problems from time to time in a pure polymer melt. Depending on the pigment, different carrier systems have proved satisfactory. The basis of a pigment concentrate can be a polymer, a wax or a mixture of the two. Powder-form pigment concentrates are also available. For example, free-running, dust-free powder pigment concentrates are in demand for colouring plastic powders during processing. They can also offer concentrate manufacturers a simple, manageable in...
Kunststoffe international, 2005-11-21, House Shows: Show of Expertise at Coperion
...n conveying properties. Blow-through Rotary Valves with 40% Higher Capacity For the continuous feeding of bulk goods into pneumatic conveyor units, rotary valves are needed. They pass the material under pressure to the conveyor line. For powders, blow-through rotary valves are generally used, in which the conveying air for product transport flows parallel to the rotary valve axle, directly through the lower chambers of the rotor. This results in a forced discharge, which also ensures that the ...
Kunststoffe international, 2005-11-21, Ideal for Laboratory and Production
...er masterbatches or compounds. Quick stock availability, high product quality and market prices - optimal combination of these three factors is a key to success for among others manufacturers of masterbatches, compounds of engineering plastics or powder coatings. The compounder is the determining factor, usually a twin-screw extruder. The machines must be suitable for a wide variety of uses, particularly the smaller units with screw diameters between 25 and 70 mm. They begin with production of...
Kunststoffe international, 2005-11-21, Improved Efficiency and Quality
...sible specific throughput for a particular dry blend. In general, with high-performance profile extrusion, only one formulation (normally dry blend) is processed, and the machines operate in a narrow performance range. In all cases in which not only powder but also pellets or regrind is to be processed, it is necessary to use a feed unit. It is notable that the proportion of gravimetric feed systems is increasing steadily. This is because of the ever-tighter dimensional tolerances of the profile...
Kunststoffe international, 2005-11-21, Increased Demand: Polyoxymethylene (Polyacetals, POM)
... bring a new production line on stream from 2005 ("white room”), in which the requirement of GMP (Good Manufacturing Practice) have been taken into account. An example of an innovative application in medical technology is the dry powder inhaler SkyeHaler TM from Sky Pharma AG of Switzerland. The POM used is a high-quality crystalline acetal copolymer with a linear structure. It offers impressive frictional, sliding and wear properties, hydrolysis and chemical resistance and durability. In s...
Kunststoffe international, 2005-11-21, Injection Moulding Ceramic Powder
Injection Moulding Ceramic Powder Requirements and Prerequisites for Plastics Processors Wolfgang Kollenberg, Moritz von Witzleben, Rheinbach/Germany Ceramic injection moulding procedures are particularly suitable for implementing complex part geometries. The authors describe principles and refinements of the procedure for potential users in their contribution. Ceramic materials constantly gain in importance due to their unique characteristics. Ceramic materials are used in all kinds of ...
Kunststoffe international, 2005-11-21, Injection Moulding Metal and Ceramic Powder
Injection Moulding Metal and Ceramic Powder PIM is Not a Job Just for Specialists Michael Bayer, Gersthofen/Germany Despite the many advantages that injection moulding of plastics offers, limits are set by the material properties. Powder injection moulding permits the combination of a thermoplastic moulding process with ceramic or metal materials. In this article, the smooth integration of powder injection moulding into a plastics injection moulding plant is described. Thermoplastic moul...
Kunststoffe international, 2005-11-21, Injection Moulding Operation: Tailor-made Materials Supply
...As a result, energy consumption can be reduced and substantial savings made on costs. The nine square-shaped Somos drying hoppers (Fig.3), each of which holds 400 litres, are insulated and have their own heaters. The surface of the drying module is powder-coated, the side walls are made of high-grade steel and the conical section is made of GRP. It features a large cleaning door with integrated window for easy cleaning. Hopper and pipelines are integrated as a compact unit in one console. The i...
Kunststoffe international, 2005-11-21, Injection Moulding Trends: Increased Complexity and Tighter Specifications
...ion moulding where the subsequent assembly steps are dispensed with by having this stage performed inside the mould too. Further promising fields of application for the future are not only multi-component injection moulding but also powder injection moulding, and the processing of liquid silicone rubber (LSR), elastomers, thermosets and PET, and the gas techniques. New applications will also emerge for non-plastics, such as wood or natural fibres. There will be considerably fewer market developm...
Kunststoffe international, 2005-11-21, Injection Moulds Direct by Laser
...ading manufacturer of rapid prototyping systems offers a process in DMLS (direct metal laser sintering) and its rapid tooling application called DirectTool, that greatly shortens this time. The much-improved surface quality of the new DirectSteel 20 powder leads to substantially shorter finishing and thus to much shorter project lead times. The following examples show by how much the process chain from CAD to injection-moulded parts now can be shortened. The real-life example of a modem housing ...
Kunststoffe international, 2005-11-21, Interior Trim Parts made of Plastic: Common Ground between Automotive Technology and Design
...lden had to enter the current production without a transition. This succeeded through close co-operation with the customer, who made an accelerated release procedure possible locally. The seat covers are injection moulded with PP with 20% talcum powder in five different colours. The material defined by the customer is supplied already dyed. In 1+1 moulds left and right screens are injection moulded in parallel in one cycle. The mould forms the surface texture (etched scar) defined by Audi. A col...
Kunststoffe international, 2005-11-21, Interview with Dr. K. Bourdon: “We Need to Strengthen our Corporate Identity”
Market and Management Ferromatik’s “Innovation World” open day was a huge success, attracting over 1000 professional visitors (see report on page 4). Kunststoffe editor Clemens Doriat met Dr. Karlheinz Bourdon, president of global plastics machinery of Milacron Inc. and interim managing director of Ferromatik Milacron Maschinenbau GmbH, on the fringe of the event in Malterdingen/Germany. “We Need to Strengthen our Corporate Identity” Karlheinz Bourdon on the German/American collaboration, the G...
Kunststoffe international, 2005-11-21, Isocyanate-free Route to Polyurethane
... catalyst addition. The CBC additive (trademark: Allinco, manufacturer: DSM) is setting new standards here. As can be seen from its chemical structure shown in Fig.2, CBC is an activated derivative of carbonic acid. It is supplied either as a white powder by DSM or as a masterbatch by Clariant. CBC melts at 112°C and is non-toxic with an LD50 value >2000mg/kg. With this carbonic acid derivative, it is possible to carry out completely new reactions in addition to the typical reactions of acti...
Kunststoffe international, 2005-11-21, Joining Technologies: Lightweight Hybrid Structures
...ed in the rod end. The thickening of the rod end produced by the spreader is tightly held in the funnel-shaped inner contour of the metal load transfer element. Fibre-reinforced thermoplastic rods can be economically produced by pultrusion from powder-impregnated roving material or blended yarns with a thermoplastic fibre content. The load transfer elements can be efficiently installed with, for example, three pneumatic drives and a heating element. The rod end is heated indirectly by heating th...
Kunststoffe international, 2005-11-21, Large-scale Production: Challenges in Ceramic Injection Moulding
...lems and solutions involved in scaling up the principles for practical industrial production. To illustrate the process chain, the basic elements are listed: - Raw material: compounded, injection-moulding grade ceramic compound comprising ceramic powder (in this case aluminium oxide), binder system (PE based, manufacturer: Clariant) and various additives. - Injection moulding: fully automatic processing of the ceramic compound on a standard injection moulding machine equipped with a hard metal i...
Kunststoffe international, 2005-11-21, Laser Sintering: Complete Freedom of Design
...arket demands must be flexible in their production capabilities. New methods of product development and manufacture are therefore gaining in importance. An example of such an innovative method is laser sintering. A laser melts plastic, metal or sand powder locally, and it immediately solidifies again. In this way, layers are built up one on top of another. The part grows directly out of the CAD data. Almost Unlimited Freedom of Design In comparison to conventional manufacturing methods, laser si...
Kunststoffe international, 2005-11-21, Laser Sintering: For Tools, Looms and Water Cooling
...nely focussed laser beam permits high detail resolution of the part, while the high absorption of the laser wavelength, together with the variable laser focus increases both the building speed and system productivity. The handling of the machine and powder have also been simplified. The system also has a gastight process chamber that ensures very high purity of the process chamber. The system consequently offers an ideal platform for future material and process developments. The manufacturer als...
Kunststoffe international, 2005-11-21, Laser Welding A Mature Joining Technique
...ed that, even for the "laser-transparent" component, up to 50 % of glassfibres or glass beads will not cause the laser radiation to be scattered or absorbed too extensively. Mineral fillers are more problematic; plastics filled with talcum powder or "Wollastonite" mineral fibre are not transparent enough to allow laser radiation to generate a good welded joint. This proved to be precisely the case when several colour pigments were examined. For example, it has not been possible s...
Kunststoffe international, 2005-11-21, Laser-sintering Technology: Series Production in Miniature
...earing aid, or a withdrawal thread and an unambiguous ID code. The geometrical data obtained in this way then form the basis for steering the laser-sintering unit. Laser-sintering is a dry process in which CO2 lasers build up a work piece from powdered polyamide on a layer-by-layer basis. The process is a very rapid one, taking just a few hours, depending on the geometry, size and number of parts. The rule here is: the more filigree and complex the desired shape, the higher the productivity – a ...
Kunststoffe international, 2005-11-21, Lignin - Tailor-made
...ch/Germany. The materials marketed under the name Arboform contain up to 50 % natural fibres and are based on a thermoplastic lignin matrix. Unlike these finished lignin compounds, pure lignin can be bought from Granit SA in the form of a brown powder. Depending on the type of lignin, which is usually determined by its plant origin, the melting point of lignin can vary (150 to 180°C) and therefore the viscosity behaviour of the compound produced from it. With increasing lignin content (up to...
Kunststoffe international, 2005-11-21, Lotus-Effect – Now and in the Future
...erwerke (see www.lotus-effect.com). The spectrum of developments ranges from roof tiles through exterior house paints, plastics products, wood varnishes, paint raw materials, glass and metal, textiles and car polishes to paper and powder coatings with lotus-effect. And the number of free-riders has now unfortunately reached three digit figures. Self-cleaning Plastics Surfaces Let us now focus our attention on the plastics sector. Degussa AG, through its Creavis Technologies & Innovation Divisi...
Kunststoffe international, 2005-11-21, Market for GRP and Thermosets
...stellung = Sheet manufacture; Wickeln = Filament winding; Schleudern = Centrifugal casting; Pultrudieren = Pultrusion; Sonstiges = Other Fig. 2. The European thermosets market during the period 1998 to 2000 Verbrauch = Consumption; UP-trocken = UP powder; Sonstige = Other Fig. 3. The expert forum organised by the Kunststoffe editorial office attracted considerable visitor interest at Materialica Plastics Composites World Properties such as light weight combined with higher abrasion resistan...
Kunststoffe international, 2005-11-21, Material in Movement
...s; the bulk material has a fluid flow behaviour and tends to shoot. With coarse particles, high gas flows are required to form the fluidized bed. With compressed tables that are smaller than 5 µm, individual large flow channels form before the powder is fluidized. Moist, sticky, abrasive, fragile and/or in particular non-isometrically shaped particles have other unfavourable properties that necessitate special treatment. The points discussed above make it clear that a knowledge of the part...
Kunststoffe international, 2005-11-21, Material supply: Storage, Conveying and Metering
...al, regrind and masterbatch); - the prescribed residual moisture content must be observed, without inadmissible fluctuation; - soiling or foreign bodies in the product flow must be avoided; - contamination of the production environment with dust or powder must be prevented. It thus makes sense for processors to acquire an overview of the processes and possibilities that exist in the fields of storage, conveying and metering. Only with this knowledge will they be in a position to compile a conce...
Kunststoffe international, 2005-11-21, Materials Recycling
...re no longer able to assume their function as a binder because of their irreversible crosslinking, which is why they must be calculated at the same value as mineral fillers when considering their reuse. In fact, the costs for producing the recyclate powder are higher than those for the mineral fillers they are replacing, which is why recycling is not economically viable here. Glycolysis involves breaking down polyurethanes with the addition of glycol and additives. The resultant polyol is suitab...
Kunststoffe international, 2005-11-21, Medical Technology for the Mass Market
...with the same active ingredient, he will probably choose the one which is more comfortable and easier to use for the patient. Intelligent dosage systems are clearly booming. Typical examples include pens for the injection of liquids for diabetics, powder inhalers and needle-less injection devices. The driving force behind this development is the increasing tendency for the medication to be administered by the patients themselves without any need for help from medical staff (Fig. 1). This gives...
Kunststoffe international, 2005-11-21, Metal Injection Moulding: Precision Parts Rapidly and Economically
...nts, metal injection moulding (MIM) represents an ideal approach to meet these objectives. An absolute prerequisite, however, is knowledge of the specific limits of the process. Thorsten Hickmann Eric Klemp It is for good reason that the number of powder metallurgically produced parts continues to grow. The benefits are obvious, since parts produced in this way correspond very closely to the final geometry: They are characterised by very high accuracy as well as surface quality and require alm...
Kunststoffe international, 2005-11-21, Metallised Synthetic Fibres: Shielding Electromagnetic Radiation
...were exposed to cyclic temperature stress between 20 and 80°C, a decrease in conductivity to about one-fifth of the original value was observed after only 5 temperature cycles [6]. In the same tests, a polymer filled with 30% Al flakes and 20% Fe powder showed a sharp drop in shielding attenuation values after only three temperature cycles (20/80°C). In this case, compared with the starting sample, shielding effectiveness at 1GHz was reduced from 23 to about 11dB, i.e. by half. The reason for th...
Kunststoffe international, 2005-11-21, Mixing and processing: PVC Dry Blends for Pharmaceutical Film
...roduction building was sufficient because even the new larger heating/cooling mixer combination was of compact design. Suitable Concept for Wide Variety of Formulations The basic material for the pharmaceutical film made by ac-Folien is a PVC powder produced by suspension polymerisation (S-PVC). Other ingredients in the formulation are E-PVC produced by the emulsion process, a PVC copolymer to improve the thermoforming properties, plus different auxiliaries and additives in the form of powdere...
Kunststoffe international, 2005-11-21, Modified Polyphenylene Ether (PPE)
...e allows it be used in paint ovens. Over the past few years, conductive (PPE+PA) blends have been introduced that offer electrostatic painting without requiring the use of conductive primers. The material has also been shown to be suitable for powder coating, thus opening up a whole range of potential applications outside the automotive sector. GE Plastics is continuing to develop new (PA+PPE) blends, focusing mainly on conductive, higher-heat, lower-CTE materials for larger vertical car body pa...
Kunststoffe international, 2005-11-21, Modified Polyphenylene Ethers (PPE)
... These can be electrostatically painted without the need for an electrically conducting primer. Fenders and front-ends as well as smaller applications like tank flaps and decorative trim are made with these materials. They are also very suitable for powder-coating applications. Another area of application for PA/PPE blends is under the bonnet, e. g. connectors and fuse boxes. The advantage of the blends over other semicrystalline thermoplastics is their excellent dimensional stability at high te...
Kunststoffe international, 2005-11-21, More Light
...extrusion product is between three and four days. Perfect Surface Appearance In the production hall for lighting units for outdoor applications, Elkamet has rotational mould units which it built itself. The moulds, filled with powder, are rotated around two axes during the rotation moulding process and are heated and cooled with oil as the heat transfer medium. Outside the hall is a heat exchanger that heats the oil to temperatures of up to 330°C. The hollow shapes that are produced here can w...
Kunststoffe international, 2005-11-21, More Throughput with Less Wear
...eed zone. The air acts as an insulator and prevents proper preheating of the material by contact with the screws and barrel wall. In conventional extruders, this air is not removed until the venting zone, beyond 18 D. If the material is still fairly powdery in the venting zone, e.g. in highly filled formulations, powder may swirl up into the venting unit. With the new 36 D extruders, the material is compacted and preheated after the feed. It passes the first venting zone at only 15 D (Fig. 2). H...
Kunststoffe international, 2005-11-21, Mould Design: Advances in Injection Mould Design
...ion and provide protection for cable connections. The space-saving thick-film heating is concealed under a rugged covering. Complete “hot halves“ are now almost standard for Günther. The replaceable needle guide made of powder metallurgical steel extends the service life considerably. Both the needle and needle guide can be replaced easily (Fig.10). Should the hot runner channel change direction through use of a rounded end plug to guide the flow or through use of an optimised transition chamber...
Kunststoffe international, 2005-11-21, Mould-making 2000
...rocessing range allow even large-size cold-runner systems to be balanced with less effort. New Steels Increase Accuracy Another important contribution to the quality improvement of injection moulding tools for silicones was made by the wide use of powder metallurgical or steels produced by the HIP (high-temperature isostatic pressing) method. This allows high article accuracy to be maintained even during long runs. To achieve this, cavity dimensions may deviate by a maximum. 5 µm; so as ...
Kunststoffe international, 2005-11-21, Multi-Material Mould with Rotary Mechanism
Multi-Material Mould with Rotary Mechanism 16+16-cavity Injection Mould for the 2-Materialbase of the Housing for a Powder Inhalation System Hansjörg Keusgen, Bahlingen/Germany In order to assure reliable production and high yields, moulds used for mass production of high-quality multi-material plastic products must meet very high standards. High-precision multi-material moulds and a well-engineered rotary mechanism guarantee short cycle times. Function and design play an increasingly im...
Kunststoffe international, 2005-11-21, Nanocomposites - En Route to Application
...for use in scratch-resistant coatings on glass, for example. Development work here has produced a series of inorganic nanoparticles that are dispersible in aqueous and organic media. Examples include synthetic, dispersible aluminate (boehmite) powder (Pural, Disperal, Dispal) from Condea, which now belongs to Sasol Chemical Industries Ltd. POSS and Hyper-branched Polymers Over the past decade, new approaches have been adopted towards finding a solution to the nanoparticle dispersion problems i...
Kunststoffe international, 2005-11-21, Nanopigments: Dwarfs in Automobile Coatings
Automotive - Nanocomposites Dwarfs in Automobile Coatings Nanopigments. New processes have been developed to manufacture barium sulphate nanoparticles that can be dispersed in powder form without mechanical or chemical aids. Selected analytical methods ensure high quality. Stephan Haubold There are high expectations for nanocomposites – especially in the field of automotive coatings – and the first such products on the market are already making a big impact. In most cases, the chemical compo...
Kunststoffe international, 2005-11-21, One Step Closer to Nature
...ng to install artificial turf, since public subsidies are frequently only awarded to artificial-turf pitches that conform with the standard. Rubber granules are generally made of shredded tyres (90 000 t used tyres were processed into granules and powder in 2000 [4]) and/or other technical product waste. They are a motley collection of different types of rubber that were optimised for their original application. A modern tyre, for example, is made up of a number of different rubber compounds (tr...
Kunststoffe international, 2005-11-21, PBT Oligomers: Always in Good Form
...IM (structural reaction injection moulding). The CBT resin products, together with the required catalysts, produce stable one-component systems. According to customers' requirements, they are available as pellets, granules or powder with defined particle-size distributions (Fig.1). They can be processed – preferably by thermoplastic techniques – in combination with additives or reinforcing agents to form thermoplastic structural composites, or alternatively can be reactively compounded in ex...
Kunststoffe international, 2005-11-21, Peak Performance in Profile Extrusion
... The loads on the screws and gearing are typical examples of a range of other extruder components. PVC window profiles are mainly produced on counterrotating twin-screw extruders with tightly intermeshing screws. In the C-shaped melt chambers, the powdered polymer is melted with the least possible shear loading. The outstanding self-cleaning effect of the screws, in conjunction with a narrow residence-time range, take account of the low thermal stability and shear sensitivity of PVC. This extr...
Kunststoffe international, 2005-11-21, Pelletised and Powdered Rubber: New Feedstock from Old Tyres
Recycling New Feedstock from Old Tyres Pelletised and Powdered Rubber. In a new tyre recycling facility, post-consumer tyres can be broken down into their constituents. The rubber content is then ground to pellets and to high-quality powdered rubber. Powdered rubber is the product of a cryogenic process which involves the use of liquid nitrogen as a cooling agent. Ursula Mertig The official launch of a unique tyre recycling line located at Ohlsdorf/Austria by Gummi Verwertungs GmbH (GVG) in the...
Kunststoffe international, 2005-11-21, Perfect optical symbiosis
...oint of view of BASF Coatings this does not apply to clear paint, but low emission systems are preferred here, to which belong hybrid UV clear paints with high solids content. In industrial plastic paints improvements in hybrid systems as well as in powder paints with lower baking temperatures are being worked on. Pre-treatment Flaming continues to dominate among pre-treatment methods. According to estimates by DuPont Performance Coatings it is used in about 90 % of all cases (Fig 4). The reas...
Kunststoffe international, 2005-11-21, Physical Blowing Agents: Foaming Plastics with Inert Gases
...Both processes will only be mentioned in passing here. Depending on the process and required density, chemical or physical blowing agents are used to initiate the foaming process. Chemical blowing agents are generally added to the plastic pellets in powder or granule form and decompose at elevated temperatures. Above the specific decomposition temperature of the blowing agent, a gaseous reaction product is released, usually nitrogen or carbon dioxide (CO2), which acts as a blowing agent. Because...
Kunststoffe international, 2005-11-21, Polyaryletherketones (PAEK)
...cantly higher tensile strength and higher flexural modulus at 250°C, - higher compressive strength, and - greater durability. New Applications Innovative developments include, for transport applications, a novel cylinder head gasket based on a powder coating process from STE Dichtungstechnik, which combines the positive properties of PEEK with those of PTFE. The cylinder head gasket, marketed under the trade name Monomet, is punched from solid steel with a specified thickness distribution, and...
Kunststoffe international, 2005-11-21, Polyphenylene Sulphide (PPS)
...o an important engineering plastic material for exposed applications. Poly(thio-1,4-phenylene), or simply PPS, is made from dichlorobenzene and a sulphur source. With cross-linked PPS as well as with linear PPS, this synthesis leads to polymers in powder form. Cross-linked PPS was developed by Chevron Phillips in the year 1953. The linear PPS production method is based on this technology and creates technically superior products. Both products are partially crystalline and have a melting point...
Kunststoffe international, 2005-11-21, Polyphenylene Sulphide (PPS)
...ight PPS grades are nowadays essentially based on the process that was improved by Edmunds and Hill in 1967, involving the synthesis of para-dichlorobenzene with the aid of sodium sulphide in a polar organic solvent to produce a polymeric powder. The salt that is produced as a result is relatively easy to wash out. A few years later, Phillips Petroleum patented a synthesizing process for obtaining grades with a higher molecular weight, a process that has since been further optimised – in modifie...
Kunststoffe international, 2005-11-21, Polystyrene recycling: Regranulates from Post-consumer Waste
...filter system and then prepared (adjusted to give a favourable solvent-to-plastic ratio for further processing) and the PS precipitated through evaporation of the solvent. The PS which is obtained in the form of a dry powder was then processed into granulate on a special extruder. Only material from sorting facility 3 was used for the solution polymer recycling process. The comparison of the characteristic values obtained for the granulate with the values from conventional extrusion recycling sh...
Kunststoffe international, 2005-11-21, Polyurethanes: Diversity in PU
...o offering low emissions at the same time. Desmopan is being developed into a décor material for the automotive interior in partnership with Geba Kunststoffcompounds GmbH. An instrument panel produced by blow moulding rather than the customary powder-slush process was displayed at K2004. Thieme uses Bayflex EA in safety elements for the automotive interior and exterior. These deform under load but, thanks to their structure, regain their original shape again. Elements of this type provide head, ...
Kunststoffe international, 2005-11-21, Powder Injection Moulding: Joining Injection Moulded Sintered Parts in the Green-compact Phase
Joining Joining Injection Moulded Sintered Parts in the Green-compact Phase Powder Injection Moulding. The complexity of parts produced by powder injection moulding is ultimately limited by the possibilities available in the mould technology. Unlike moulds for plastics technology, not even small undercuts can be accommodated by forced demoulding. Ceramic or metal green compacts can now be joined using standard techniques to form complex geometrical structures. Helmut Potente Lars Wilke Powder i...
Kunststoffe international, 2005-11-21, Processing of Thermosetting Resins: Pioneering Spirit Needed for Survival of the Species
...return valve, except when BMC is being processed. For processing non-abrasive moulding compounds, the barrel and screw can be made of nitrided steel. Fibreglass and mineral-filled moulding compounds also require bimetallic barrel designs and usually powder metallurgical steels for the screw. The resultant high level of abrasion protection ensures that the plasticating unit has a long service life. Wear of the barrel and/or screw increases the gap between both components that has a direct influen...
Kunststoffe international, 2005-11-21, Processing Technologies: Processing Fibre-reinforced Plastics
...method used for the prepreg materials and the resulting varying degrees of impregnation and consolidation, a distinction is made between the types of prepreg shown in Table1 [11]. As part of a joint project funded by the BMBF [12], a powder prepreg machine was designed and built at IVW, which can be used to coat various types of flat textile structures on one or both sides. With the aid of this machine, it is possible to produce powder prepregs at low cost that can later be further processed by ...
Kunststoffe international, 2005-11-21, Product Marketing: Global Trends in Packaging Design
...German names “flink” and “flott” suggests that the idea was borrowed for a new product category. Back to our example: Even the most skilled of women needs a mirror to apply lipstick. Probably even more than to powder her face. However, in the latter case, a mirror has been provided for years – even in the lower price categories, while the lipstick with mirror took until fairly recently to be “invented”. It is not always necessary to reinvent the wheel. Sometimes an intelligent combination of ind...
Kunststoffe international, 2005-11-21, Production Monitoring: Particle Monitoring on the Extruder
...f optical parts) and the properties of these parts (such as stress cracking behaviour). Particles and inhomogeneities of this type include gel particles, specks, agglomerated filler and gas bubbles, and also incompletely melted granules or grains of powder. Effective detection of defects of this type cannot, however, be left until the semi-finished and finished parts are inspected offline, but requires the application of time and cost-saving Process Analytical Technology (PAT) at the melt compou...
Kunststoffe international, 2005-11-21, Progress with Standard Components
...laser sintering (DMLS) allows the manufacture of metal moulds, which need no secondary processing and are very close to the subsequent production parts in terms of material, dimensions and tolerances. A computer-controlled laser beam solidifies the powder material layer by layer to the desired shape and builds up complex geometries fully automatically within a few hours. Metal parts can thus be produced with great accuracy because the powder is sintered with virtually no shrinkage. The mechanica...
Kunststoffe international, 2005-11-21, Pulverising High Performance Polymers
Pulverising High Performance Polymers Efficient Procedure for Producing Powders High performance plastics are used more and more often as powders in processing whereby the particle size distribution is important. Often there are applications only beginning with a certain powder fineness. The wide temperature range in which modern plastics remain flexible and cold tough makes reducing particle sizes to significantly less than 100 µm a challenge. The particles react to the applied forc...
Kunststoffe international, 2005-11-21, PVC Processing: The Historical Development of the Counter-rotating Twin-screw Extruder
...xtruder manufacturers, as it were, has three main branches: Anger (Mapre), Kestermann and Schloemann (Pasquetti). Following the founding of the Anger company, the brothers Anton and Wilhelm Anger developed a process in the early 1950s for extruding powder into a finished pipe in a single working step (Fig. 1) [1]. Almost simultaneously, they also succeeded in solving the problem of how to join pipes by means of plastic. In 1954, Anger developed a Mapre extruder. Just one year later, the first s...
Kunststoffe international, 2005-11-21, Quality of SMC Surfaces: Paintability Enhanced
...velopment of TCA has had a tremendous positive effect on the quality of surface automotive panels. But there are more strides to be made. Unlike Ford, some other OEMs use a powder prime process. Traditionally, SMC does not perform well in powder coating, most likely due to water absorption. Research at the ThyssenKrupp Budd Company Technology and Innovation Centre is attempting to solve this problem by exploring the chemistry of the SMC. ThyssenKrupp Budd is experimenting with changes in the bas...
Kunststoffe international, 2005-11-21, Requirements and Markets: Polymeric Flame Retardants
...e foam. Table2 shows the composition of the foams and quantities of flame retardant extracted. Pentabromobenzyl acrylate, a reactive flame retardant: Pentabromobenzyl acrylate (FR-1025M-DSBG) is a monomeric brominated flame retardant supplied in powder form. It is unique in that it can be reactively polymerised during processing on standard commercially available compounding machinery. The property spectrum of pentabromobenzyl acrylate (Fig.3) combines a high bromine content with good thermal ...
Kunststoffe international, 2005-11-21, Retrospective: The Development of Injection Moulding
...ction moulding no longer represents an economically viable method for producing parts for which the material properties of other plastics (moulding materials) suffice [...], e.g. clasps, buttons, powder, cosmetic and jewelry cases, toy figures, switch levers, pushbuttons, handles for tools and cutlery, small appliance housings. [...]” Judging from the above report, injection moulding was not immediately considered superior to the well-known technique of compression moulding. In fact, even today ...
Kunststoffe international, 2005-11-21, Routes to Microcellular Foam
...ility, nitrogen and carbon dioxide are the mostly widely used physical blowing agents today [3]. After all, it is through supersaturation of the polymer with blowing agent that foaming is initiated. Chemical blowing agents are added as solids (e.g. powder, masterbatch) to the polymer granules prior to processing. The mixture is melted so that it can flow. More heat is then added to initiate decomposition of the blowing agent, which is already homogeneously dispersed in the polymer matrix. The re...
Kunststoffe international, 2005-11-21, Sealing Through Contamination
...ected as a reference polymer. In laboratory and practical tests, monolayer films, coextruded films and laminated structures were compared to each other. The contaminants studied covered a wide range - such as tomato juice, milk, olive oil and coffee powder. Experimental The structures used for this program are listed in Table 1. The various sealing polymers which were compared are described in Table 2. Table 3 lists all the other polymers and adhesives used in the study. Appropriate additives ...
Kunststoffe international, 2005-11-21, Series Production - Quickly
...ign after production of the first 3D-CAD models. Concept models are available from different manufacturers in different versions. With equipment from the Z-corporation (USA) it is possible to develop coloured models on the basis of starch or gypsum powder, for instance. Objet Geometries Ltd. (Israel) develops and markets a user-friendly plant with which durable models can be made of photopolymers. If in the early phases stringent requirements are already made on the strength or the resistance of...
Kunststoffe international, 2005-11-21, Shaping New Realities!
...istant polyester polyurethane sole of a walking boot (photo: Hoocker S.A.C, Barcelona/Spain) Fig. 3. Brussels tram track with a PU elastomer surround (photo: Hyperlast, Dordrecht/Netherlands) Fig. 4. Filling unit for the production of recycled PU powder on an industrial-scale plant (photo: Mobius Technologies, Grass Valley, California/USA)
Kunststoffe international, 2005-11-21, SLM Technology: Prototypes for Biomechanics
...omplexity in a single process. As a result, SLM technology is opening up new perspectives for medical implants. Ronald Simmonds “At present the most innovative rapid prototyping development for the production of metal components using any type of powder,” is how Dr. Chris Sutcliffe, Head of the Bioengineering Department at Liverpool University, UK, described the SLM process jointly developed with MCP-HEK (see box). Liverpool University was the first university in the UK to invest in a machine li...
Kunststoffe international, 2005-11-21, Small But Potent
...rapid solidification, - narrow temperature interval between free flowing and solidification, - dimensional stability (shrinkage and contraction), - no mould deposits, - high structural viscosity, - homogeneous batch, and - small pellet dimensions or powder. The important feature for reproduction fidelity is the viscosity of the polymer melt under process conditions, which decreases by several orders of magnitude with increasing shear rate. The term pseudoplastic behaviour is used. In microstruct...
Kunststoffe international, 2005-11-21, Styrene Plastics: Wrapping up Beauty in an Attractive Pack
...cs is a key factor in this. Having said that, the term ‘packaging’ should not be taken here to mean conventional packaging solutions like so-called ‘flexibles’ or hollow containers. In the cosmetics industry, packaging can mean powder compacts, delicately designed scent flacons, lipstick holders with a twist mechanism, or any of the broad range of mechanical or liquid liners, which, differently formulated, offer a wide variety of application properties. Cosmetic Packaging: An Ideal Application ...
Kunststoffe international, 2005-11-21, Tailor-made Compression Moulding Process: Automatic Compression Moulding Machines for Powder Materials
Tailor-made Compression Moulding Process: Automatic Compression Moulding Machines for Powder Materials The charging and densification of powders in moulds requires a great deal of skill from producers of semi-finished goods and high-performance parts. The necessary level of density distribution in the part is just as critical as geometrical accuracy. Stefan Herzinger Charging and compression systems have to be able to process a wide range of materials. Materials suitable for compression in...
Kunststoffe international, 2005-11-21, Tailor-made Properties: Modification of Polyamides
...merox) are solid at room temperature. They can improve the flexibility, elasticity and water repellency of all kinds of polymers, and are used predominantly for the production of polyamides and polyesters and as a building block in, for example, powder coatings through reaction with glycidyl methacrylates. Azelaic acid is produced by oxidation with ozone (ozonolysis) from oleic acid (C18) [5]. This crystalline solid dissolves in hot water, alcohols, diethyl ether and other polar solvents. Deriva...
Kunststoffe international, 2005-11-21, Technology and New Dimensions
...t company in Germany this year to stage its Technology Show. The company, based in Loßburg/Germany, concentrates its activities on technological progress. Arburg showed its complete range of standard machines and specialty equipment, e. g. from its powder injection moulding and CD laboratory. The 2,100 visitors to the Show were able to inspect not only the machines that make up the company's standard and specialty machine range, but also the new machines presented at the Fakuma, such as th...
Kunststoffe international, 2005-11-21, The Design of Injection Moulding Screws
...f injection screws and non-return valves to corrosion and wear can, however, not be reliably achieved through the use of conventional full-hardened and nitrided steel with thermochemical surface layer hardening. One possible alternative is to use powder-metallurgically produced steel of hard metal, although their big disadvantage is the high manufacturing costs. Another approach towards improving the wear resistance of plasticising components is hard chromium plating. However, one of the main di...
Kunststoffe international, 2005-11-21, The Market for Masterbatches in Germany
...t any significant new areas of application for additive and colour concentrates in this market within the foreseeable future. In the field of polyolefins, which make up some 65 % of the market, the methods of incorporating the colourants/additives - powder (pigments), powder mixtures, pastes, liquid colourants, compounds and masterbatches - have more or less stabilized. Only minor changes can therefore be expected for the overall market (Fig. 2). Over and above this, there is a noticeable trend ...
Kunststoffe international, 2005-11-21, The PVC Loop Closed
...e PVC Loop Closed Recycling of PVC Composites Jean-Marie Yernaux, Brussels/Belgium, and Reinhard Saffert, Rheinberg/Germany A new recycling process selectively dissolves the PVC in composite products. The end product is a clean PVC compound in powder form that may be used without further processing, such as melt filtration or granulation, and in some cases may even be employed in the original application (closed-loop recycling). Nowadays, there is a consensus in society that the landfill...
Kunststoffe international, 2005-11-21, The Right Software Brings Success
..., Dieburg/Germany, is capable of processing fibres up to 50 mm in length. The material therefore has much greater strength. A useful side effect is that the carbon fibres render the material electrically conducting and, like metal parts, amenable to powder coating. This allows very high quality, robust surfaces to be produced in almost any colour. Up until 1993, Thermoplastik GmbH performed only contract work and did not have its own design department. As it was now going to develop its own prod...
Kunststoffe international, 2005-11-21, Thermoplastic Films: Car Body Parts With and Without a Paint System
...e demands made by the automotive industry on the scratch and abrasion resistance of the thermoplastic surface. In this respect, the testing concepts of the OEMs differ significantly. Figs. 2 and 3 show the scratch resistance of an automotive powder coating, a PC-based film from GE, and the Senotop film with facing layers of PMMA. Test method A (Fig. 2) shows the needle scratch resistance according to DIN 53 799-4-15, while test method B (Fig. 3) shows the abrasion resistance according to DIN 55 ...
Kunststoffe international, 2005-11-21, Thermosets
...ial applications. These applications include electrical insulation, adhesives and FRP, as well as UV-curable coatings, since cycloaliphatic resin systems are radiation-curable. Other further developments in the latter sector involve powder coatings that are heated by IR radiation and then radiation-crosslinked, water-based UV-curable resin systems and more ecofriendly epoxy acrylates [1]. For floor coatings, there is a range of innovations, e.g. a cycloaliphatic amine for rapid curing [3]. A sol...
Kunststoffe international, 2005-11-21, Trends in Injection Moulding: Specialists Increasingly in Demand
...new processes will come on stream and will be perfected further down the line. The key areas have already been mentioned: miniaturisation, multi-functional mechatronic parts, microprocessor engineering, MID, optical parts, nanotechnology, and powder materials – in many areas, research and development work on plastics is already proceeding in parallel with a view to opening up new application areas for them. All these developments have a common feature: the injection moulded parts are becoming mo...
Kunststoffe international, 2005-11-21, Tribological Applications: PEEK Compounds in an Aqueous Environment
...icants. These components give rise to specific properties: - The addition of reinforcing fibres increases the mechanical loadbearing capacity of the bearing material and generally also reduces wear. - The addition of internal lubricants such as PTFE powder or graphite decreases the friction coefficient. As a result of the lower friction, surface shear stress and therefore frequently also wear are reduced. Because of its high price, PEEK is preferably used in applications unsuitable for other mat...
Kunststoffe international, 2005-11-21, Two-component Micro Powder Injection Moulding: Three Special Processes in One
Injection Moulding Three Special Processes in One Two-component Micro Powder Injection Moulding. To produce multifunctional ceramic micro-parts, multicomponent, powder and micro injection moulding were combined in one process. This article describes the injection moulding of high-performance heating elements with adjustable electrical resistance. Powder injection moulding allows economic mass production of complex parts of metal and ceramic. Multicomponent injection moulding offers multifunctio...
Kunststoffe international, 2005-11-21, Unobtrusive, Invisible, Universal
...In fact, however, the term ‘plastics’ no longer adequately describes the range of materials that can be processed by injection moulding. In recent years, particularly in the high-end segment, new materials based for example on ceramic and metal powder mixtures have been gaining increasing importance. Historically, Arburg was one of the pioneering group of companies that found a way to make their products more widely usable by replacing conventional materials with plastic. In the 1950s, the compa...
Kunststoffe international, 2005-11-21, Viscosity Measurement: Determining Rheological Data Directly at the Machine
...ns of exchangeable inserts in the measurement nozzle (Fig.8). Behaviour of Filled Plastic Compounds Wall slip even occurs in highly filled compounds such as wood-plastic compounds or PIM feedstocks [5]. Feedstocks are used in powder injection moulding (PIM) and comprise a binder system and a metal or ceramic powder. The binder system usually consists of a polymer-wax mixture. This improves the flow properties of the feedstock while allowing the binder to be easily removed by thermal means (de-b...
Kunststoffe international, 2005-11-21, Wear Protection: The Plastication Unit as a Focus of Conflict
...g on a cylinder liner requires an appropriate process technology. The most economic method is centrifugal casting for the production of bimetallic cylinders. The hard material alloy of reduced melting point is charged into a tube in the form of a powder. This is sealed at the ends and rotated and, while rotating, is heated to a temperature at which the hard material alloy melts. The tube is then cooled while rotating at high speed (Fig.3). This results in a wear-protection layer that is intimate...
Kunststoffe international, 2005-11-21, What Hardens Surfaces
What Hardens Surfaces Powder-Metallurgical Materials as a Solution to the Problem of Mould Components at Risk of Wear in Injection Moulding Wolfgang Thierfelder, Andreas Hoffmann, Reutte/Austria, and Stefan Schmidt, Frank Ohm, Thomas Eulenstein, Lüdenscheid/Germany Wear on mould surfaces or mould components still constitutes a problem in injection moulding. By using annealed and surface-treated materials, an attempt is made to reduce the impact on the mould and hence on the surface finish ...
Kunststoffe international, 2005-11-21, Wood extrusion: Wood from the Extruder
...me profiles is concerned. Wood extrusion is targeted more at markets or niche markets that have been covered until now by traditional materials such as wood or MDF board. The surfaces of the wood fibre profiles can be e.g. veneered, lacquered or powder coated. Furthermore, these products can be nailed, screwed, drilled or planed like wood, or shaped and moulded like thermoplastics. The fields of application for wood profiles vary enormously. Typical examples are decking elements and shuttering b...
Kunststoffe international, 2005-11-21, Worldwide Demand is Increasing: Polyphenylene Sulphide (PPS)
... for reinforced compounds, which can contain up to 65% reinforcement. Processing by Conventional Techniques PPS is manufactured from p-dichlorobenzene and a sulphur component. With both crosslinking and linear grades, the synthesis yields powder products. Both grades have a melting point of about 285°C and show comparable glass transition temperatures (85 to 100°C) and post crystallisation temperatures (110 to 135°C). The production of linear PPS is based on the process developed in 1967 for th...
Kunststoffe international, 2005-11-21, Worldwide Growth: Engineering Plastics
...erm supply reliability and constancy of formulation are also guaranteed. The medical grades of the polyacetal copolymers is particularly used for equipment that has to satisfy high dimensional stability. An example is the dosing mechanism in powder inhalers (Title photo, Fig.5). For example, the new powder inhaler consists of 22 parts. A total of nine components are made of materials from Ticona, including medication container, container cover, slit and valve release. Here, POM is impressive for...
Kunststoffe international, 2005-11-21, “It Depends on the Part”
...ce, they are increasingly finding use in the automotive industry. A process patented by Engel allows product innovations and freedom of design in LSR parts through selective cavity production by means of gas-assist technology [18]. Powder injection moulding (PIM) allows various materials (metals and ceramics) to be processed into complex parts. Examples include bearings, valves, rocker switches etc. Thixomoulding (magnesium injection moulding) is a process in which the molten metal is injection ...
Kunststoffe international, 2005-11-30, Plug-in Connectors: Selectively Metallisable Polymer Compounds
...llisation process. Activating the polymer surface with palladium seeds is not necessary with this process. The complete two-component plug-in connector was then selectively metallised in a single metallisation step. Apart from the palladium powder, two palladium compounds and different types of copper powder were used as activation seeds for the metallisation. Another problem, apart from the incorporation of the metallisation seeds into the blend, is the difficulty of chemically metallising sold...
Kunststoffe international, 2005-11-30, PTFE Multicomponent Compounds: A Material for Hard and Soft
...lers are glass in the form of fibres, beads, hollow spheres or ground glass, carbon as coking coal, electrical carbon, conductive pigment, graphite or carbon fibres as well as bronze in various forms. Also used are molybdenumdisulfide, steel powder, aluminium oxide and wollastonite. The properties vary in accordance with the filler, e.g. the coefficient of friction. This is very low for graphite and very high for glass. In the latest compounds, the manufacturer combines various fillers to yield...
Kunststoffe international, 2006-01-25, Added Value: Compounding at Maximum Power Density
Compounding Compounding at Maximum Power Density Werner Wiedmann Added Value. In compounding, the limiting factor on throughput is usually the available power density. A disproportionate increase in economics and product quality requires a finely balanced increase in extruder torque, speed and free volume. The technological development of compounding on co-rotating extruders has been decisively influenced by improvements in design, material and computational methods. This has made it possibl...
Kunststoffe international, 2006-01-26, Processing: Continuous Process for Manufacturing Natural-fibre-filled Plastic Boards
...des a final product with reproducible quality in fully automatic continuous operation at low energy and manufacturing costs. Start up is automatic without prior heating. Fibres of renewable natural materials, particularly wood flour, plastic chips, powder or pellets, together with lubricants and other quality-determining additives are gravimetrically metered, homogenised and plasticated and then extruded through the openings in the die plate (Fig.3). Rotating knives cut off the extruded material...
Kunststoffe international, 2006-01-30, Dosage Systems: Functional Packaging for the Medical Sector
...ontribution towards improving the frequently inadequate or inconvenient process of taking drugs. One example is the treatment of asthma. Alongside a high degree of purity and sterilisability, other specifications for a dosage mechanism for dry-powder inhalers included absolute dimensional stability and good surface-slip properties (title photo, Fig.4). POM can also be used to produce a valve for aerosol inhalers which permits precise dosing of the active ingredient through the necessary droplet ...
Kunststoffe international, 2006-02-22, Cockpit Surfaces: Workplace and Living Room on Wheels
...ld surfaces are created using casting techniques based on a leather model (or pattern), via electroplating or via the Mond process. With the aid of engraving and etching, additional corrections to the surface structure can be made. Powder Slush is one of the oldest skin moulding technologies used for large-scale production. In spite of all scepticism, especially regarding the most important material, PVC-P, compounders and processors have succeeded in refining this technology to the point that t...
Kunststoffe international, 2006-02-27, Automaking: Inspiration in the Interior
...e carrier are grained or painted in colours specified by the customer. Partial Foaming as Design Option The process involves several steps. Visteon obtains the skins from Benoac Fertigteile GmbH, Peine, which produces them via the powder slush method. Since the powder is heated in a tumbling mould with a contour identical to that of the instrument panel, the slush skin is preformed. This skin is placed in the lower half of the foam mould and held in place via vacuum. The carrier is placed in th...
Kunststoffe international, 2006-04-25, Marking: Coding at Full Speed
...This is a centre and rebate seal system for turn-tilt windows, house front doors and side doors and slide-and-tilt elements, with outstanding acoustic and thermal insulation properties. All Kinds of Identification All profiles are produced from PVC powder by a complex process of melting, shaping and hardening. It is cooled in a calibration zone before being cut up into individual 6-metre lengths. The applicable standards require the profiles to be identified every metre. At Dimex, this is perfo...
Kunststoffe international, 2006-05-23, Trends and Products: Masterbatch Manufacturers in Germany
...ical applications are in the automobile industry. BASF Pigment GmbH, Cologne/Germany, covers the whole range of applications and markets. Still today colouring fibres (Fig.2) represents another speciality in the masterbatch world. Liquid colours and powder pigment mixtures are further niche products complementing classical masterbatches. A further supplier of colorants for fibres and thin film is Clariant Masterbatches (Deutschland) GmbH with establishments in Lahnstein/Germany and Ahrensburg/G...
Kunststoffe international, 2006-08-02, Thermal Balance: Conformal Cooling on the Advance
...oulds worldwide are equipped with this type of cooling and fulfil their function every day. A relatively newly launched technique, which has already gained wide attention, is direct laser forming. This process generates a mould insert from a metal powder bed, often with an original mould making material, such as DIN No. 1.2343. Ultrafine metal powder is placed in a heated chamber on a build platform that can be lowered. A laser directly melts the powder bed, which has been levelled by a slide, a...
Kunststoffe international, 2006-08-06, Conformal Cooling Channels: Cooling Complex Parts
...nel geometries without seam can only be produced by generative manufacturing processes. One example of these is Direct Laser Forming (Trumpf GmbH & Co. KG, Ditzingen/Germany), which permit the inserts to be built up in one piece from a tool-steel powder material. Materials appropriate for mould making include, for example, the tool steels X38CrMoV5 1 or X42Cr13 [3, 4]. In Direct Laser Forming, metal powder is applied layer by layer and selectively melted by a laser. The work platform is lowered ...
Kunststoffe international, 2006-08-06, Laser Forming: Cores for Garden Equipment
...his is standard practice in many injection moulding shops. For some months, however, Gardena has for the first time started using an injection mould whose cores are produced in a direct laser-forming process. In direct laser forming pure metal powder without binding agent is melted on layer by layer by the laser and fused to form a virtually pore-free workpiece of complex geometrical shape and in a very short time directly from the CAD model. Product Design Requires Ingenious Cooling. The use o...
Kunststoffe international, 2006-09-05, Viscosity Measurement: Material Characterisation in Powder Injection Moulding
Injection Moulding. Material Characterisation in Powder Injection Moulding. Christian Gornik Viscosity Measurement. Large quantities of complex metal or ceramic components can be produced by powder injection moulding in a cost-efficient way. The manufacturing method and the composition of the so-called feedstock often lead to variations in process stability and part quality. Two methods prove suited to characterise the feedstock's properties of flow and thus the mixture's homogeneity....
Kunststoffe international, 2006-09-05, Wood-filled Thermoplastics: No All-purpose Fire Protection
...reak) were not significantly influenced by the flame retardant content. The liquid flame retardants, DPK and TOL, as well as TEP in higher contents, brought a reduction in tensile elastic modulus as per EN ISO 527. The flame retardant powder products Alfrimal 103 and 437, on the other hand, caused a significant increase in tensile modulus. Higher contents of TEP produced a considerable softening of the wood/plastic composite (Fig.4). The flexural impact tests as per EN ISO 179 showed a fall in f...
Kunststoffe international, 2006-09-27, Trend Outline: Integration and Intelligence
...k moulding compounds (BMC) are increasingly used. Further efforts are being undertaken on enhancing continuous feeding of these compounds. Process Innovations Tap New Fields of Applications. Processing powder materials such as steel, hard metal or ceramic powder opens up new areas of application. Powder injection moulding of these materials permit for the production of geometries so complex that they cannot be manufactured in a traditional process. This method permits for highly economic produ...
Kunststoffe international, 2006-09-28, A Holistic Approach: Integrated Engineering
...ers are the model data generated in the CAD system. The more common of the two processes is now generation of a polymer laser-sintered prototype, which the laser builds up layer by layer from a polyamide powder. The disadvantage of a sandstone-rough surface, caused by a relatively large layer thickness, is offset by advantages such as high strength and elasticity, which are not possible in stereolithography. The economic batch size is one to five parts, which can be used for the first functional...
Kunststoffe international, 2006-09-28, From Pretreatment to Finishing
...motion of the belt and rotating screen. Subsequent thermal treatment assures good bonding of the decorative material to the plastic surface. To improve the wear and abrasion resistance of the surfaces, the screen can also apply a micro-fine powder. Winding and Cooling Film. Multi-layer barrier films have to meet increasingly stringent requirements in terms of their properties. In order to provide an optimum film for demanding customer products, Windmöller & Hölscher, Lengerich, has developed th...
Kunststoffe international, 2006-10-30, Laser Sintering: Functional Prototypes Produced from PEEK
...materials with high elastic modulus and high tensile strength, coloured orange in Fig.1, the particle-filled sintered materials do not achieve the excellent properties of the fibre-filled injection moulded materials. This is due to the fact that the powder used in the laser sintering process as starting material cannot be filled with fibres but only with particulate additives. For this reason, their tensile strength, in particular, can only be increased to a limited extent. As yet there are no l...
Kunststoffe international, 2006-11-24, Additive Systems: Composition Decides
...ult to manufacture very small wooden parts. Employing WPC, in turn, makes it possible to produce a broad range of large and small components. For WPC production, the wood, plastics and additive materials are at hand in a granule or powder form. A variety of methods are used to produce almost any form or size desired. By simply applying heat and compression, very large panels can be manufactured at exactly the same shapes and thicknesses. In an extrusion process, various profiles and concave fo...
Kunststoffe international, 2006-11-24, Optimum Ratio: Torque or Volume?
...bakery sector where very low energy input is needed. Because of the narrow flights, it is short, supported at two ends and has significant radial clearance. Current ZS-B side-feeders also have this Do/Di, since they have to convey large amounts of powder into the compounder with low torques. ZS-EG side-degassing units and ZS-EW side-dewatering units utilise this large Do/D to expel the large amounts of gas and water without entraining product. - The Continua, with a Do/Di of 1.71, that was devel...
Kunststoffe international, 2006-11-28, Practical Example: 6-Cavity Injection Mould for Transport Fasteners
Tooling. 6-Cavity Injection Mould for Transport Fasteners. Practical Example. This article describes which design-engineering details played a major role when configurating a metal powder injection mould for transport fasteners. To produce threaded transport fasteners in MIM technology, a standard mould (see also DIN ISO 12165:2002-06, Fig. 1) was selected. The six-cavity mould of Wilhelm Eisenhuth GmbH KG, Osterode/Germany is designed mainly with Z standard elements (manufacturer: Hasco Hasen...
Kunststoffe international, 2006-12-06, Polyetheretherketone: Material Advantages in Semiconductor Production
...aled that the critical quality factor that causes wafer defects is carrier particles that are formed at the point of contact between wafer and the carrier teeth. It is estimated that 20% of all foreign material defects are related to black powder from the carriers and boxes made with conventional carbon-powder-filled lower performance base-materials. The wafer carrier material should display excellent wear resistance, dimensional stability, high abrasion resistance to various surfaces, low parti...
Kunststoffe international, 2007-01-22, Complex Moulds for Foam
... have a particular shape so that the drawing remains within limits and preliminary trimming in the system is possible. Skins that are produced by slush moulding must also have the same contour at the edge to permit functional sealing of the powder box. At the same time, these surfaces must also be suitable for foaming, which particularly affects the all-round seals. These edges are subsequently separated from the part by a trimming operation. Here, too, not every method, such as stamping, milli...
Kunststoffe international, 2007-02-13, From Three-dimensional Cell Cultures to Contour-matching Mould Temperature Control
...rs the direct laser forming method affords the possibility of introducing almost any channel geometries seamlessly for contour-matching temperature control. This generative method allows mould inserts to be built up in one piece from an identical powdered material, for example from 1.2343 or 1.2083 tool steels. The basis for the contour pathways for the temperature control channels is determined for design purposes by 3D-CAD and if need be they can be optimised by Moldflow simulations before the...
Kunststoffe international, 2007-03-15, More Lightweight Construction for the BMW 3 Series Coupé and Convertible Models
... body oven for curing various adhesives in the body shell, on through cataphoretic dip painting for corrosion protection, in which a drying temperature of up to 195°C is attained, and extending to application of filler, cover coat and clear powder coating. Component Development In order to cope with the high temperatures occurring in the production sequence the rigidity of the material in question, a (PA+ABS) blend was evaluated by DMA (dynamic mechanical analysis) testing. The curve resulting...
Kunststoffe international, 2007-04-17, Ceramics Dressed as Plastics
Ceramics Dressed as Plastics Hybrid Parts Overmoulding of powder injection-moulded ceramic inserts opens up interesting possibilities for manufacturing plastics/ceramics hybrids on a large scale. This process was closely examined in a joint research project by the Süddeutsches Kunststoff-Zentrum (SKZ) and the Institute for Materials Research III at the Forschungszentrum Karlsruhe. Volker Piotter et al. The development of novel composites, in which the properties of different materials are ...
Kunststoffe international, 2007-04-17, Chalk – Much More than a Problem Solver
Chalk – Much More than a Problem Solver Sheet Production Adding calcium carbonate powder during recycling reduces the deposits of printing ink in the compounding plants. Recycling sheets’ qualities are improved and raw material costs reduced. Gerhard Gotzmann In the past, polypropylene (PP) and polyethylene (PE) films with a thick print have often been causing problems during recycling, since printing inks tend to deposit in the cutter compactor drum and the extruder. This led to the unfav...
Kunststoffe international, 2007-04-17, Hydraulics is High-Tech
...ns: Interkama, Factory Automation, Industrial Building Automation, MDA – Motion, Drive & Automation, Digital Factory, Subcontracting, Energy, Pipeline Technology, ComVac, SurfaceTechnology with Powder Coating Europe, MicroTechnology as well as Research & Technology. The 2007 Hannover Messe focuses on industrial automation, drive and fluid technology, energy technologies, industrial supplies and services as well as future technologies. The partner country at this year’s Hannover Messe is Turkey. ...
Kunststoffe international, 2007-04-17, Mechanical Engineering Tracking Materials Development
...ever, has been established by Cincinnati in which the screw outside diameter is coated with molybdenum while the barrel stays nitrided. Of the various molybdenum coating methods, plasma injection yields the best results. The molybdenum powder is introduced into the plasma at 15,000K, melted and sprayed onto the screw flights in extremely thin layers of about 7–8 µm (Fig. 5). Covering with many overlaps yields an accurate layer with extraordinary adhesion to the base material (Fig. 6), with the m...
Kunststoffe international, 2007-05-14, Customised Property Combinations
...category will undoubtedly be stand-up pouches, which have become established in a wide variety of sectors as a weight-saving, user-friendly alternative to glass and metal packaging. For packaging diverse products ranging from washing powders (Title picture), cosmetics, pet food and ready meals to medical devices (Fig.4), these universal packaging units are indispensable to everyday life. The optical and mechanical properties of the carrier film, for which specially customised polypropylene grade...
Kunststoffe international, 2007-05-14, Economical Production of Heat Sinks for LEDs
...nductive Compounds Lighting systems based on LEDs are being used ever more widely. Compact and rugged LEDs can be found everywhere today – whether in automotive headlights, street lamps, traffic signals or office and household lighting. A ceramic powder-filler polyamide 12 contributes to economical and cost-effective production of LED lighting. Luca Posca LEDs (light-emitting diodes) offer many advantages compared with conventional incandescent lamps. Besides low power consumption, they also ...
Kunststoffe international, 2007-06-18, Metal Injection Moulding at Micro Scale
...erials and, for a moulding process, its characteristic suitability for the production of large production runs together with efficient utilisation of the material. µ-MIM can produce parts with external diameters below 300µm. With very fine metal powders, structural details down to 10µm can be reproduced. The potential of the process is described below with reference to the production of a micromixer and a replica of the smallest human bone, the stirrup bone in the auditory canal. The micromixer ...
Kunststoffe international, 2007-07-18, Innovations for Medical Technology
... of the magnetic filler particles, which forms the basis for the magnetization, is also combined with other processes, such as micro and/or multicomponent injection molding. Robust Process Integration in Ceramic Injection Molding Powder injection molding (PIM) combines the advantages of ceramic and metal materials in the application with the production advantages of injection molding. As product, solid bodies, e.g. of zirconium oxide or aluminum oxide ceramics are produced, as well as low-allo...
Kunststoffe international, 2007-07-18, Product Design Tailored to Patients
...eets. The high filler content makes it cool to the touch, with haptics that come very close to those of a mineral material. Virtually original metal or ceramic properties in respect of thermal conductivity can be achieved through powder injection molding. This involves the use of granules made up of plastics, very fine metal or ceramic powders, and a number of additives. The parts receive their metal or ceramic properties after the plastic matrix has been debindered and a sintering operation ha...
Kunststoffe international, 2007-07-18, Resorbable Implant Containing Medication
...lanning. In addition to its ability to produce microcellular foam structures, the CESP process is characterized by processing of material at low temperatures that are gentle on the medication. With this process, the resorbable polymer in the form of powder is exposed to a high-pressure carbon dioxide atmosphere in an autoclave. As soon as the polymer has become saturated with carbon dioxide, the pressure in the autoclave is reduced in a controlled manner. The resultant supersaturation of the pol...
Kunststoffe international, 2007-08-14, New Structure Bears Fruit
...from all other companies in the Reifenhäuser Group. Complete one-source product solutions characterize its business philosophy. The armoring alloys required for hard facing, for example, are produced on the company’s in-house powder atomization plant. Then in our partially self-developed and designed plant, a wear-resistant layer of metal powder is arc-welded onto the screw and cast centrifugally in the barrel. In mid-2006 an additional centrifugal caster was commissioned. The "PSM 6000"...
Kunststoffe international, 2007-09-19, A Design Tailored to Requirements
...ith the Kunststoff-Zentrum in Leipzig, can produce moldings weighing less than 0.28 mg with a high precision and in a high optical quality. It is suitable for processing all current thermoplastics and also for metal and powder injection molding. Conclusion One thing is certain: the machine builders are (as usual, it almost has to be said) exhibiting a broad range of machines and concepts. It will be necessary to wait until after the exhibition, however, to see which of the innovations and impr...
Kunststoffe international, 2007-09-19, Basis of Product Quality
... with gentle transport by means of pneumatic conveyor systems ensures a largely troublefree production routine on the part of materials supply – and this is the case not only for large processing companies. A complete range of conveyor systems for powders and granulated materials is available from Pelletron Corporation, Lancaster, Pennsylvania, USA. Apart from high- and low-pressure sluices as well as pipe junctions and mixers, the specially developed and patented Pellbows pipe bends prevent the...
Kunststoffe international, 2007-09-19, Face Lifts for Molded Parts
...lexibility control. Robustness, flexibility and precise control of the blade are its main features. Matex is represented in Germany by Dipl.-Ing. Günter Staschik in Menden. Not only can flowable compounds be coated, but for particular applications powder material can also be applied. Rolf Schlicht GmbH, Hamburg, Germany, has developed the RSC electrostatic power applicator for the uniform, finely controlled, dust free dosing of powder onto cable, wire, hoses and profiles. Due to the electrostati...
Kunststoffe international, 2007-09-19, Great Achievements in any Respect
...e of extrusion lines (Fig. 12). Schlicht downstream equipment shows excellent accuracy of trim and tolerances, as well as accurate cut-section. In addition, the enterprise is going to show its RSC model of an electrostatic powdering machine. The equipment is suited to powder cables, wires, tubes and profiles at diameters between 0.5 and 120 mm with talcum, stearate, varnish powder, swellable powder etc. With RSC, powdering is effected homogeneously, can be dosed finely and is absolutely free of ...
Kunststoffe international, 2007-09-19, It’s the Mixture that Counts
...harged both with polymers as well as all sorts of additives. This requires flexible and dependable metering systems. The K-Tron Process Group of Pitman, New Jersey, USA, is introducing various gravimetric metering units for charging extruders with powder and pellets. The Micro Cone metering unit with its conical, rotating tube is well-suited for very small throughputs of 0.02 to 6dm3/h (Fig.1). Brabender Technologie KG of Duisburg, Germany, is introducing a new version of the ScrewDisc type feed...
Kunststoffe international, 2007-09-19, Prior to Film Extrusion
...nces in the polymer matrix, so that plant technology can be kept as simple as possible. As color and additive masterbatches are available in granular form, simpler material handling systems can be used than would be the case with base materials in powder form. Evidence for this is found in the increased use of batch feeding in extrusion lines. Manufacturers in the materials handling business are required to cover an extensive range of know-how. Amongst others, this includes expertise in their ow...
Kunststoffe international, 2007-09-19, Rare Earth Metal Stabilizers: Appearance and Reality
Rare Earth Metal Stabilizers: Appearance and Reality PVC Stabilizers For some years now, samples of PVC stabilizers based on rare earth metals and their compounds have been turning up in Europe. They are being talked of as heavy-metal-free alternatives to the European systems based on calcium-zinc or organic substances. This article aims to present a realistic picture of rare earth metal stabilizers to set against the advantages that are often claimed for them as a result of inadequate infor...
Kunststoffe international, 2007-09-19, Versatile Material with Unlimited Potential?
...new aromatic thermoplastic polyurethane (TPU) known as Desmopan DP 3790AP for this technology. The material is used for molded skins that are post-coated as well as for a new process, in which an in-mold coating (IMC) step precedes the actual powder slush molding (IMC-TPU-slush). The international system supplier, Intier Automotive Interiors, a member of the Magna International group, developed this process jointly with the OEM and coating supplier. According to the manufacturer, the new materia...
Kunststoffe international, 2007-10-21, Polyaryletherketones (PAEK)
...K in four melt viscosities and a vast range of fillers and compositions, as well as several grades of PEEK-HT. This product range of over forty grades consists of granules for standard thermoplastic processing as injection molding and extrusion, powders for compounding and fine powder grades for compression molding and fiber impregnation technologies. Market Development and Production Capacities Victrex is still the world’s largest manufacturer of PAEK with nearly thirty years of experience. N...
Kunststoffe international, 2007-10-21, Polyoxymethylene (POM)
...; and thus places the same stringent requirements on the plastics used and on their raw materials as on the drugs. AC-Pharma AG, Strasslach, Germany, for example, uses an MT variant of POM for the dosing ball and flap of a dry powder inhaler (Fig. 3). The innovative breath-controlled dry powder inhaler offers unique protection against overdosing and duplicate administration. Alongside the accurate release and palpable supply of the precise quantity of active ingredient, it is also a matter of pr...
Kunststoffe international, 2007-11-21, Surface Finishing in the Cockpit
.... Apart from its "adhesive effect" the latter also assumes the function of compensating for thickness tolerance and exerts a damping action in the system. Typical examples include: - Complex multilayer parts having mold skin surfaces such as powder slush, RIM skin and spray skin with or without in-mold painting, and - Film- or leather-laminated components having an intermediate layer composed of expanded foam or textile (Fig. 2). Circumstances are somewhat different in the following two ...
Kunststoffe international, 2007-12-17, Technology being Consolidated
...and heat so that the residual plastic content melts and in this way renders the panel resistant to weathering and aging. Waste tire granules can also be processed in similar fashion and compressed with an upper and lower covering layer of recycled powder. Technologically, the company is putting its trust in the ContiRoll pressure and temperature control system which is equipped with two circulating steel bands in the heating and cooling zone. Pressure and temperature are transferred more uniform...
Kunststoffe international, 2007-12-17, Unlimited Versatility and Design
...nveyor belts, Bayer MaterialScience works together with Belgian plastic refiner, Dakota Coatings, on thermoplastic polyurethanes (TPU). Low-melting Desmopan, in particular, is applied to engineering fabric webs by means of the powder sintering process. The TPU is compounded by Dakota Coatings together with coloring agents and additives and processed into fine powders through cold grinding. It is also marketed under the name of Dakotex. The concept for the rear bumper on the extravagant Audi R8 (...
Kunststoffe international, 2008-01-15, Complete Solutions Sought
...andle extremely abrasive materials. In addition, Koch has added a patent-pending double mixer to its range of products. It is claimed to effectively counteract the tendency of bulk materials with components having different bulk densities, e.g. powder, pellets, film scrap, dusty reclaim or wood flour, to separate. The mixer operates with horizontally intermeshing reciprocating and rotary motions that convey the material upwards. To complement its existing line of robot systems, Wittmann introduc...
Kunststoffe international, 2008-01-15, Elastomer Industry Has Understood
...f ingenious mold technology and an interposed MuCell unit (licensed from Trexel Inc., Woburn, USA). Here, the P-Group made use of its longstanding experience with Pibiflex grades for the powder-slush process, which also requires extremely easyflowing formulations to overcome the sometimes lengthy flow paths typical of slush molded components. The surface requirements, too, are practically identical. Another complex production process was demonstrated on the Krauss Maffei stand throughout K2007. ...
Kunststoffe international, 2008-02-17, Doping for Masterbatch Production
...common feature of these masterbatches is that they consist of a polymer carrier, which contains a concentrated liquid or solid additive. In solid additives, a distinction is made between non-melting and melting substances. Compounding of non-melting powder additives does not usually differ from the method for powder solids such as minerals. The incorporation of additives into the carrier material is known as dispersion. The aim is to minimize the particle size and subsequently distribute it homo...
Additional information about this tradename, like producer contact address, etc. can be found at www.materialdatacenter.com. For access to this extra information a registration is requested. Free online registration is available.
Note: the information in Material Data Center was collected with maximum care, based on information from material producers. They are subject to short term changes at the market. There is no warranty for the correctness of this information. In no way this information can be seen as a legal advice, whether certain tradenames are protected or not.